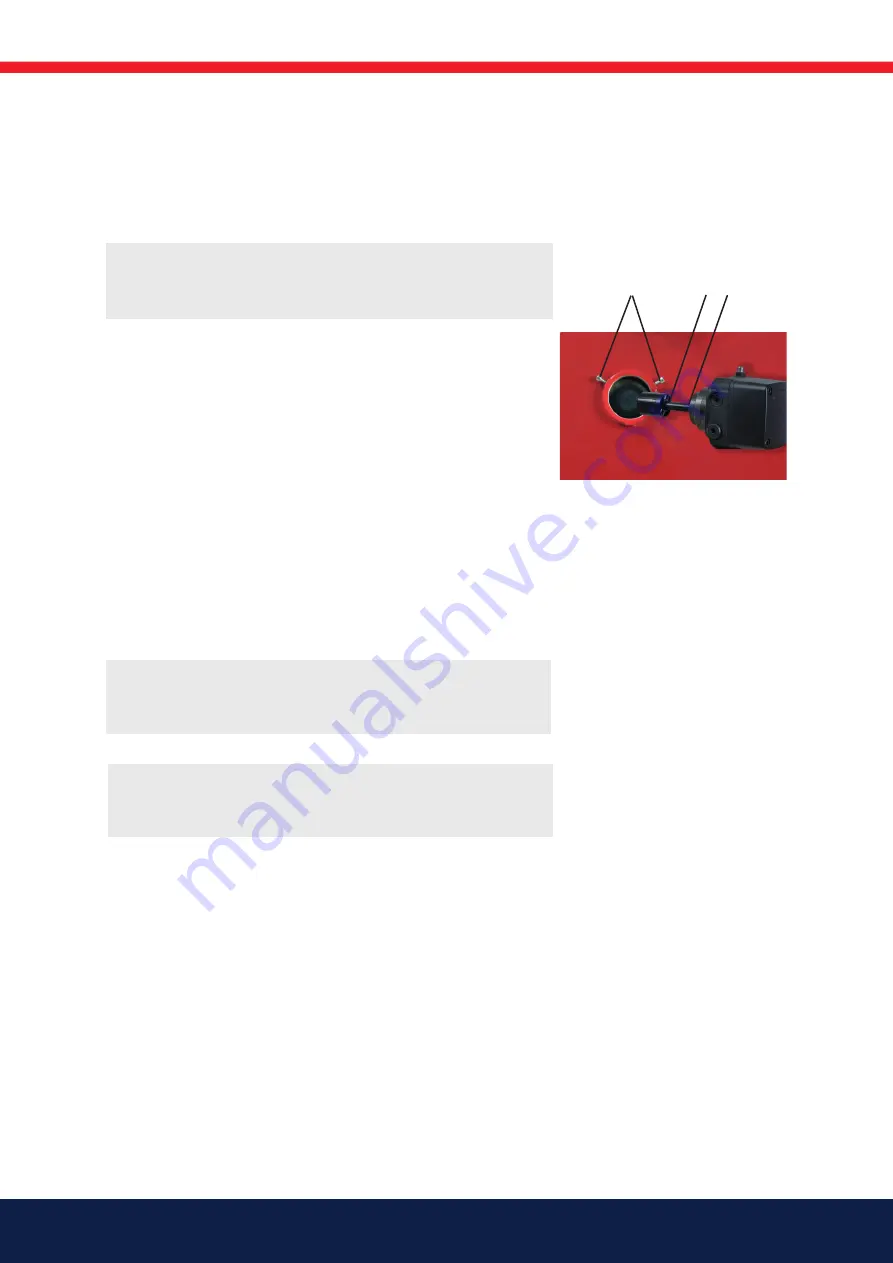
26
Bentone
!
Use caution when operating the burner, surfaces may be hot.
!
When servicing oil bearing components, check the oil density
when the burner is commissioned after servicing.
J
K
6.4 Replacement of oil pump
Removal and installation
1.
Turn off the main power switch and disconnect the Eurostecker
connectors from the burner.
2.
Disconnect the oil hoses from the pump.
3.
Undo the screws (J) and pull out the oil pump.
4.
Measure the distance between the pump mounting and the pump
coupling (K).
5.
Transfer the pump coupling to the new pump and adjust to give the
same spacing between the pump and pump coupling as before (K).
6.
Fit the oil pump on the burner and tighten the screws (J). (It is
important that splines on the pump shaft align correctly with the pump
coupling.)
7.
Fit the oil hoses.
8.
Connect the Eurostecker connectors and turn on the main power
switch.
9.
Bleed the pump, start the burner and adjust to the correct oil pressure.
10. Check combustion.*
Note:
*
When servicing/replacing components that affect combustion, an
analysis and soot test must be carried out on the installation
!
If the burner is directly connected, ensure that all components on
the burner are without power.