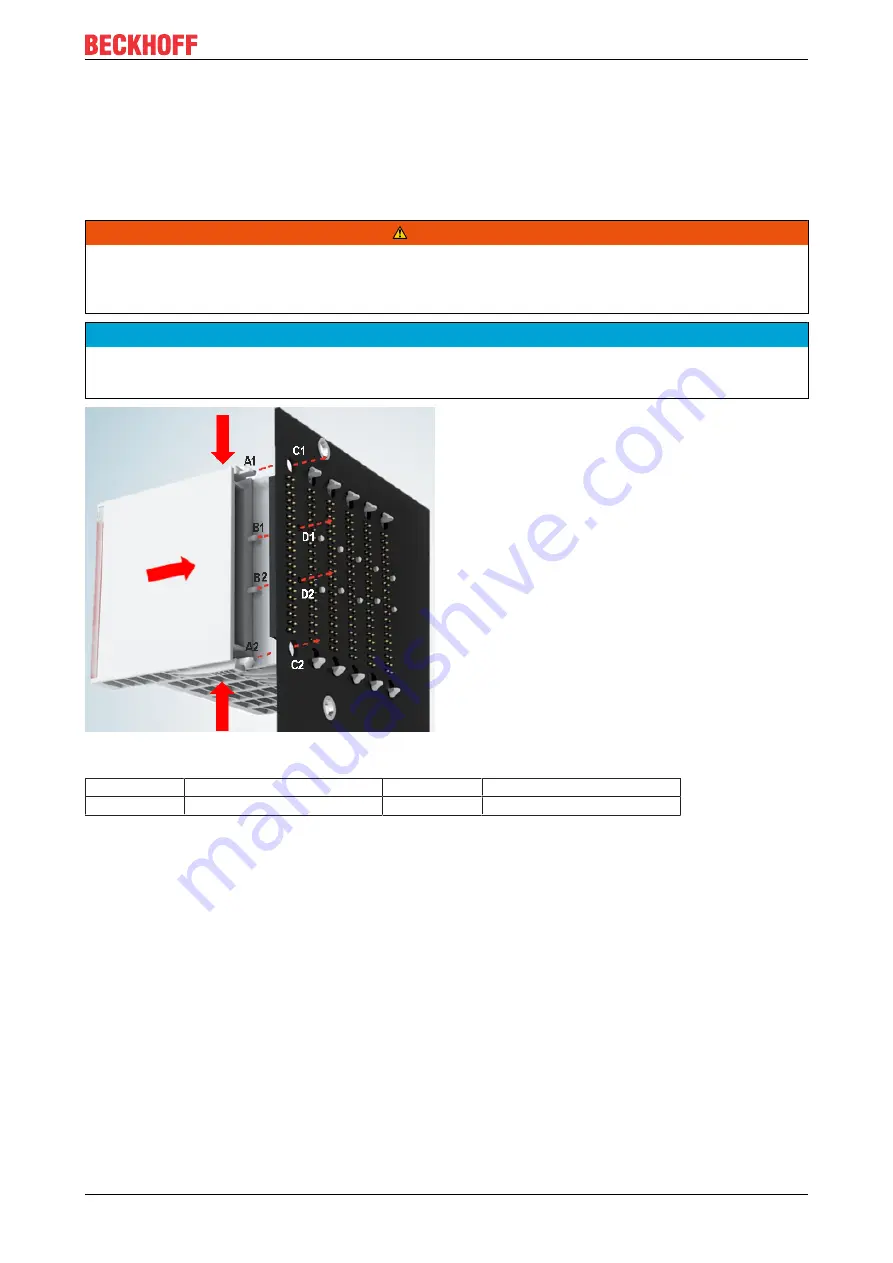
Installation of EJ modules
EJ3255
27
Version: 1.1
4.5
Installation on the signal distribution board
EJ modules are installed on the signal distribution board. The electrical connections between coupler and EJ
modules are realized via the pin contacts and the signal distribution board.
The EJ components must be installed in a control cabinet or enclosure which must provide protection against
fire hazards, environmental conditions and mechanical impact.
WARNING
Risk of injury through electric shock and damage to the device!
Bring the module system into a safe, de-energized state before starting installation, disassembly or wiring
of the modules.
NOTE
Risk of damage to components through electrostatic discharge!
Observe the regulations for ESD protection.
Fig. 19: Installation of EJ modules
A1 / A2
Latching lugs top / bottom
C1 / C2
Mounting holes
B1 / B2
Coding pins
D1 / D2
Coding holes
To install the modules on the signal distribution board proceed as follows:
1. Before the installation, ensure that the signal distribution board is securely connected to the mounting
surface. Installation on an unsecured signal distribution board may result in damage to the board.
2. If necessary, check whether the positions of the coding pins (B) match the corresponding holes in the
signal distribution board (D).
3. Compare the device name on the module with the information in the installation drawing.
4. Press the upper and the lower mounting tabs simultaneously and push the module onto the board
while gently moving it up and down, until the module is latched securely.
The required contact pressure can only be established and the maximum current carrying capacity en-
sured if the module is latched securely.
5. Use placeholder modules (EJ9001) to fill gaps in the module strand.
Summary of Contents for EJ3255
Page 2: ......