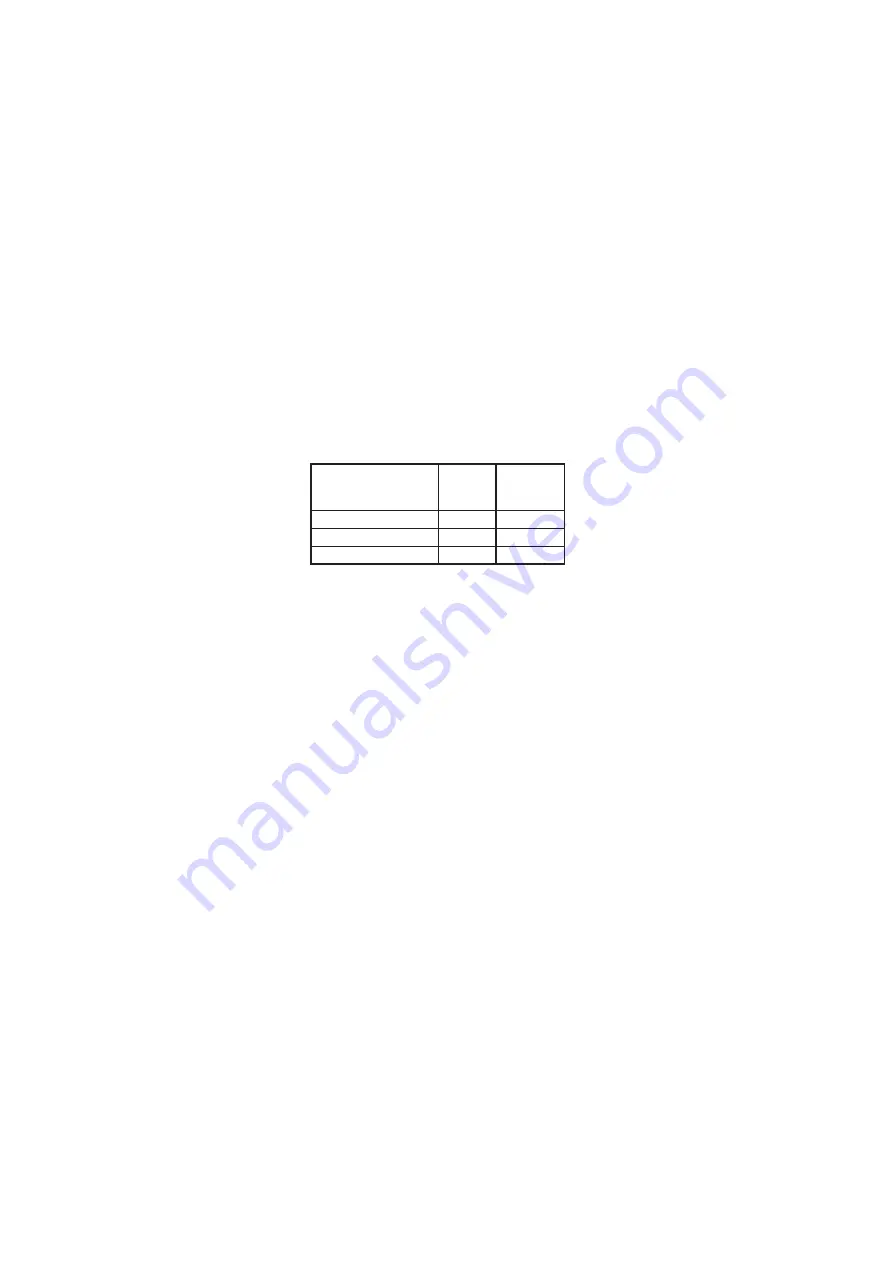
28
11 – Take the control panel and the top front panel
of the casing.
Boilers with basic control panel one
stage
11.1 – Fix the control panel (29) to the panel (30)
with the four screws supplied.
