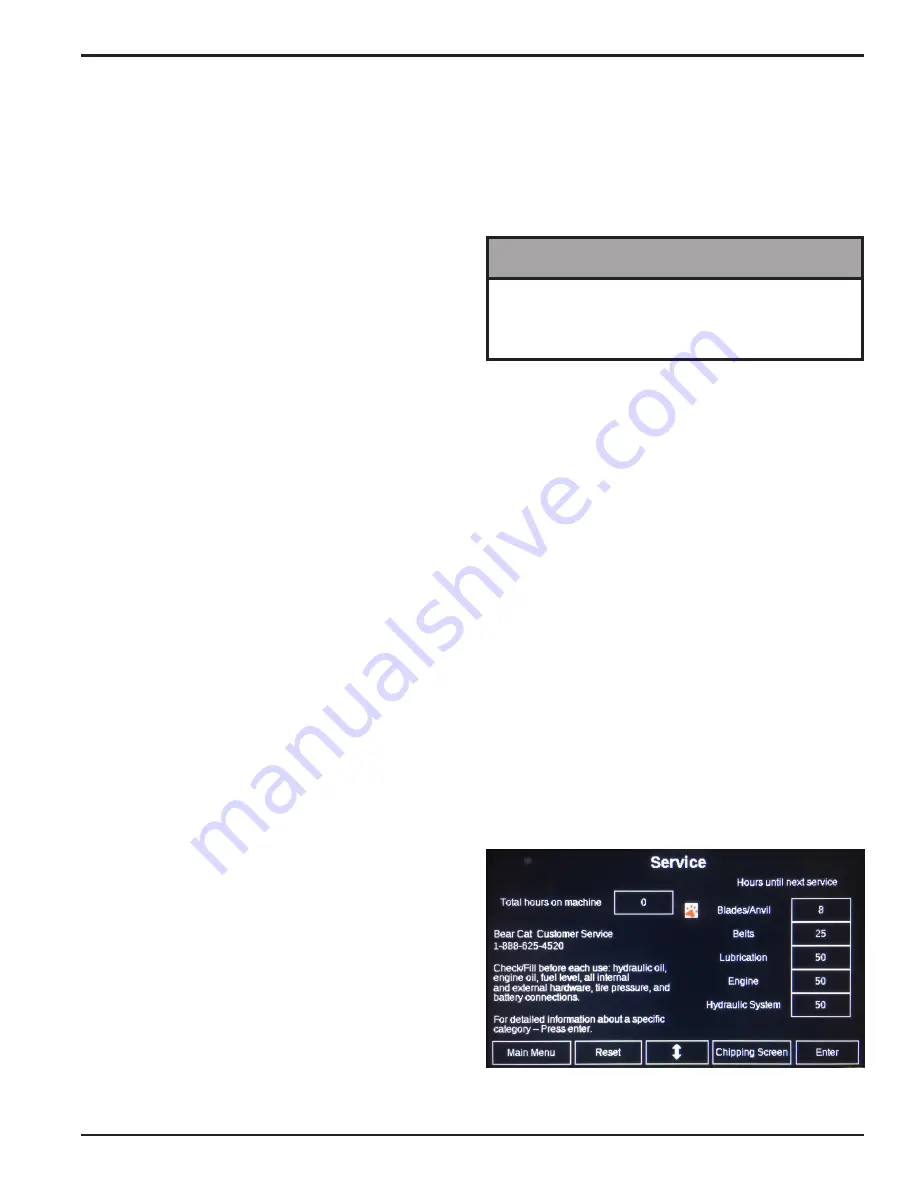
19
9 INCH CHIPPER
ENGLISH
OPERATION
Bar safety system has been activated.
To re-engage the
feed roller safety system after the Knee Bar safety
system has been activated, the operator must press
and hold the Knee bar Reset button for two seconds.
Any time the Knee Bar safety system is activated,
carefully check that the infeed chute and feed roller
are clear and it is safe to continue chipping before
resetting the Knee Bar safety system.
4.7.3 HOURS/SERVICE REMINDERS
The Hours/Service Reminders screen is shown in
Figure 4.6.
The Total hours on the chipper are shown in the upper left
corner of the screen. The total hours are based on “Key
On” time and cannot be reset.
The service reminders on the right hand side of the screen
are all count down timers. They all show the time until
the next service is required in each category. Additional
information for each category can be found by moving the
cursor next to a category with the Navigation Button and
pressing Enter.
●
Blades/Anvil –
Hours are based on the time the
feed roller is in Forward since that is the only time the
blades can actually chip wood.
●
Belts –
Hours are based on “Key On” time.
●
Lubrication –
Hours are based on “Key On” time.
●
Engine –
Hours are based on “Key On” time. The
service interval is dependent on the model selected.
(Does not apply to PTO driven models.)
●
Hydraulic System –
Hours are based on “Key On”
time. First service interval is at 50 hours; subsequent
service intervals are at 200 hours.
Anytime the user leaves the Chipping Screen, the
feed roller will automatically stop. The user will have to
re-enter the Chipping Screen and press the Forward
button again to resume chipping.
NOTE
Figure 4.6, Hours/Service Reminders
In the upper left hand corner of the screen is a reminder
that the feed roller speed can be adjusted. The adjustment
occurs at the control valve, the location of which varies by
model. In general, the speed of the feed roller should be
slower for large diameter material and faster for smaller
diameter material. See chipper owner’s manual for
detailed instructions.
Below the Feed Roller Speed image is an empty area of
the screen that will flash Check blades/anvil when the
chipper blades or anvil require service.
After servicing the blades and anvil, the service indicator
will need to be reset. See Section 4.7.3 for information on
resetting the service indicators.
The large indicator in the upper right hand corner and the
text box below it will give one of four indications:
●
Flashing Green –
The chipping rotor has not achieved
enough RPM to begin chipping. It is not possible to
engage the feed roller in the forward direction when
the indicator is flashing green. The text box below the
indicator will display “RPM Not Met.”
●
Solid Green –
The chipping rotor has achieved
sufficient RPM to begin chipping. The feed roller can
now be engaged in the forward direction. The text
box below the indicator will display “FORWARD,”
“REVERSE,” or “STOP.”
●
Solid Red –
The knee bar has been activated and the
feed roller is now stopped. The text block below the
indicator will display “Hold Knee Bar Reset.”
The Knee Bar functions as an emergency stop system
for the feed roller to immediately stop the feed roller
system. Occasionally, branches or limbs may contact
the Knee Bar with enough force to activate the Knee
Bar safety circuit. When this occurs the operator will
need to reset the Knee Bar safety system with the
“Knee Bar Reset” button to continue chipping. The
“Knee Bar Reset” button will need to be held for two
seconds to reset the system.
Carefully check to be certain the infeed chute and
feed roller are clear and that it is safe to continue
chipping before resetting the Knee Bar Reset.
●
Solid Yellow –
There is a fault in the chipper control
system. The text box below the indicator will display
“Go to Diagnostic Screen.”
The buttons to the left and to the right of the Navigation
Button are used to control the feed roller.
The Forward button starts the feed roller turning forward
and feeds material into the chipper.
The Reverse button reverses the direction of the feed
roller and will push the material back toward the operator.
The Stop button stops the feed roller.
The Knee Bar Reset button resets the controller so
Forward and Reverse can be re-engaged after the Knee