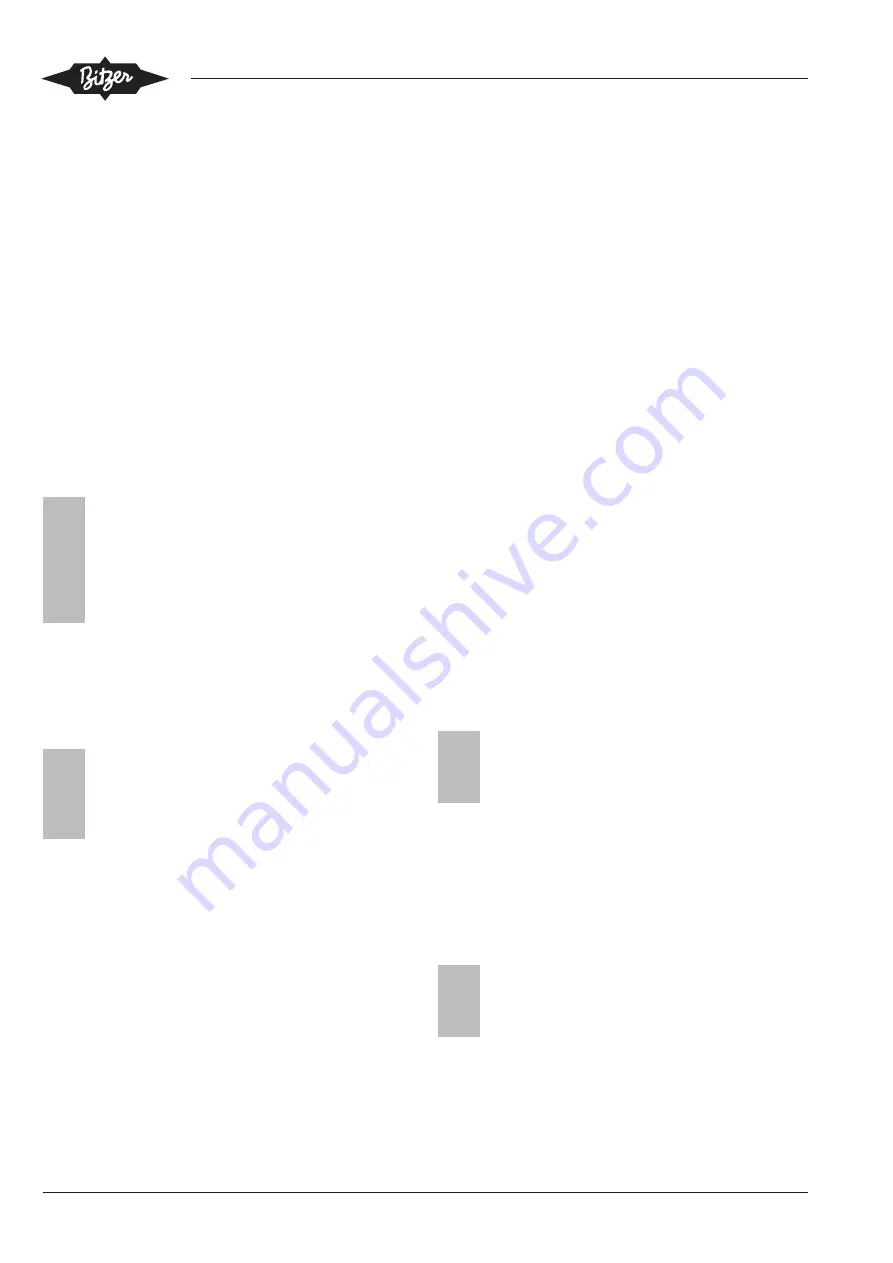
SB-520-2
30
6.7.2
Start
Restart, slowly open the suction shut-off valve and ob-
serve the sight glass in the oil injection line. If there is
no oil flow within 5 s, switch off immediately. Check oil
supply!
6.7.3
Checking the oil level
Immediately after commissioning, carry out the follow-
ing checks:
• During operation, the maximum and recommended
oil level is within the sight glass area of the oil separ-
ator (the minimum oil level is secured by the oil level
switch).
• During the start phase, oil foam may appear which,
however, should decrease after 2 to 3 min. Other-
wise high proportions of liquid in the suction gas are
suspected.
!
!
NOTICE
Risk of wet operation by charging liquid refriger-
ant!
Measure out extremely precise quantities!
Maintain the discharge gas temperature well
above the condensing temperature:
with NH
3
at least 30 K.
If the oil level switch is triggered during the start phase
of the oil monitoring system or after the delay time has
elapsed (10 s), this indicates an acute lack of oil. This
may be caused by a too large share of refrigerant in the
oil. Check the suction gas superheat.
!
!
NOTICE
Risk of compressor failure due to liquid slug-
ging!
Before adding larger quantities of oil: check the
oil return!
6.7.4
Setting high pressure and low pressure
switches (HP + LP)
Perform a test to check the exact cut-in and cut-out
pressure values according to the application limits.
6.7.5
Setting the condenser pressure control
▶ Set the condenser pressure so that the minimum
pressure difference is reached within 20 s after the
start.
▶ Avoid quick pressure reduction with finely stepped
pressure control.
6.7.6
Checking the operating data
• Evaporation temperature
• Suction gas temperature
• Condensing temperature
• Discharge gas temperature:
– Min. 30 K (NH
3
) above condensing temperature
– Max. 100°C
• Oil temperature:
– Reniso KC68, Reflo 68A, SHC226E: max. 60°C
• Cycling rate
• Motor current
• Motor voltage
• For operation with ECO:
– ECO pressure
– Temperature at the ECO connection
• Creation of data protocol
For application limits, see brochure SP-520 or
BITZER SOFTWARE.
To prevent motor failures, the following requirements
are specified:
• Maximum cycling rate, motor current, motor voltage:
Observe the notes of the motor manufacturer.
• Desirable minimum running time: 5 min
!
!
NOTICE
Risk of motor failure!
The specified requirements must be ensured by
the control logic!
6.7.7
Vibrations
When operating with frequency inverter, check the en-
tire speed range of the system for abnormal vibration.
Speeds at which resonances still occur must be
avoided in the programming of the frequency inverter. If
required, take additional safety measures.
!
!
NOTICE
Risk of burst pipes and leakages on the com-
pressor and system components!
Avoid strong vibrations!