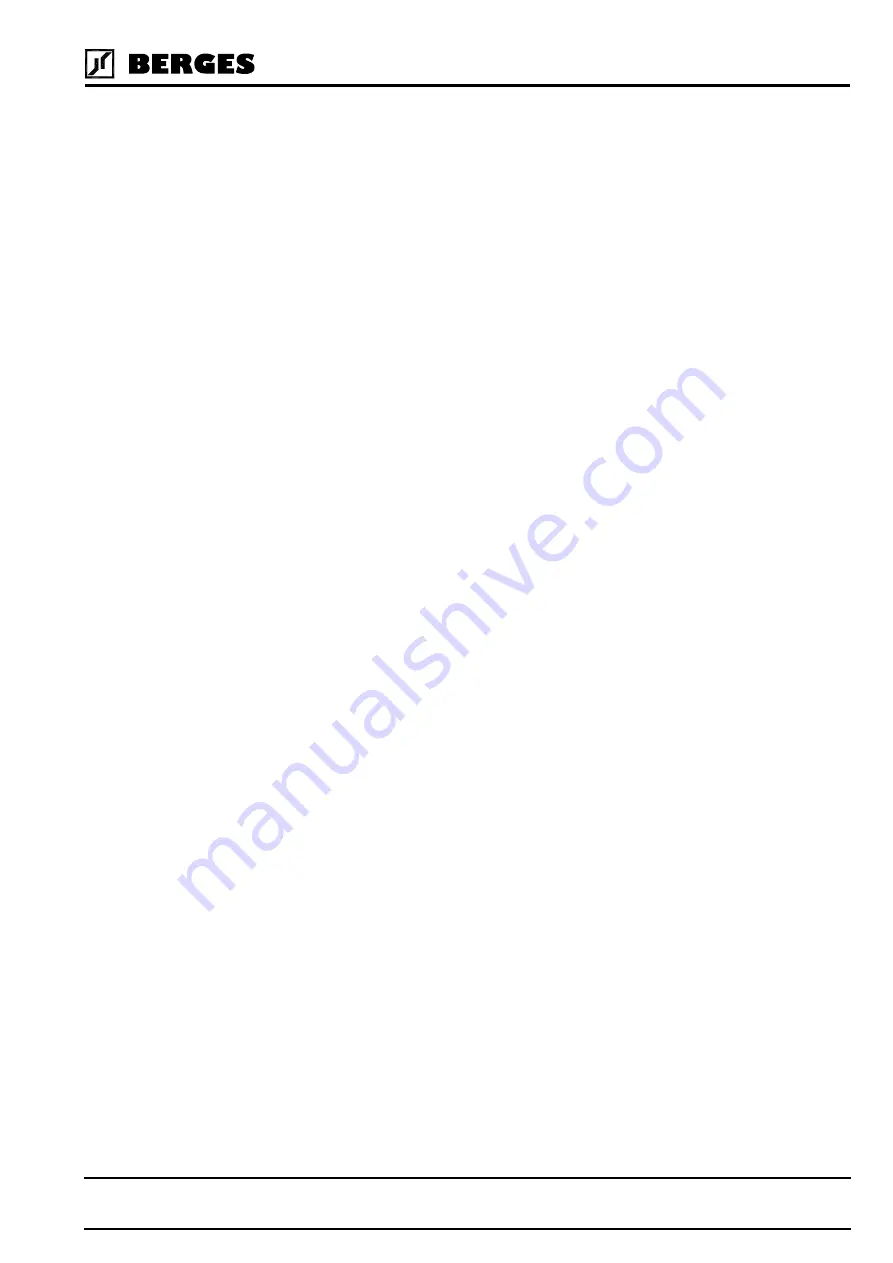
21.12.98
Operating manual
04_GB
ACP 3000 — 0.37–15.0
51
Berges electronic
•
D–51709 Marienheide-Rodt
•
Tel. 02264/17-0
•
Fax 02264/17126
6
PI Controller
6.1
Introduction
ACP 3000 inverters have a built-in PI (Proportional-Integral) Controller that makes it possi-
ble to control a process by adjusting motor speed using a reference input and a feedback
input. When PI control is enabled, several new parameters (as well as new data codes for
some existing parameters) become available to support PI control.
This section first provides an overview of how PI control operates. Following this discus-
sion, the new parameters and data codes are described.
6.2
Overview of PI Control
Figure 6.1 on the next page provides a flowchart of PI control. The characteristics of PI con-
trol are set with the
81-PRGNO
parameter (see page 56). The data codes for parameter
81-PRGNO
allow you to select:
Direct- or Reverse-Acting Loop
•
In a direct-acting loop, a positive error will cause an increase in output frequency. Con-
versely, in a reverse-acting loop, a positive error will cause a decrease in output frequen-
cy.
Slow or Fast Rate of Integration
•
A slow rate of integration is usually selected for processes with long time constraints (for
example, thermal and fluid level controls). On the other hand, a fast integration rate is
utilized for processes with short time constraints (such as mechanical systems and pres-
sure loops).
Whether Feed-Forward is Active
•
Feed-forward is useful in situations where the reference value has a direct relation to the
feedback signal, such as controlling motor speed in a closed loop. Note that feed-for-
ward should be enabled when attempting to close a speed loop.
Whether the PI Controller is turned on and off via the PS3 input.
Separate parameters are also available for adjusting proportional gain (parameter
B3-KP
),
integral gain (parameter
B4-KI
), and scaling for the feedback terminal VIN1 (parameter
B5-
KIN
). These parameters may be adjusted while the inverter is operating.
StockCheck.com