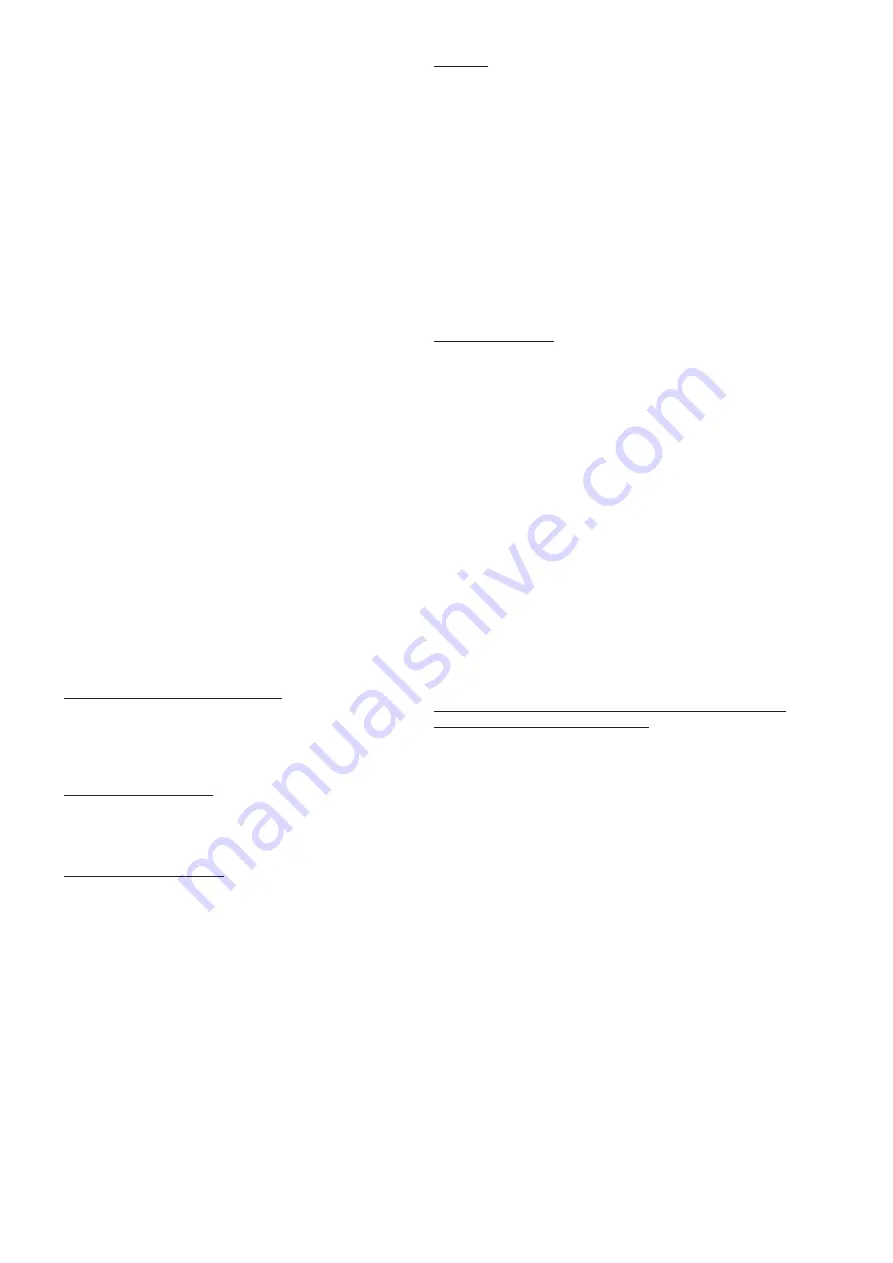
29
System power modulation is controlled by a PID regulator,
which controls the manifold temperature and the setpoint
is that of the active circuit (high or low temperature circuit
setpoint or DHW setpoint). The PID has a direct influence
on the last 2 burners ignited, whereas the previous ones
operate at maximum power.
If the manifold temperature < Setpoint – 5°C the next burn-
er is ignited and both are managed by the PID regulator.
The Master control unit waits for 30s and then
if the manifold temperature < Setpoint - 5°C, another burner
is ignited.
The first burner operates at maximum power, whereas the
other two are managed by the PID regulator.
