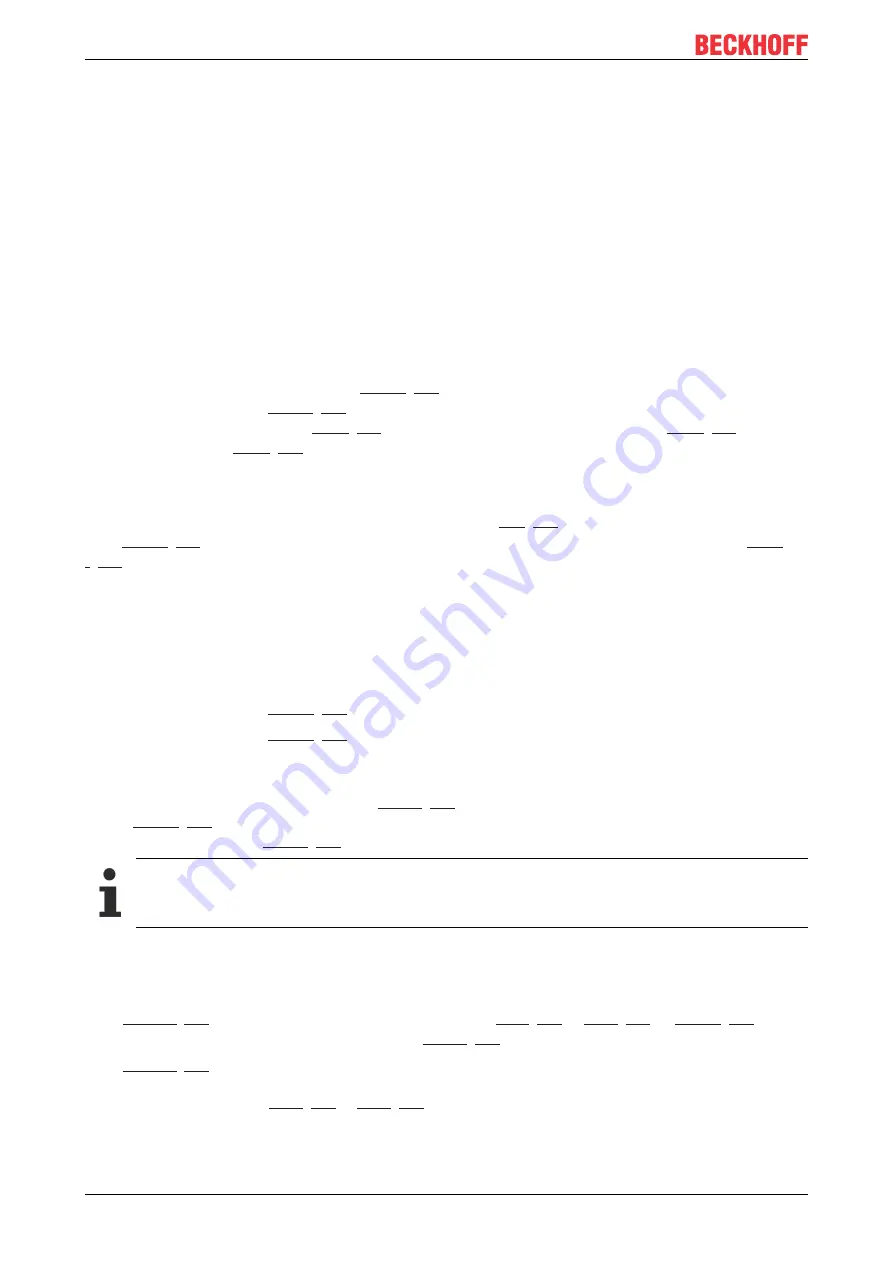
Basic function principles
KL2532/KS2532, KL2552/KS2552
16
Version: 3.2.0
3
Basic function principles
3.1
Basic principles
The KL2532/KS2532 DC motor terminal integrates two compact DC motor output stages up to 24 W in a
very compact design.
The KL2552/KS2552 DC motor terminal integrates two compact DC motor output stages up to 250 W in a
very compact design.
General functions
Enable/Readiness for operation
For activating the output stage enable bit
has to be set. If the terminal is in an error-free state
at the time, it sets ready bit
as acknowledgement. If the terminal is ready to operate, it indicates
this by setting "Ready to Enable" (
). Directions of rotation are indicated by bit
(Moving Negative).
Set / delete position
The user can set or delete the current position value. Register
is used as reference. A rising edge
at bit
sets the current position, and the acknowledgement is provided through status bit
.
Latch functions (only KL2552/KS2552)
The internal encoder offers the option of registering a latch event. A latch event can be generated via the
digital input signals.
The terminal response to the latch events is activated as follows:
activates the rising edge at the digital input (highest priority)
activates the falling edge at the digital input (second-highest
priority)
Once the user has enabled the function, during the next latch event, the terminal saves the current position
value and indicates this by setting status bit
. Reading of latch values must be initiated by
, which causes the latch value to be mapped in the DataIN process data (the terminal
Reading the latch value
The enable that was set previously must be retained while reading out the latch value. The latch
value is lost if enable is cancelled!
Manual and automatic torque reduction
A torque reduction can be achieved in two ways:
•
= 0: The torque is reduced (to the value in
or
=
1. The terminal acknowledges this by setting
.
•
= 1: The torque is automatically reduced, if the process input data exceed the values
configured in R45 or R48.The torque is reduced automatically if the process input data exceed the
settings configured in
. The reduction is deactivated, if the process input data
fall below a value of R45 or R48 - 2%.
R41 (reduced torque) and R45 (torque threshold) are used for the positive direction of rotation.