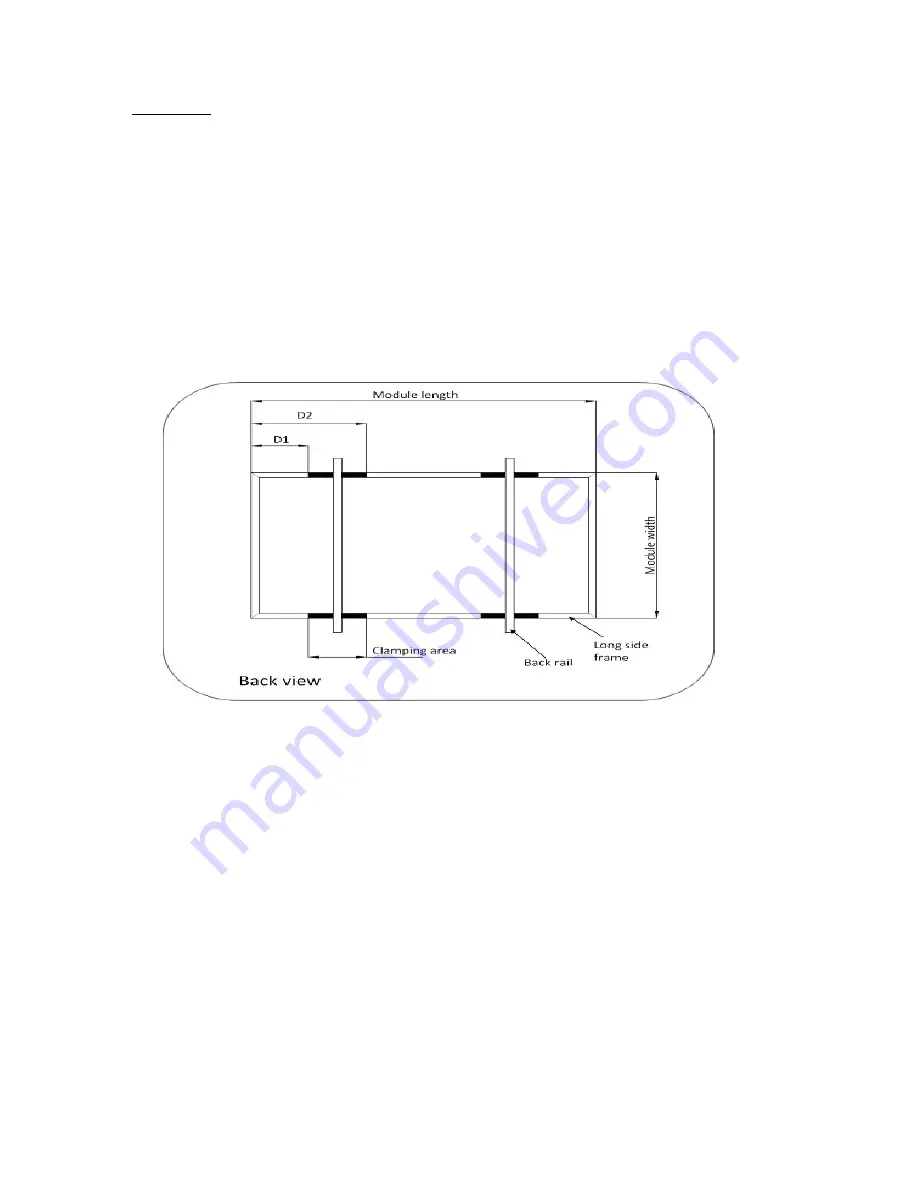
Last revised: May 17, 2013
8
CLAMPING
CLAMPING
CLAMPING
CLAMPING
Note that the clamping clips on the side frame should be installed in parallel to each other.
The cross-section dimension of Back rail should be larger than 40mm*80mm. When
Clamping on longer side frame, the side frames of clamping should touch longer sides of the
module to ensure tight connection between frame and clamping.
Figure 3-4 shows module mounting areas. The centerline of the clips should be between
D1-281mm~D2-375mm from the short end of the module for
2400Pa design strength under
UL 1703.
Figure 3
Figure 3
Figure 3
Figure 3----4
44
4: Effective Mounting Area (Clamping)
: Effective Mounting Area (Clamping)
: Effective Mounting Area (Clamping)
: Effective Mounting Area (Clamping)