Straighten up the capillary tubes of the
thermostats and thermometer (31),
introduce the bulbs in the pocket (9) and
fix them with the incorporated clip.
Straighten up the capillary tube of the
pressure gauge (32) and fasten it to the
check valve (12). See Fig. 13.
Pass the electrical cables through the
cable entry (33) and wire the thermostats
to the control panel (29) in accordance
with the directions in the instructions for
the burner.
The door switch (7) must be connected in
series with the limit thermostat (35). See
Fig.4.
Boilers with basic control panel two
stages or digital KSF panel
11.1 – Open the control panel to gain access
to the terminal strip and to the capillary
tubes of the thermostats, thermometer
and pressure gauge.
Straighten the capillary tubes, passing
them across the base of the control panel
and through the knockouts in the top front
panel of the outer casing.
Fasten the base of the control station to
the panel with the screws provided.
In those models with a 2 stage basic control
panel (38 Fig.4) the thermostat bulbs
(39) and the bulb of the combined temp./
altitude gauge (40) will be introduced in
the pocket (9, fig. 14). The pocket located
in the socket (10, fig. 9) of the heating
flow pipe (11, fig. 9). Introduce and fix the
pressure sensor of the combined temp./
altitude gauge in the check valve (12)
located in the connection (13).
In those models equipped with KSF control
panel (70 Fig. 4), the safety thermostat
bulb (39 Fig 14a) and the temperature
sensor (78) will be introduced in the
pocked as showed on Fig. 14a, using the
spring (79) supplied with the KSF control
panel. Introduce and fix the pocket (9
Fig. 14a) in the socket (10 Fig. 9) of the
heating flow pipe (11, fig. 9).
It is recommended that heat conducting
paste be put in the pocket beforehand.
Fix the bulbs into the pockits using the
incorporated clips.
12 – Assemble the sides of the casing which
for the moment will be suspended by the
slots in the front (41) and rear (42) tubular
plates. See Fig. 15.
13 – Put the top central panel in place and by
simple pressure it will remain fixed to the
side panels.
14 – Put in place the top front and rear panels
which will rest on the central cover and will
remain fixed by the side clips.
15 – Open the boiler door and check the correct
position of the turbulators (43), which
should be level with the tubes at the front
of the boiler. Both sections should be
interconnected; should they have become
separated, pull the long section out a little,
give a quarter turn to the short section and
interconnect them again.
From the CPA 345-BT upwards, each
turbulator consists of two sections: a long
one which should remain in the final part of
the tube and a shorter one of stainless steel
which should be level with the tube at the
front of the boiler.
16 – Assemble the burner on the boiler door. If the
burner is not made by
BAXI , you should
check that the flame tube (44) surpasses the
ceramic fibre (45) by at least 20 mm. See Fig. 16.
Important:
Fill with rock wool or ceramic fibre (45) Fig. 16
the space which might remain between the flame
tube (44) and the insulating fibre (45) of the door.
17 – Make the fuel connection to the burner.
18 – Electrical connection
The installation should include a circuit
breaker or other omnipolar disconnect switch
to isolate all power supply to the boiler.
The connection of external appliances should
be done through approved wiring harness
type ES-NOSW5-F.
Basic control panel (one stage
operation)
The electrical connection between the burner
and the boiler thermostats will be carried out in
accordance with the instructions for the burner.
The door switch will be connected in series with
the limit thermostat.
Basic control panel (two stage
operation)
Control panel supply voltage: 220/230 V~, 50 Hz.
The components which can be connected to the
control panel and their maximum power input are
the following:
Component
Control
Panel
Terminal
Max.
power
Input
Pump
5-6
1000 W
Burner
14-6
1000 W
Storage cylinder
4-7
2800 W
However, the total electrical load of components
must not exceed 2,800 W.
KSF digital control panel
In the manuals of the KSF panel (70 Fig.4), you
will find a complete information about features and
heating installations can be managed with this
panel, which has specific components like fuse
(72), overtemperature lookout indicator (71) and
the control unit with LCD screen (73).
