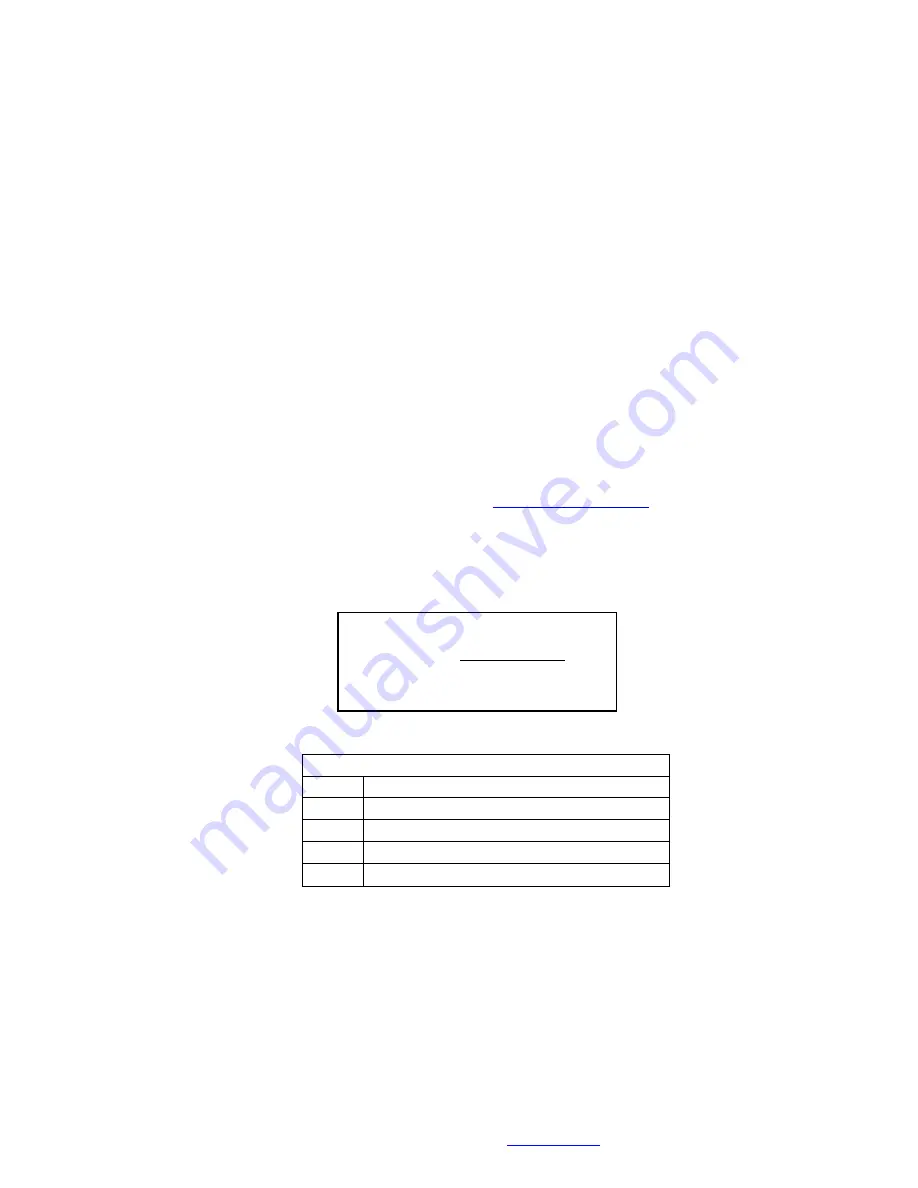
Binsfeld Engineering Inc. | 231-334-4383
www.binsfeld.com
869500-9_G Pg. 33
load close to those expected during testing. At a minimum, they
should represent at least 10% of the range.
Shunt Calibration
The more common method is to perform a shunt calibration. This
method takes into account deviations in the setup from the strain
gage to the transmitter, but unlike a deadweight calibration, none
of the deviations in the physical parameters.
The easiest way to conduct a shunt calibration is by enabling one
of the reference shunt resistors on-board the TX10K-S. An
internal precision resistor is placed in parallel with one arm of the
bridge to simulate a precise strain value. As stated earlier,
Reference 1 simulates 100 microstrain (µe) and Reference 2
simulates 500 µe when using a 350Ω strain gage with a Gage
Factor of 2.0. Alternatively, precision resistors can be placed in
parallel with one arm of the bridge to simulate a torque load. The
Tech Info section on our website (
www.binsfeld.com
) has a helpful
Torque Strain Calculator to assist in determining the strain a given
resistor value simulates. The equation relating strain and shunt
resistance is shown below:
Legend of Terms
R
C
Shunt Calibration Resistance (k
Ω)
R
G
Gage Resistance (
Ω)
N
Number of Active Gages
GF
Gage Factor
ε
Strain (
µe)
In the example from Steps 1 & 2, the Full Scale Torque is 4,901 ft-
lb and the RX10K output has been scaled so that 10 V
corresponds to a torque load of 5,000 ft-lb by setting the System
Gain to 3920. This was determined by multiplying the Transmitter
Gain of 4000 (±500 µe range) by the Scale Factor (Z) that was
calculated to be 0.9802.
R
G
R
C
=
(N)(GF)(
ε)