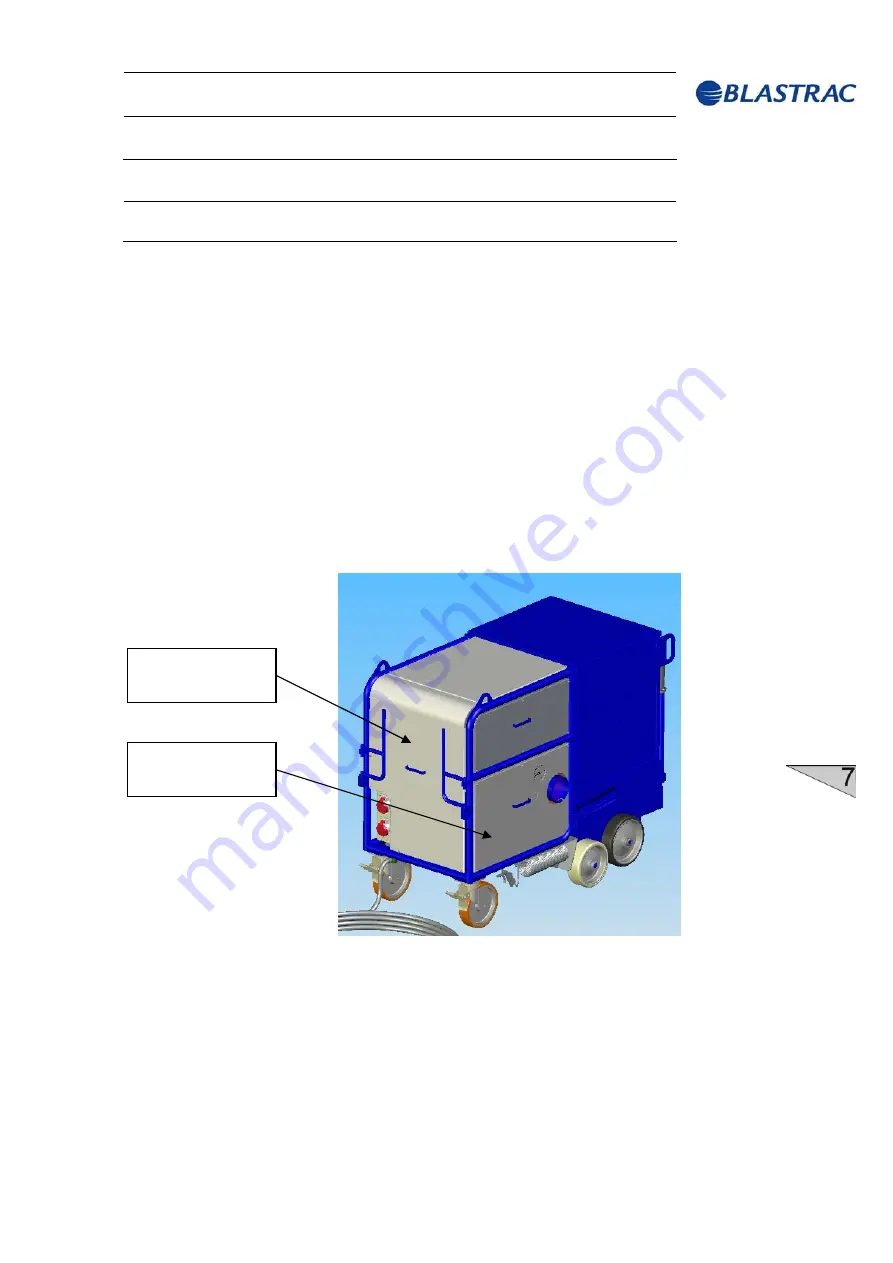
655DC Operating
Instructions
Maintenance
5
7.4 The
V-belts
The V-belt drive is designed for the installed driving power. To force a
higher output through an excessive high tension of the V-belt will
break the belt, damage bearings and cause losses of the total
efficiency. Too low belt tension will cause slipping with the result of a
very high temperature of the V-belt a premature destruction of it.
Temperatures over 70° for a longer period will decrease the working
life and the efficiency of the V-belt. The grooves of the V-belt pulleys
must be free of rust, fat and dirt and must not show any damages.
The use of belt wax or similar substances in order to increase the
friction coefficient is not necessary and it damages the V-belt. Soiling
due to oil, grease or chemicals have to be avoided.
In order to get perfect power transmission the V-belt drive has to be
checked regularly.
The V-belt drive is located behind the Compressor panel.
The V-belt tension device is located behind the Left lower panel.
Compressor
panel
Left panel
lower
Fig.7.4.1
Summary of Contents for 655DC
Page 1: ...Operating Instructions 655DC MAN 655DC EN...
Page 2: ......
Page 4: ......
Page 10: ...Operating Instructions 655DC Technical data 6...
Page 29: ...655DC Operating Instructions General 7 Fig 3 3...
Page 30: ...Operating Instructions 655DC General 8...
Page 34: ...Operating Instructions 655DC Transport 4...
Page 40: ...Operating Instructions 655DC Initial operation 6...
Page 48: ...Operating Instructions 655DC Operation 8...
Page 66: ...Operating Instructions 655DC Maintenance 18...
Page 68: ...Operating Manual 655DC Electrical systems 2 8 1 Electric circuit diagrams 655DC EC version...
Page 69: ...655DC Operating Instructions Electrical systems 3...
Page 70: ...Operating Manual 655DC Electrical systems 4...
Page 71: ...655DC Operating Instructions Electrical systems 5...
Page 72: ...Operating Manual 655DC Electrical systems 6...
Page 73: ...655DC Operating Instructions Electrical systems 7...
Page 74: ...Operating Manual 655DC Electrical systems 8...
Page 75: ...655DC Operating Instructions Electrical systems 9...
Page 76: ...Operating Manual 655DC Electrical systems 10...
Page 77: ...655DC Operating Instructions Electrical systems 11...
Page 78: ...Operating Manual 655DC Electrical systems 12 8 2 Electric circuit diagrams 655DC UL version...
Page 79: ...655DC Operating Instructions Electrical systems 13...
Page 80: ...Operating Manual 655DC Electrical systems 14...
Page 81: ...655DC Operating Instructions Electrical systems 15...
Page 82: ...Operating Manual 655DC Electrical systems 16...
Page 83: ...655DC Operating Instructions Electrical systems 17...
Page 84: ...Operating Manual 655DC Electrical systems 18...
Page 85: ...655DC Operating Instructions Electrical systems 19...
Page 86: ...Operating Manual 655DC Electrical systems 20...
Page 91: ...655DC Operating Instructions Spare parts 1 Contents Chapter 10 10 1 Spare parts...
Page 94: ...Operating Instructions 655DC Spare parts 4 Fig 10 2...
Page 96: ...Operating Instructions 655DC Spare parts 6 Fig 10 3...
Page 98: ...Operating Instructions 655DC Spare parts 8 Fig 10 4...
Page 100: ...Operating Instructions 655DC Spare parts 10 Fig 10 5...
Page 102: ...Operating Instructions 655DC Spare parts 12 Fig 10 6...
Page 104: ...Operating Instructions 655DC Spare parts 14 Fig 10 7...
Page 106: ...Operating Instructions 655DC Spare parts 16 Fig 10 8...
Page 108: ...Operating Instructions 655DC Spare parts 18 Fig 10 9...
Page 110: ...Operating Instructions 655DC Spare parts 20 Fig 10 10...