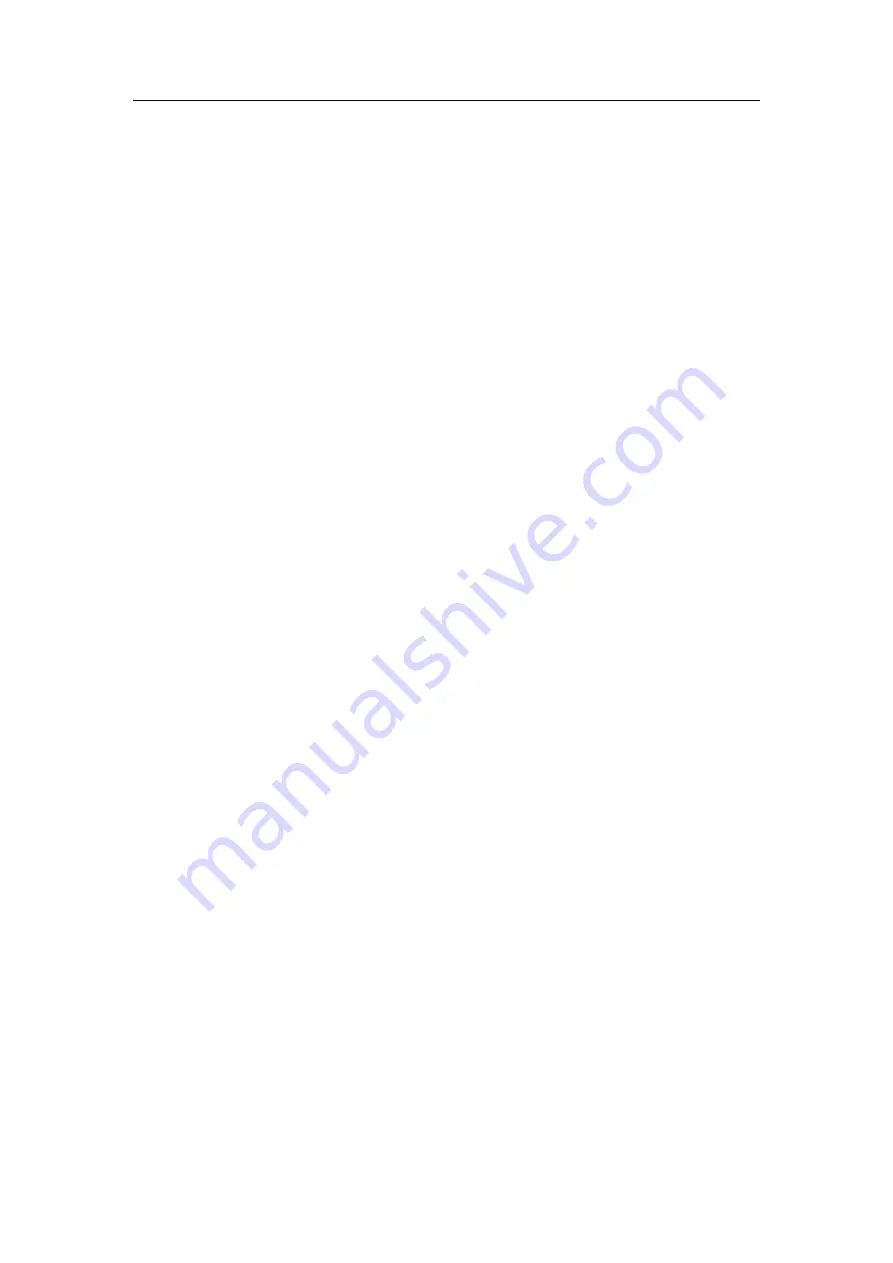
Operation
53
4.6 Electronic control system
Reading the fault code via the diagnostic switch:
Press the diagnostic switch (diagnostic lamp comes on), and then release to reset the
diagnostic switch (diagnostic lamp turns off)
The diagnostic lamp flashes and reports the fault code
Repeat step 1
for several times, the subsequent fault codes will be shown one by one.
When the first fault code is repeated, it indicates that all the fault codes have been read
Check the "List of fault codes" to find the explanation corresponding to each fault code
and you can determine the current fault.
Please check the code sheet at
6.5.2 Diagnostic Fault Codes List.