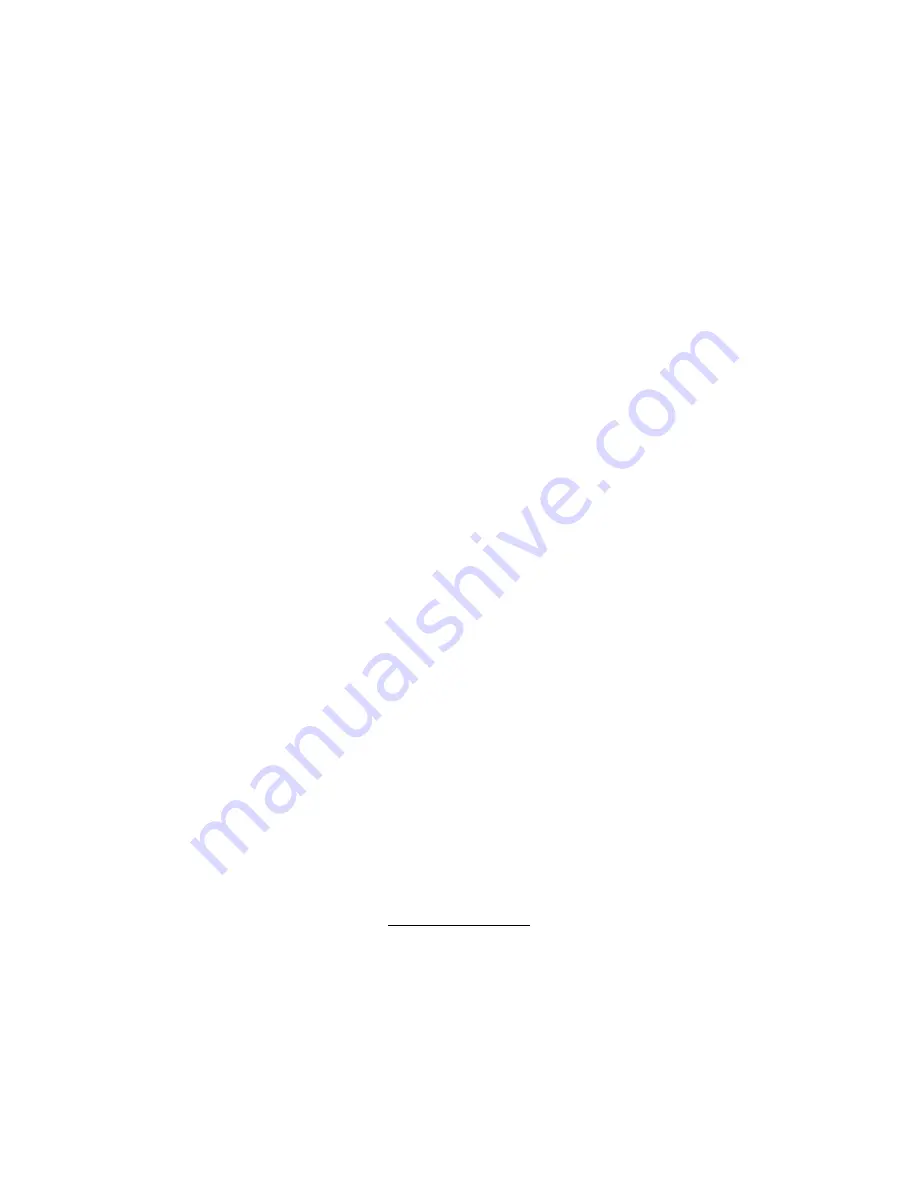
44
44
WILL NOT RAISE LOADED LIFT
POSSIBLE CAUSE
1. Air in oil, (1,2,3,4)
2. Cylinder binding, (5)
3. Cylinder leaks internally, (5)
4. Lift overloaded, (6,5)
5. Lowering valve leaks, (7,8,1,5,9)
6. Motor runs backwards, (10,12,9)
7. Pump damaged, (5,9)
8. Pump won’t prime, (1,2,3,4,5,11,9)
9. Relief valve leaks, (8,5,9)
10. Voltage to motor incorrect, (10,12,5)
REMEDY
INSTRUCTIONS
1. Check oil level . . . . . . . . . . . . . . . . . . . . . . . . . . . . . . . . . . The oil level should be up to the bleed screw in the
reservoir with the lift all the way down.
2. Check/Tighten inlet tubes . . . . . . . . . . . . . . . . . . . . . . . . . . Replace inlet hose assembly.
3. Oil seal damaged or cocked . . . . . . . . . . . . . . . . . . . . . . . . Replace oil seal and install.
4. Bleed cylinders . . . . . . . . . . . . . . . . . . . . . . . . . . . . . . . . . See Installation Manual.
5. See Installation Manual . . . . . . . . . . . . . . . . . . . . . . . . . . . Consult Lift Manufacturer.
6. Check vehicle weight . . . . . . . . . . . . . . . . . . . . . . . . . . . . . Compare weight of vehicle to weight limit of the lift.
7. Flush release valve . . . . . . . . . . . . . . . . . . . . . . . . . . . . . . Hold release handle down and start unit allowing it to
run for 15 seconds.
8. Replace with new part . . . . . . . . . . . . . . . . . . . . . . . . . . . . . Replace with new part.
9. Return unit for repair . . . . . . . . . . . . . . . . . . . . . . . . . . . . . . Return unit for repair.
10. Check motor is wired correctly . . . . . . . . . . . . . . . . . . . . . . Compare wiring of motor to electrical diagram on
power unit drawing.
11. Inlet screen clogged . . . . . . . . . . . . . . . . . . . . . . . . . . . . . . Clean inlet screen or replace.
12. Check wall outlet voltage and wiring . . . . . . . . . . . . . . . . . . Make sure unit and wall outlet is wired properly.
IMPORTANT
If a vehicle becomes stranded in the air, follow all operation instructions as shown on pages 33 - 38.
If, after observing that all mechanical locks are released and the lift still fails to move following all standard operat-
ing procedures, immediately stop using the lift and contact the factory or a factory-approved service center for further
instructions.
Summary of Contents for XPR-12CL
Page 14: ...14 HOSE ROUTING Side of Post ...
Page 27: ...27 ...
Page 30: ...30 30 OPTIONAL EQUIPMENT INSTALLATION ...
Page 46: ...46 ...
Page 47: ...47 ...
Page 48: ...48 Depends on model ...
Page 61: ...61 ...
Page 64: ...64 ...