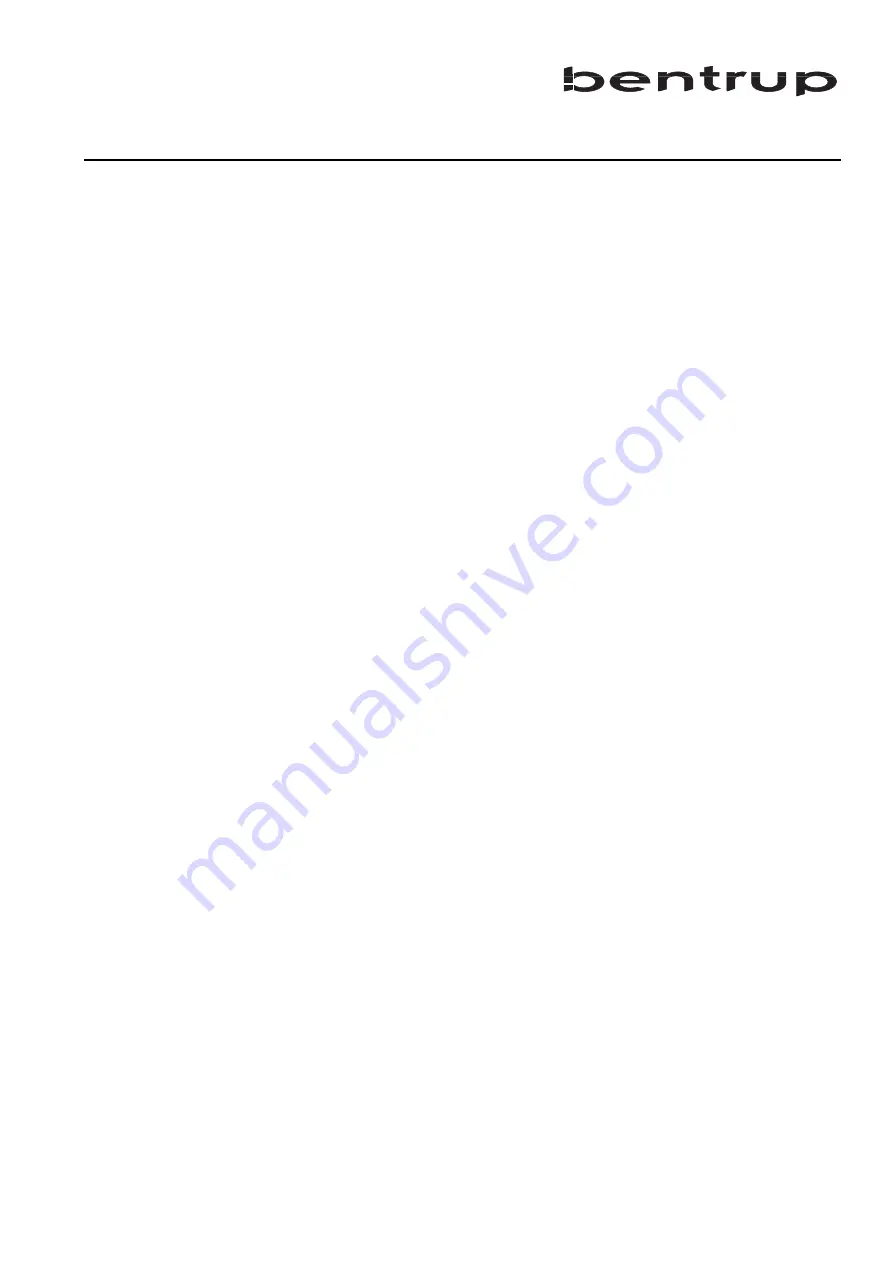
Your TC505 is the choice of the professionals in the
bentrup controller family TC500. These controllers
use the latest technology available and incorporate
many features which haven´t been available on kiln
controls before. Appearing as a controller easy to use,
it is a highly sophisticated instrument with a totally
configurable control design allowing adaption to
almost all applications (for details see Appendix C).
Reading through this manual quickly familiarizes you
with the numerous features of the TC505.
Please also refer to the safety advise of your kiln
manufacturer. Make sure that the control is placed at a
proper distance from the kiln and is not exposed to
direct heat or radiation from the kiln.
3
General Information.............................................3
Calling up a Programme .......................................5
Starting a Firing ...............................................5
Displays during a Firing ...................................6
Entering and Checking a Firing Curve...................7
The Value SKIP ................................................7
Starting a Programme ...........................................8
Working with Programmes ..............................8
Reading the Kiln Temperature ..............................9
Control outputs, Time / Date............................9
Locking the Controller........................................11
Miscellaneous
Power Failure.................................................11
Actual Duration of a Segment........................11
Kiln can not follow the Ramp ........................11
Miscellaneous ...............................................12
Appendix A: Error Messages of the TC505..........13
Appendix B: Data- and Error Log........................16
Calling up the Data Log.................................17
Calling up the Error Log.................................18
Appendix C: Configuration .................................19
Explanation of the Parameters ........................20
Calling up the Configuration..........................22
Appendix D: Weekly Switching Clock ................23
Appendix E: Communication Link ......................24
Appendix F: Checking Installed Options.............24
Appendix G: Electrical Connections ...................25
Contents
General Information