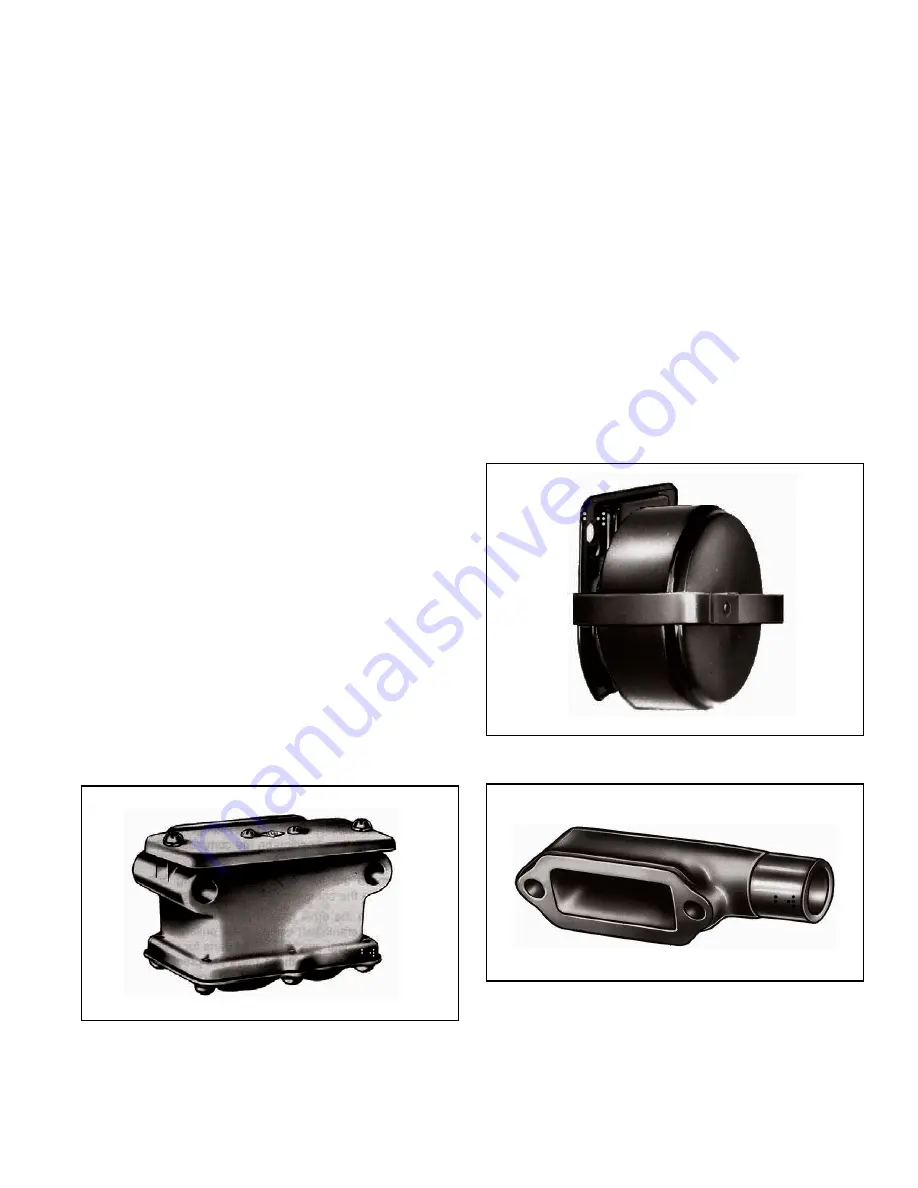
5
DRY ELEMENT—PLEATED PAPER AIR
STRAINER
Every 20,000 miles or 800 operating hours:
Remove the spring clips from either side of mounting baffle
and remove the cover. Replace the pleated paper filter and
remount the cleaned cover making sure the filter is in
position. Be sure to replace the air strainer gasket if the
entire air strainer is removed from the compressor intake.
(Note: Some compressors are fitted with compressor intake
adapters which allow the compressor intake to be connected
to the engine air cleaner.) In this case, the compressor
receives a supply of clean air from the engine air cleaner.
When the engine air filter is changed, the compressor intake
adapter should be checked. If it is loose, remove the intake
adapter, clean the strainer plate, if applicable, and replace
the intake adapter gasket, and reinstall the adapter securely.
Check line connections both at the compressor intake
adapter and at the engine air cleaner. Inspect the connecting
line for ruptures and replace it if necessary.
COOLING
Air flowing through the engine compartment from the action
of the engine’s fan and the movement of the vehicle assists
in cooling the crankcase. Coolant flowing from the engine’s
cooling system through connecting lines enters the
compressor and flows through the internal passages in the
cylinder block and head and back to the engine. Proper
cooling is important in maintaining discharge air temperatures
below the 400°F recommended maximum.
PREVENTIVE MAINTENANCE
Regularly scheduled maintenance is the single most
important factor in maintaining the air brake charging system.
Refer to Table A in the Troubleshooting section for a guide to
various considerations that must be given to the maintenance
of the compressor and other related charging system
components.
Important Note: Review the warranty policy before
performing any intrusive maintenance procedures. An
extended warranty may be voided if intrusive maintenance
is performed during this period.
Every month, 300 operating hours or after each 10,000 miles,
depending on the operating conditions, experience and the
type of strainer used, service the air strainer.
POLYURETHANE SPONGE STRAINER
Every 5000 miles or 150 operating hours:
Remove and wash all of the parts. The strainer element
should be cleaned or replaced. If the element is cleaned, it
should be washed in a commercial solvent or a detergent
and water solution. The element should be saturated in clean
engine oil, then squeezed dry before replacing it in the
strainer. Be sure to replace the air strainer gasket if the
entire air strainer is removed from the compressor intake.
FIGURE 5 - POLYURETHANE SPONGE STRAINER
FIGURE 6 - PAPER AIR STRAINER DRY ELEMENT-
PLEATED
FIGURE 7 - COMPRESSOR INTAKE ADAPTER