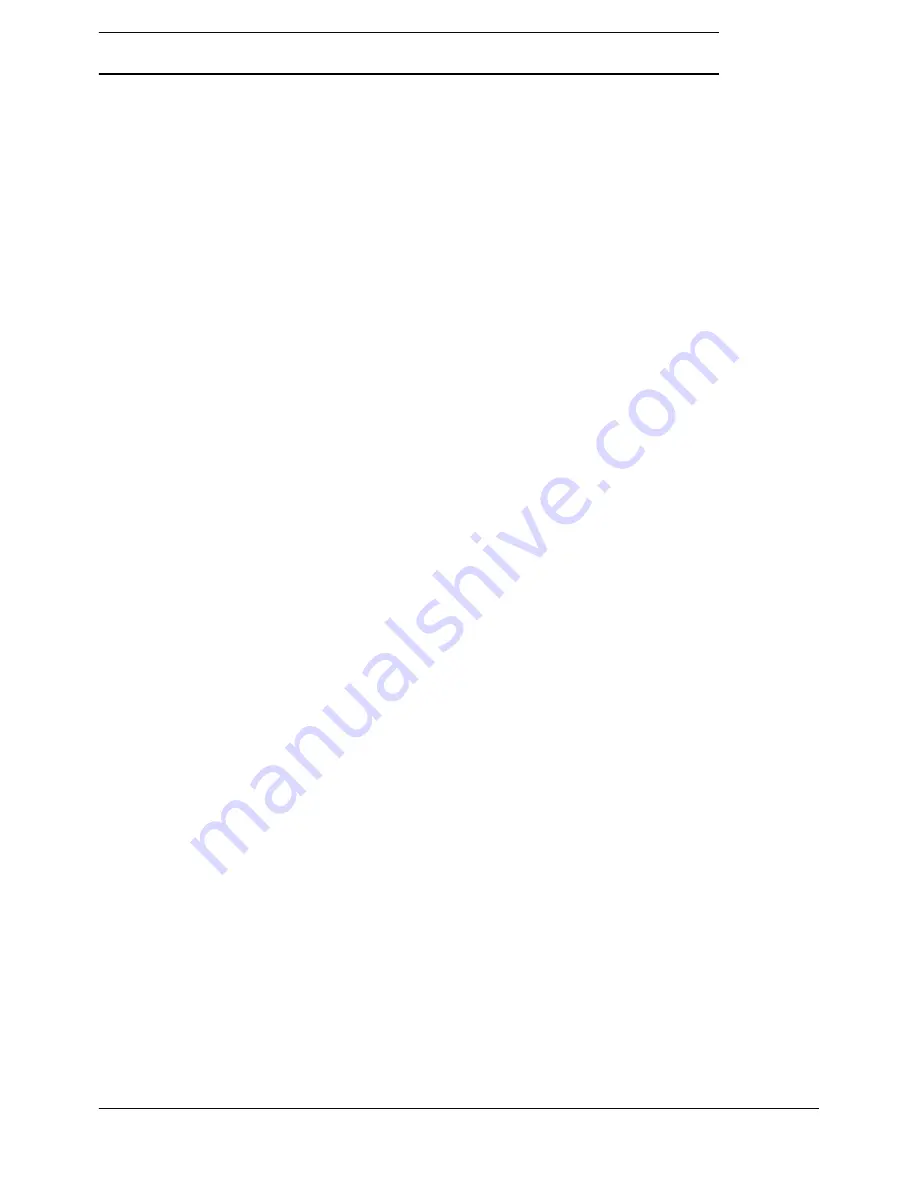
4
Commissioning
Introduction
Commissioning of the Anaesthetic Gas Scavenging disposal system must be carried out in full after initial
installation. Appropriate sections of the commissioning procedure must be carried out post major component
change, during the routine maintenance cycle or when the system has been shut down and unused for a period
of 4 weeks. The object of commissioning is to ensure that all components are serviceable and that the system
is adjusted to produce the correct design flow rates and performance figures. Personnel carrying out the
commissioning procedure must be conversant with information contained within this manual and fully
understand the layout of the actual installation to be commissioned. Commissioning is carried out in two parts.
Part 1
Part 1 of the commissioning procedure is carried out after installation of the pipeline distribution system and
all first fix assemblies. This procedure is designed to prove the integrity of the pipeline installation in
accordance with BS6834:1987 and BS EN ISO 7396-2 and consists of the following steps:
1. Check that the pipeline installation is correctly identified and labelled with identification tape at 10 metre
intervals and on both sides of any dividing wall.
2. Remove second fix assemblies from all terminal units (if previously fitted).
3. Clean the piping: purge the pipeline installation to remove all particular matter.
4. Blank off all terminal first fix assemblies by fitting blanks.
5. Remove the flow regulating valve(s) from the distribution system (if previously fitted). Use one open
pipeline to pressure test the system and blank off the remainder.
6. Disconnect the inlet pipeline to the exhauster unit and blank off the open pipeline connection. Pressure
test the pipeline installation at 0.7 bar for 15 minutes and check that the pressure loss does not exceed 0.1
bar. Locate and rectify any defective pipe work as necessary and repeat the pressure test. Remove blank
and re-connect inlet pipeline to the exhauster unit.
7. Re-fit all flow regulating valves to the distribution system. Check each valve adjuster for freedom of
operation and re-fit silencers.
8. Remove blanks Part No 1825190 from all terminal units and re-fit second fix assemblies (if previously
fitted).
9. On multi-system installations, carry out anti-confusion testing in accordance with HTM2022/02-01.
Part 2
Part 2 of the commissioning procedure is carried out on completion of all installation work. The procedure is
designed to adjust and check system design performance and functionally test all components in accordance
with BS6834:1987 and BS EN ISO 7396-2, and consists of the following operations:
Terminal units
1. Ensure that all AGS disposal system terminal units are correctly identified and labelled.
2. Insert an AGS probe into each terminal unit and check for smooth operation and effective thread action.
3. Ensure that the variable orifice of all terminal units is set to maximum prior to commencing the system
balancing.
4. On completion of any adjustments to the variable orifice within the terminal units, ensure the locking grub
screw is tightened in fully against the back of the terminal to ensure no wandering of the adjustment occurs.
Instruction book
27
Summary of Contents for AGS 1560
Page 2: ......
Page 11: ...Simplified schematic of a AGS Simplex installation Instruction book 9...
Page 13: ...AGS Simplex AGS Duplex Instruction book 11...
Page 16: ...Service diagram AGS Simplex 1 ph typical Instruction book 14...
Page 46: ......
Page 47: ......
Page 48: ......