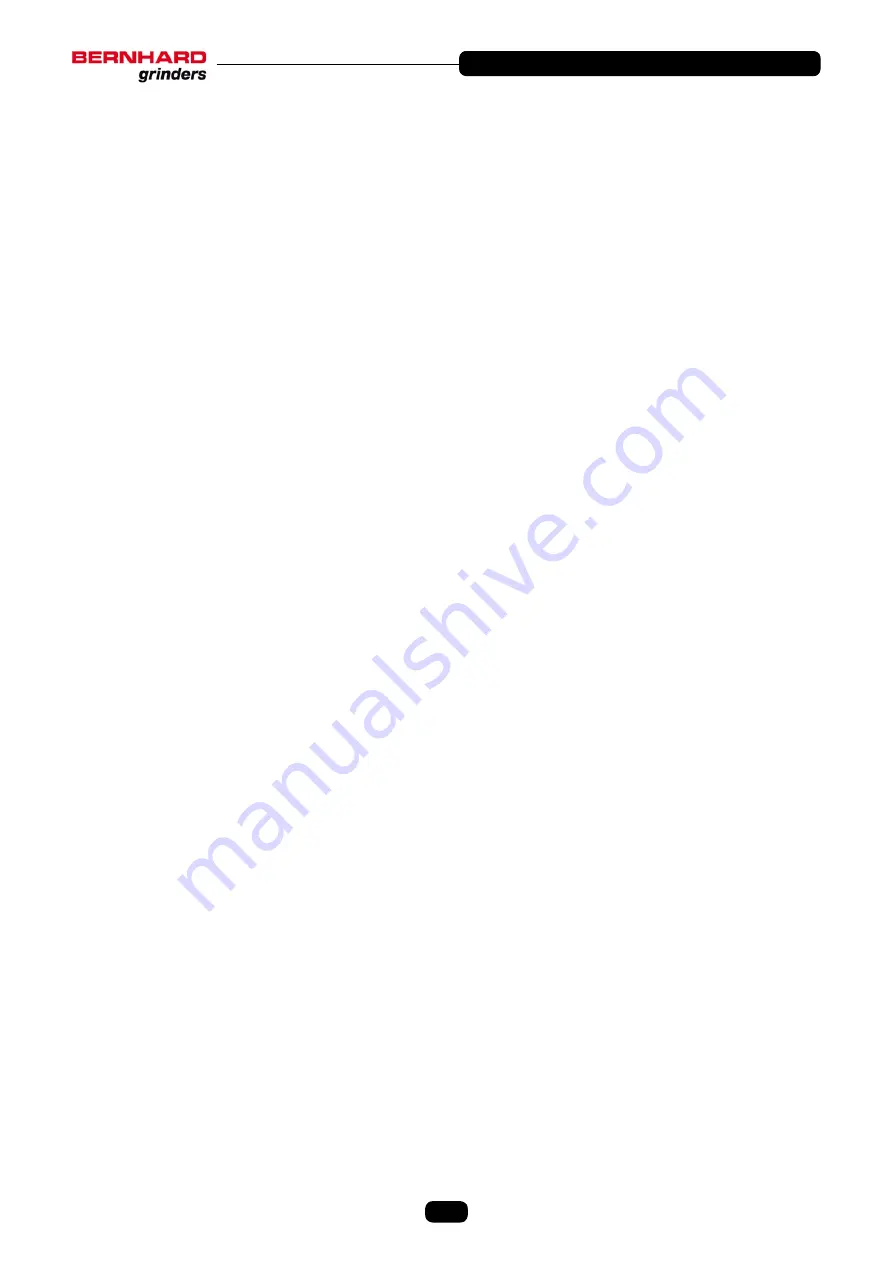
EXPRESS DUAL • ED2000
© Bernhard and Company Limited
6
EXPRESS DUAL • ED2000
© Bernhard and Company Limited
7
2.1 This machine is designed and manufactured
ONLY
for grinding lawn mower reels, rollers,
groomers and verticut units, and
MUST NOT
be used for any other purpose.
2.2 This machine should be installed, operated and maintained by competent personnel who
have received adequate training.
2.3 Before carrying out any work on the machine, other than grinding,
ALWAYS SWITCH OFF
the main electrical supply, or remove the power lead from its socket.
2.4
ALWAYS
operate the machine with the guards in position.
2.5
NOISE
- Owing to the widely varying conditions of use, noise emissions may vary
considerably. There may be occasions when the safe noise level may be exceeded (see
note on noise emission). In this case adequate ear protection
MUST
be worn.
2.6
NEVER
fit or use a grinding wheel (or other spares) other than those supplied specifically
for use on the
EXPRESS DUAL
(Warranty will be invalidated).
2.7
NEVER
fit or use a grinding wheel which has been dropped or subjected to any other form
of abuse.
NOTE:
Grinding wheels should be fitted
ONLY
by competent, trained personnel.
2.8
NEVER
leave rags or tools on the machine or wear any loose clothing or other articles
which could be caught in moving components.
2.9
NEVER
allow any combustible materials to be placed on or around the machine.
2.10
ALWAYS
ensure that all parts of the cutting unit being ground are securely fixed.
2.11
ALWAYS
ensure that all electrical connections are sound and all cables are safely routed.
2.12
ALWAYS
carry out cleaning and maintenance of the machine as instructed in this manual
(Refer to safety note 1.3).
2.13
STAY ALERT
. Watch what you are doing.
NEVER
operate the machine when tired, or
under the influence of drugs or alcohol.
If a lift table is fitted
NEVER
attempt to lift in excess of the rated capacity, and always
ensure that the area is clear before lowering the load.
2. Safety
Summary of Contents for EXPRESS DUAL ED2000
Page 2: ...EXPRESS DUAL ED2000 Bernhard and Company Limited 2 NOTES...
Page 29: ...EXPRESS DUAL ED2000 Bernhard and Company Limited 29 1 2 3 4 9 5 6 8 10 7 FEED ASSEMBLY...
Page 37: ...EXPRESS DUAL ED2000 Bernhard and Company Limited 37 1 2 3 4 5 6 7 8 9 10 GUARD...
Page 38: ...EXPRESS DUAL ED2000 Bernhard and Company Limited 38...
Page 39: ...EXPRESS DUAL ED2000 Bernhard and Company Limited 39 NOTES...