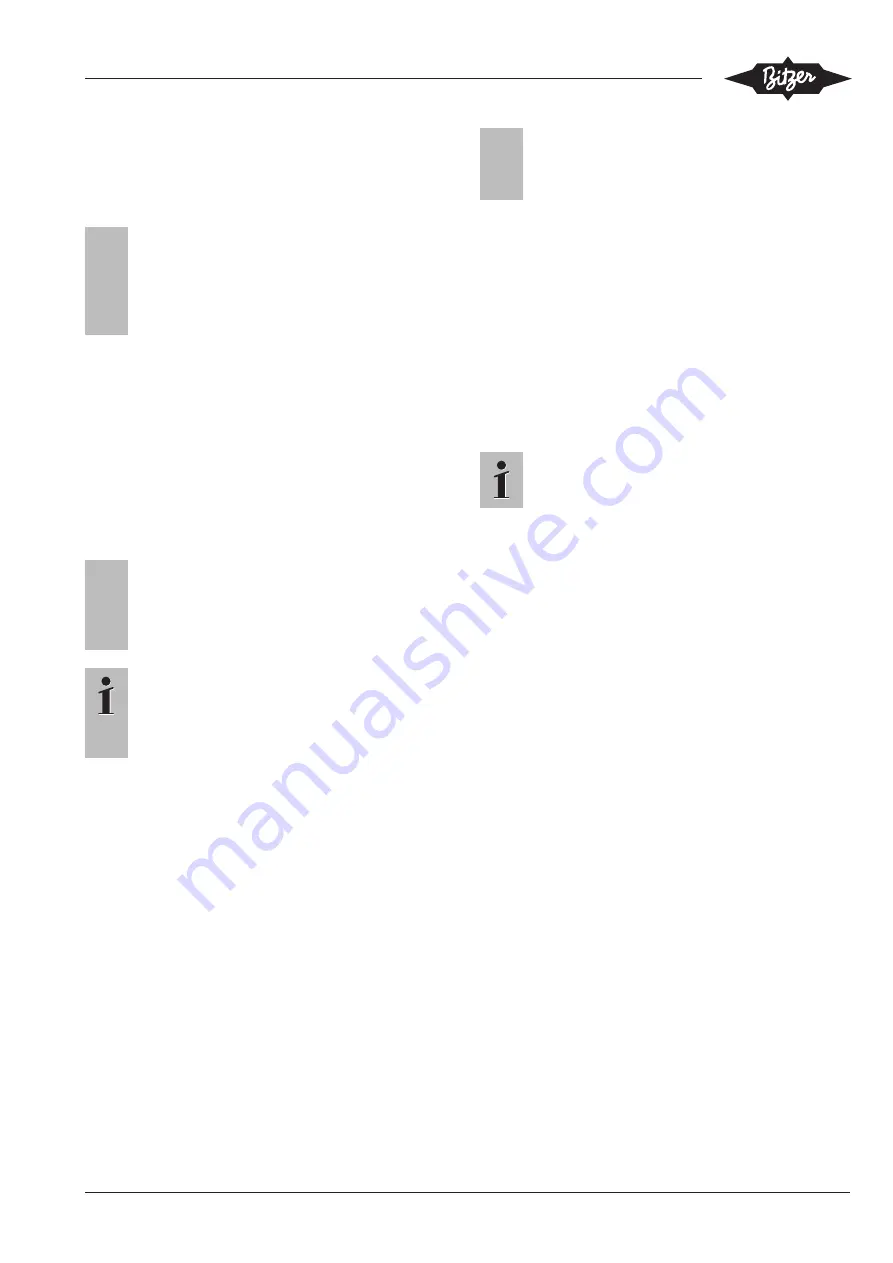
SB-520-2
25
4.4.1
Pipe connections
The pipe connections are designed in such a way that
they are suitable for pipes in all common dimensions in
millimetres and inches.
!
!
NOTICE
Do not overheat the shut-off valves!
Cool the valve body and the welding adapter
during and after the welding operation.
For welding, dismount the pipe connections and
the bushes.
4.4.2
Pipelines
Use only pipelines and system components which are
clean and dry inside (free from slag, swarf, rust and
phosphate coatings) and which are provided with an
air-tight seal on delivery.
As standard, the compressors are supplied with blank-
ing plates on the pipe connections. These must be re-
moved before performing the strength pressure and
tightness tests and commissioning the system.
!
!
NOTICE
For systems with rather long pipelines or for
welding operations without protective gas:
Install the suction-side cleaning filter (mesh size
< 25 μm).
Information
The blanking plates are only designed to serve
as a transport protection. They are not suitable
as a separation between different system sec-
tions during the strength pressure test.
!
!
NOTICE
Risk of compressor damage!
Evacuate the system and flush it once or sev-
eral times with dry nitrogen, if necessary.
Mount pipelines in such a way that the compressor is
protected from flooding with oil or liquid refrigerant dur-
ing standstill. Strictly observe the instructions indicated
in the manual SH-510.
Lines for economiser (ECO) and liquid injection (LI):
The ECO connection is arranged on the top side of the
compressor housing, therefore a bridge for protection
against oil migration is not required. Guide the line hori-
zontally or downwards from the connection. See Tech-
nical Information ST-600.
When retrofitting the ECOshut-off valve:
Information
To increase the corrosion protection, it is recom-
mended to paint the ECO shut-off valve.
4.4.3
Connecting the high pressure switch (HP)
Remove the Schrader internal valve part and the brass
Schrader screwed nipple from position 1 (HP) and con-
nect the high pressure switch there.
4.4.4
OSKAB (booster version)
An external oil pump may be necessary in systems
where a sufficient oil pressure difference cannot be
built up directly after the compressor start. This may
apply, for example, to large parallel compounding sys-
tems with extremely low condensing temperature or to
boosters.