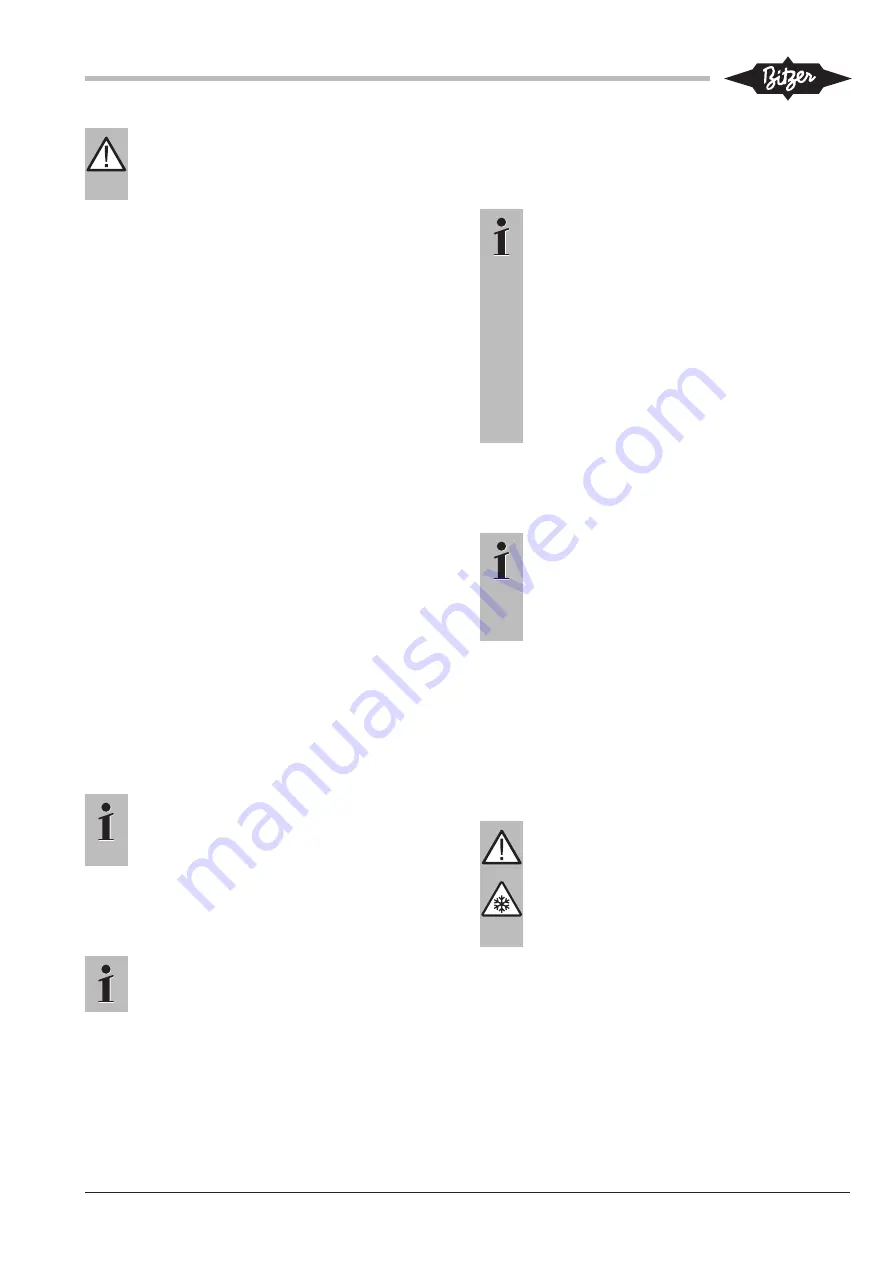
KB-130-7
11
WARNING
Induction, electric voltage!
Never operate the motor with the terminal box
open!
When the rotor rotates, electric voltage is induced in
the terminal pins – even with the motor switched off.
Permitted work on a compressor with LSPM motor
Work on the electric supply and screw fixings in the ter-
minal box, oil change as well as inspection and re-
placement of pressure relief valves, cylinder banks and
sight glass. No special tools are needed for this work.
Before opening the compressor, thoroughly clean its
environment. Pay special attention to loose metal
particles! Do not open the motor cover!
5.1
Overload protection for LSPM motors
The PTC temperature sensor integrated in the stator as
a standard protects the LSPM motor from overload
when the temperature rises (e. g. in case of prolonged
locked rotor conditions). It is recommended installing
an additional overload protective device that reacts
more quickly, since repeated locking conditions would
damage the magnets. Be sure that it is properly sized
to ensure quick protection against serious electrical
faults below the trigger level of the compressor fuse.
For example, an overload relay with adjustable time or
thermal overload switch may be selected.
• Allowed current values and durations:
– Starting: max. 0.5 s (1.25 x LRA)
– Operation: max. 2 s (1.25 x max operating cur-
rent)
Information
Manual reset of compressor protection devices
must not be changed to automatic reset by us-
ing external measures!
6
Commissioning
Information
General information and requirements, see op-
erating instructions KB-104.
Prior to putting the system into operation, check all
safety and monitoring devices of the system and in the
machine room for correct function.
The following information must also be available:
• Construction data.
• Maximal admissible pressures at standstill and dur-
ing operation.
• Pipelines and instruments diagram.
Information
Special care is required when commissioning
CO
2
compressors for transcritical applications.
Due to the high solubility of refrigerant in oil, the
high pressure levels and strong pressure vari-
ations after the starting process, overload and
lack of lubrication may occur.
It is therefore necessary to observe thoroughly
the working behaviour and the operating condi-
tions and to switch off the compressor(s) tem-
porarily in case of abnormal conditions.
Supervise the system during the whole commis-
sioning process!
6.1
Evacuation
• Switch on the oil heater.
Information
For applications with CO
2
, the "standing va-
cuum" should reach a value of 0.67 mbar
(500 microns) before the commissioning.
During the evacuation process, break the va-
cuum several times with dry nitrogen.
6.2
Charging refrigerant
The following chapter describes general requirements
when filling with refrigerant and the commissioning of
the compressors. Depending on the version and the
control system of the plant (e.g. for systems with inter-
mediate pressure receivers or booster), some adapta-
tions may be necessary.
DANGER
Liquid CO
2
evaporates quickly, cools down at
the same time and forms dry ice!
Danger of cold burns and frost bites!
Avoid uncontrolled deflating of CO
2
!
When filling the system with CO
2
, wear gloves
and goggles!
• When extracting CO
2
out of a bottle without ascend-
ing pipe, use a pressure reducer! In general, also
after service work, always break the vacuum with
gaseous CO
2
.
• For CO
2
bottles with ascending pipe, only extract
high-pressure liquid! Do not use a pressure reducer!
The membranes of the pressure reducers are not
completely sealed against liquid penetration.