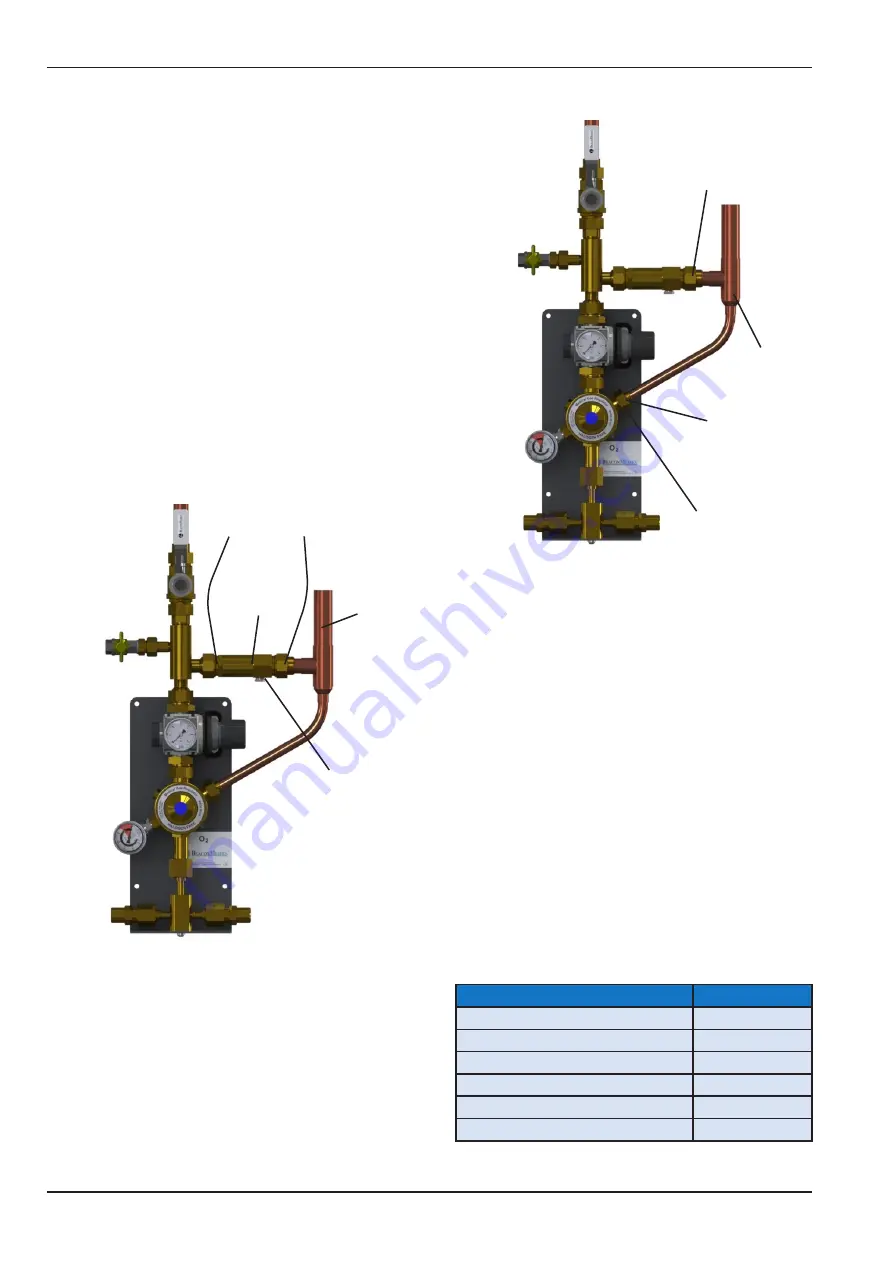
20
Manual Manifold
2006230.03
6.6.2 Slowly turn the left hand 1” swivel nut
connection. If the you hear gas escaping do not fully
unscrew the joint until the system is fully drained.
6.6.3 Fully disconnect the 1” joints plus optional
exhaust connection if fitted, as shown in
figure 15
,
and gently remove the unit by sliding it towards you.
Take care not to damage the seals.
6.6.4 Inspect the existing seals and replace if
required, see
figure 15
for seal part numbers.
Remove the 1/8 blanking plug from the old relief valve
and fit to the new unit.
6.6.5 Taking care not to damage the O-ring seals
replace the new relief valve as shown in
figure 15
, and
fasten the 2 flat face joints.
6.6.6 Follow steps in
section 6.11
to bring the
control panel back online.
6.7 Replace 1st stage relief valve
(P/N: 2005384)
6.7.1 Complete steps in
section 6.1
before carrying
out any component replacement on the control panel.
6.7.2 If the optional exhaust assembly is installed
disconnect the 3/4” and 1” swivel nut connection.
Ensure there is adequate space for removing the valve
without spraining the pipe work
(as shown in figure
16)
. Pipe line clamps may need to be unfastened to
achieve this.
Figure 15 - 2nd Stage Relief Valve Replacement
2 x 1” flat face connections
(O-ring P/N: 2000152)
2nd Stage
Safety Relief
Valve
1/8”
blanking
plug and
seal
Figure 16 - 1st Stage Relief Valve Replacement
3/4” flat face
connections
(O-ring seal P/N:
2000179
1st Stage Safety
Relief Valve
(Bonded seal P/N:
1824977)
1” flat face connections (O-ring
P/N: 2000152)
Optional
exhaust
connection
Optional
exhaust
connection
6.7.3 Start to unscrew the 1st stage relief valve, if
you hear gas escaping do not fully remove until the
system is fully drained.
6.7.4 Inspect the existing seals and replace if
required,
see figure 16
for seal part numbers.
6.7.5 Taking care not to damage the O-ring seals
replace the new relief valve as shown in
figure 16
,
and fasten the 2 optional exhaust pipe flat face
joints if previously fitted.
6.7.6 Follow steps in
section 6.11
to bring the
control panel back online.
6.8 Replace Cylinder Header
Non-return Valves
(see table 9 for part numbers)
Table 9: Header Non-return Valve Part
Numbers
Gas Type
Part Numbers
Oxygen (O2)
2000288
Nitrous Oxide (N2O)
2000289
Oxygen/Nitrous Oxide (O2/N2O)
2000290
Medical Air
2000291
Nitrogen (N2)
2000292
Carbon Dioxide (CO2)
2005850