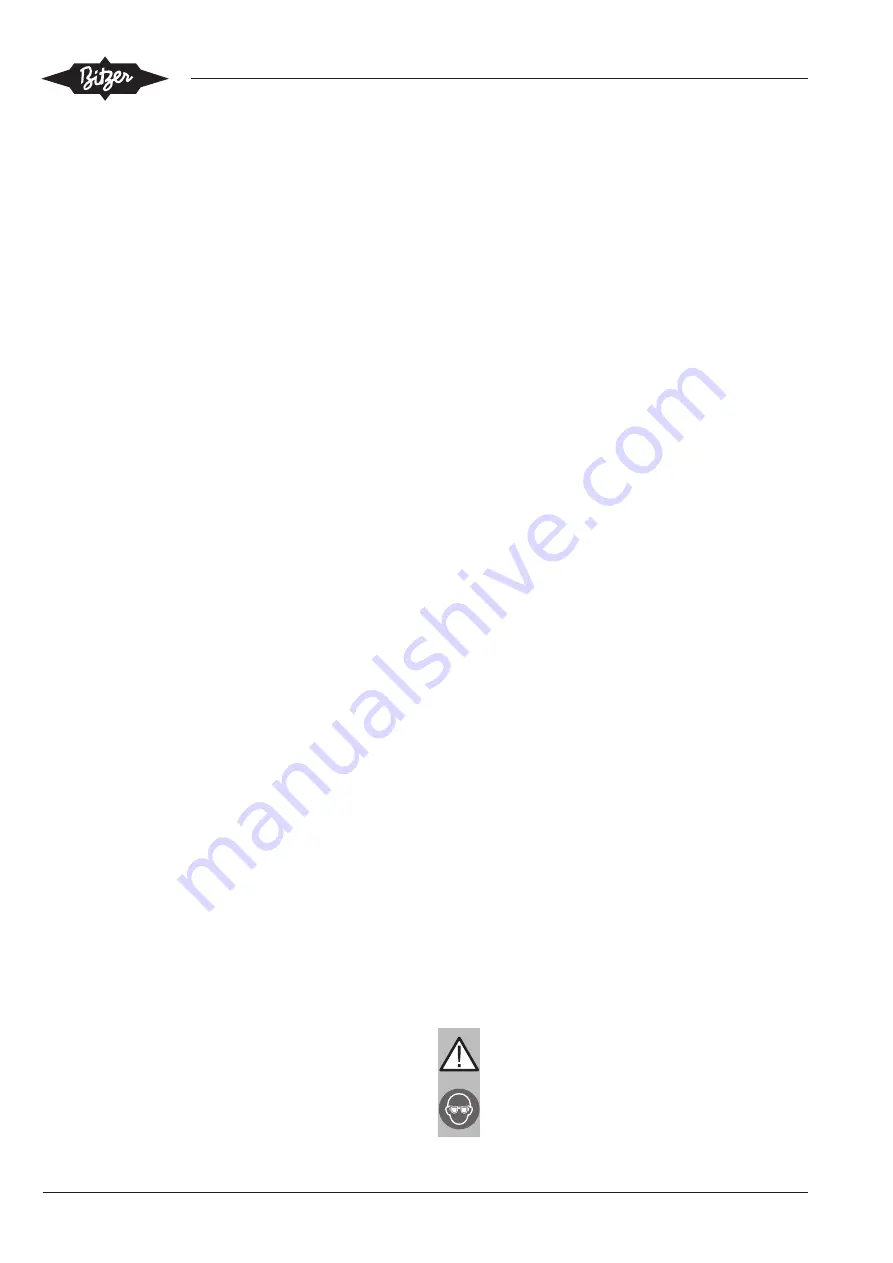
ESB-130-8
38
– If possible, insulate the sensor to ensure it meas-
ures the suction line temperature and not the am-
bient temperature.
– Sufficiently high suction gas superheat. A too high
setting of the suction gas superheat of the valves
results in high discharge gas temperatures, re-
duced cooling capacity and poor oil return. A too
low suction gas superheat may cause liquid slug-
ging and compressor bearing washout.
– When using electronic expansion devices, enabel-
ing the MOP (maximum operating pressure) fea-
ture is recommended to avoid overloading of the
compressor.
– Stable operating mode under all operating and
load conditions (also part-load, summer/winter op-
eration, minimum speed during VSD operation).
– Solid liquid at the expansion valve inlet.
• Avoid refrigerant migration (from the high-pressure
side to the low-pressure side or into the compressor)
during long shut-off periods!
– Install the solenoid valve in the liquid line.
– Automatic pump down system before any off
cycle (especially if the evaporator may get warmer
than the suction line or the compressor) as long
as the pressures are within the application limits.
– Install a sufficiently sized suction accumulator to
prevent liquid slugging during liquid floodback
when starting the compressor.
– Observe the low-pressure limit.
– Automatic sequence change for systems with sev-
eral refrigerating circuits.
– An oil heater is generally recommended, but must
be used in the following applications and under
the following conditions: Systems with reverse
cycling (e.g. hot gas defrosting), outdoor installa-
tion and in cases in which the compressor can be-
come colder than other system components. Split
systems equipped with extended pipe work.
– Switch the oil heater on at least 12 hours before
starting the compressor. This prevents oil dilution
and bearing load when starting the compressor
for the first time. The oil heater must be energized
during off cycles.
• For reverse cycling
– First switch the compressor off
– Wait for 30 seconds
– Then start the compressor
7
Operation
7.1
Regular checks
Examine the system at regular intervals according to
national regulations.
• Cleanness and traces of corrosion on the com-
pressor housing.
• Operating data, see chapter Checking the operating
• Oil supply, see chapter Lubrication / oil level monitor-
• Safety and protection devices and all components
for compressor monitoring, see chapter Protection
devices, page 34 and see chapter Compressor start,
page 37.
• Tight seat of electrical cable connections and
screwed joints.
• Refrigerant charge.
• Tightness
• Prepare data protocol.
8
Maintenance
8.1
Oil change
The oil used by BITZER (see chapter Application
ranges, page 24) is characterised by its high degree of
stability. An oil change is generally not required when
appropriate suction-side fine filters are mounted or
used.
In case of compressor or motor damage, it is recom-
mended performing an acid test. If necessary, carry out
cleaning measures: Fit an acid retaining suction line
gas filter and change oil. If necessary, change filter and
oil again after several operating hours.
Compressors of the ORBIT series can be used as re-
placement compressor in systems, which have previ-
ously been operated with compressors with POE
charge. Provided that the correct compressors and di-
mensions have been selected, a residual oil content of
up to 10% is allowed in the system.
WARNING
The compressor is under pressure!
Serious injuries are possible.
Depressurize the compressor!
Wear safety goggles!