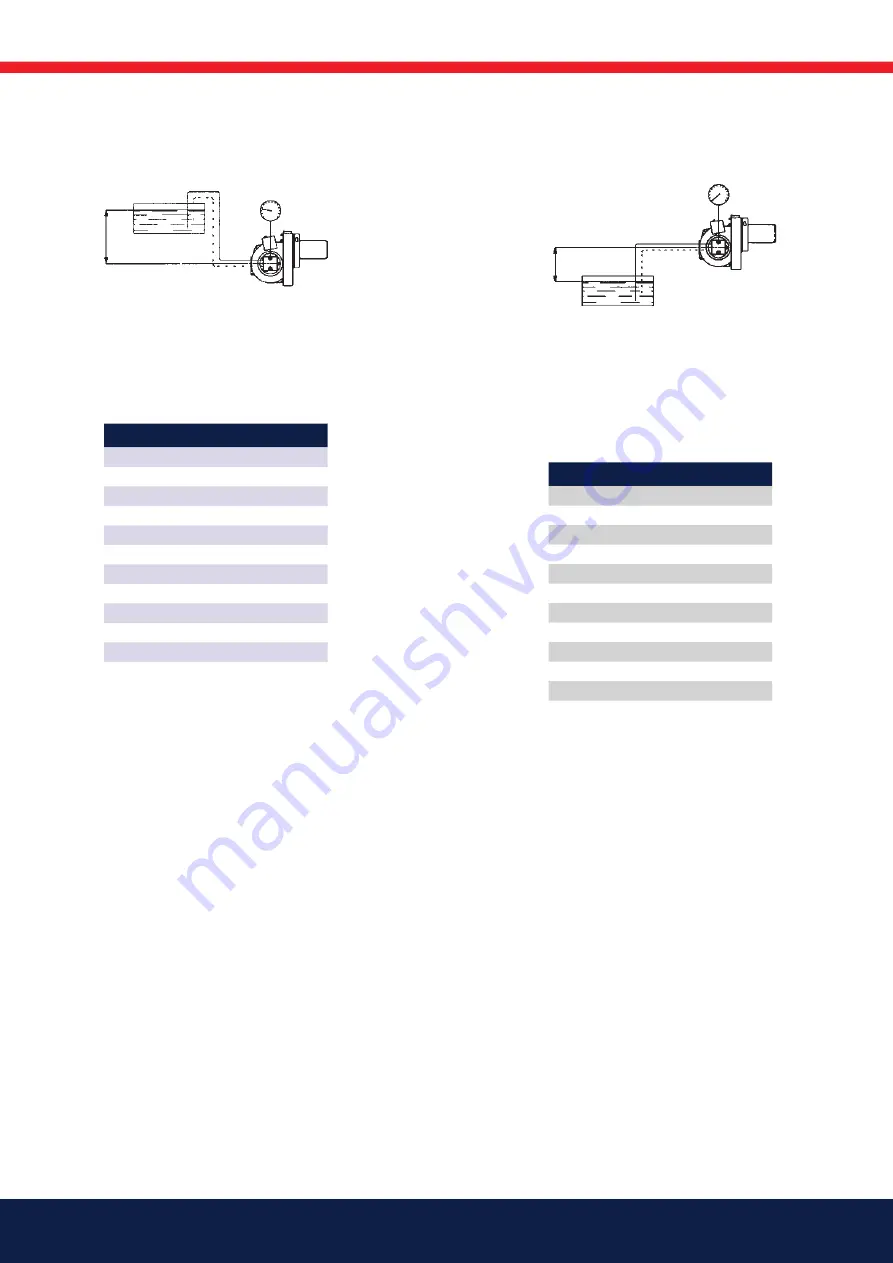
28
Bentone
The suction line tables consist of theoretically calculated values where the
pipe dimensions and oil velocity have been matched so that turbulences will
not occur. Such turbulences will result in increased pressure losses and in
acoustic noise in the pipe system.
In addition to drawn copper piping a pipe system usually comprises 4
elbows, a non-return valve, a cut-off valve and an external oil filter.
The sum of these individual resistances is so insignificant that they can be
disregarded.
The tables do not include any lengths exceeding 100 m as experience
shows that longer lengths are not needed. The tables apply to a standard
fuel oil of normal commercial quality according to current standards. On
commissioning with an empty tube system the oil pump should not be
run without oil for more than 5 min. (a condition is that the pump is being
lubricated during operation).
The tables state the total suction line length in metres at a viscosity of 6,0
mm2/s.
6.7 Suction line tables
H
1-pipe system
Pipe diameter
Höjd
H
ø12mm ø15mm ø20mm
m
m
m
m
Two-pipe system
Height
Pipe diameter
H
ø12mm ø15mm ø20mm
m
m
m
m
4,0
81
100
100
3,5
76
100
100
3,0
71
100
100
2,5
66
100
100
2,0
61
100
100
1,5
56
100
100
1,0
51
100
100
0,5
46
100
100
H
1-pipe system
Height
Pipe diameter
H
ø12mm ø15mm ø20mm
m
m
m
m
With an underlying tank a 1-pipe-
system is not recommended.
Two-pipe system
Height
Pipe diameter
H
ø12mm ø15mm ø20mm
m
m
m
m
0,0
41
100
100
-0,5
36
89
100
-1,0
31
77
100
-1,5
26
65
100
-2,0
22
53
100
-2,5
17
41
100
-3,0
12
29
91
-3,5
7
17
53
-4,0
2
5
15
Summary of Contents for B 80-3R
Page 29: ...29 Bentone 165 305 04 7 Electric equipment 7 1 Safety system...
Page 54: ......
Page 55: ......
Page 56: ...Enertech AB P O Box 309 SE 341 26 Ljungby www bentone se www bentone com...