If the manifold temperature > Se 2°C the last burn-
er ignited is shut off, the remaining last two burners are
managed by the PID regulator and the others operate at
maximum power. The Master control unit waits 30s before
making another decision.
MODE: MAXIMUM QUANTITY OF BURNERS IGNITED
(PAR.33=1)
All burners are controlled by the same PID regulator, which
controls the manifold temperature and the setpoint is that
of the active circuit (high or low temperature circuit setpoint
or DHW setpoint).
If the manifold temperature < Setpoint – 5°C the next burn-
er is ignited.
The Master control unit waits for 30s and then
if the manifold temperature < Setpoint - 5°C, another burner
is ignited.
If the manifold temperature > Se 2°C the last burner
ignited is shut off. The Master control unit waits 30s before
making another decision.
ADDITIONAL CASCADING MANAGEMENT FUNCTIONS
Sequential rotation of burner ignition
When supplying power to the Master control unit, the burn-
er with address 1 is the first in the sequence. After 24h, the
first burner will be the one with address 2, whereas the one
with address 1 will become the last in the sequence.
Ignition/shut off limitation
In both cascading strategies, after every ignition or shut off,
there is a minimum time during which the Master cannot
ignite or shut off burners.
Quick start-up and shut off
In both modes, there is a quick start-up and shut off func-
tion.
If the manifold temperature < Setpoint - 70°C
the burners are ignited at time intervals equal to 2s
If the manifold temperature > Se 4°C
the burners are shut off at time intervals equal to 2s.
Low load
The low load function prevents burner ignition and shut off
in the case of a low heat demand. The conditions for low
load operation activation is controlled in every Slave card
that sends the function activation request to the Master.
During normal operation, the setpoint of the active circuit
(high or low temperature circuit setpoint or DHW setpoint)
is sent to the Slave cards and is controlled by the tempera-
ture of the heating element by every Slave card:
if the modular system temperature > Setpoint – 8°C or
if the modular system temperature > 85°C - 8°C
consent for starting the burner is not given.
If the Slave board acquires a modular system temperature
greater than 85°C for 3 times with the burner ignited, the
heating element is turned off and the ignition procedure is
started again.
Emergency function
In the case of a Master card fault, there are two methods for
manually controlling the Slave cards:
- With eBUS and with the manifold sensor
Disconnect the power supply from the system, dis-
connect the BUS. Set the address 000000 on all
slave cards (J10 and J17 OFF). Connect a power
supply between 21 and 28 Vac to the BUS.
If the manifold temperature < Temp.Emergency
(Par.40; preset 70°C; can be set between 10 and
80°C) all the burners will operate at maximum pow-
er.
If the manifold temperature > Temp.Eme
5°C all burners are off.
- With PC
Disconnect the system power supply, disconnect
the BUS and connect the PC interface. The burner
power can be sent to the Slave card directly with the
PC.
b
In the case of error, contact Technical Assistance
Centre.
Heat demand management for the high temperature circuit
with analogue input (Par. 14=2 or 3)
The room thermostat for the high temperature circuit is
ignored in the case of heat demand and the input signal
is used for calculating the system setpoint temperature or
power.
The analogue input (see terminals 13-14 on the wiring dia-
gram on page 35) is only for the Master card and can also
be used for the low temperature circuit (Par.22). The ana-
logue input cannot be used for both circuits.
ANALOGUE POWER INPUT, Par. 14=2 (Par. 22=2 for low
temperature circuits)
The following rules apply to high temperature (low temper-
ature) circuit demand:
0-2Vdc:
no demand by the high temperature (low temper-
ature) circuit
2-9Vdc:
the heat demand is converted into a power de-
mand for each Slave. A 2V input corresponds to
minimum power, 9V to maximum power (Par.15).
The power is calculated linearly between 2V and 9V.
Hysteresis for the end of demand is 0.2V and there-
fore demand is present above 2V and stops below
1.8V.
Summary of Contents for Power Plus Box 1002 P INT
Page 1: ...Installation Manual CONDENSING Power Plus Box 1002 1003 1004 P INT EXT Installation Manual EN...
Page 36: ...36 12 WIRING DIAGRAMS...
Page 37: ...37 Valvola 2 vie Circolatore...
Page 42: ...42...
Page 43: ...43...