Electrical Connection Between the
Control Panel and Burner
See fig. 17 to 23
See legend in fig. 20
Electrical components of the Gas Train must be
connected according to burner instructions.
Legend. See Fig. 19.
19 – Burners with an air pressure test point (47)
Fig. 24 will have to be connected to the
boiler pressure test point (55) using a flexible
silicone hose (56). The pressure test point
screw should be removed before-hand.
20 – Check that there is no foreign body in the
combustion chamber. Fix the inspection
window assembly on the door (57). Fig. 24.
21 – Proceed to start up and adjust the burner,
making sure that all valves are open and that
the pump operates correctly.
22 – Start up the boiler and check for leak
tightness of flue gases with the burner at
full output. Should leak tightness not be
complete, re-tighten the nut or door clamp
nearest to the zone where the gases escape.
Having achieved complete gas-tightness,
tighten all the backnuts (6) on the hinge
side, one against the door (48) and the other
against the hinge (49). Fig.6. Do the same on
the side of the clamps, remembering, once
tightened (2) to lock the position with the
existing Allen screw (50) Fig.25.
23 – Immediately after proceed to assemble the
door casing. First open the door by undoing
the clamps. Then unscrew the arms of the
clamps.
CPA 55-BT to CPA 230-BT boilers
23.1 – Remove the burner temporarily without
needing to disconnect the oil and electricity
supplies.
23.2 – Undo the inspection window assembly.
Position the casing on the door and fix it
to this with the four screws supplied (51).
Fig. 26.
23.3 – Replace the arms of the clamps and the
inspection window assembly.
23.4 – Replace and fix the burner on the door.
CPA 290-BT to CPA 1740-BT boilers
23.1 – The door casing is supplied in two parts. To
assemble them, a light pressure is enough
for the upper (52) Fig. 26 and lower pins to
enter the housing clip. It is not necessary
to remove the burner.
23.2 – Join the two parts of the casing with the
upper screws (53) and the two lower screws
(54) provided. Position the casing on the
door and fix it to this with the four screws
(51) provided.
23.3 – Replace the arms of the door clamps.
Operation
Checks and steps to follow for starting up the
boiler and the installation.
Preliminary operations
– Check that the installation is full of water, vented
and a pressure of 0,5 bar above the static head
of the installation, at least.
– Start up the pump or pumps. Check that they
are turning.
– Bleed the air from the installation and radiators.
– In sealed & pressurised systems, refill with
water until the adjustable pointer is slightly
above the position of the fixed one.
– Close the boiler door, tightening it with the
clamps until they come up against the backnuts
(2) incorporated.
First lighting
– Follow the instructions which are supplied with
the burner.
– Set the control thermostat (34) Fig. 4 to
about 80 °C and check that this and the limit
thermostat operate correctly.
– The two stage basic control panel (38), is
prepared for controlling the burner in two stages,
and therefore incorporates two control thermos-
tats (34) Fig. 4. The thermostat regulated to
lower temperatures controls the second stage,
whilst the other, which is regulated to higher
temperatures, controls the first stage.
– Vent the installation again and check that the
radiators warm up satisfactorily.
Important recommendations
– If there is danger of freezing, add some anti-
freeze product to the water.
– Keep the same amount of water in the system
at all times; water should only be added when
topping up is absolutely necessary.
– Uncontrolled topping up with water may cause
limescale deposits in the boiler, damage it
seriously and reduce its performance.
– We recommend that the properties of the water
in the system be:
pH between
7.5 and 8.5.
Hardness:
8 to 12 French degrees (*).
(*) One French degree is equivalent to 1 gram of
calcium carbonate per 100 litres of water.
– Any work on the boiler or the installation must
be performed by qualified personnel.
Summary of Contents for CPA 1045-BT
Page 33: ...33...