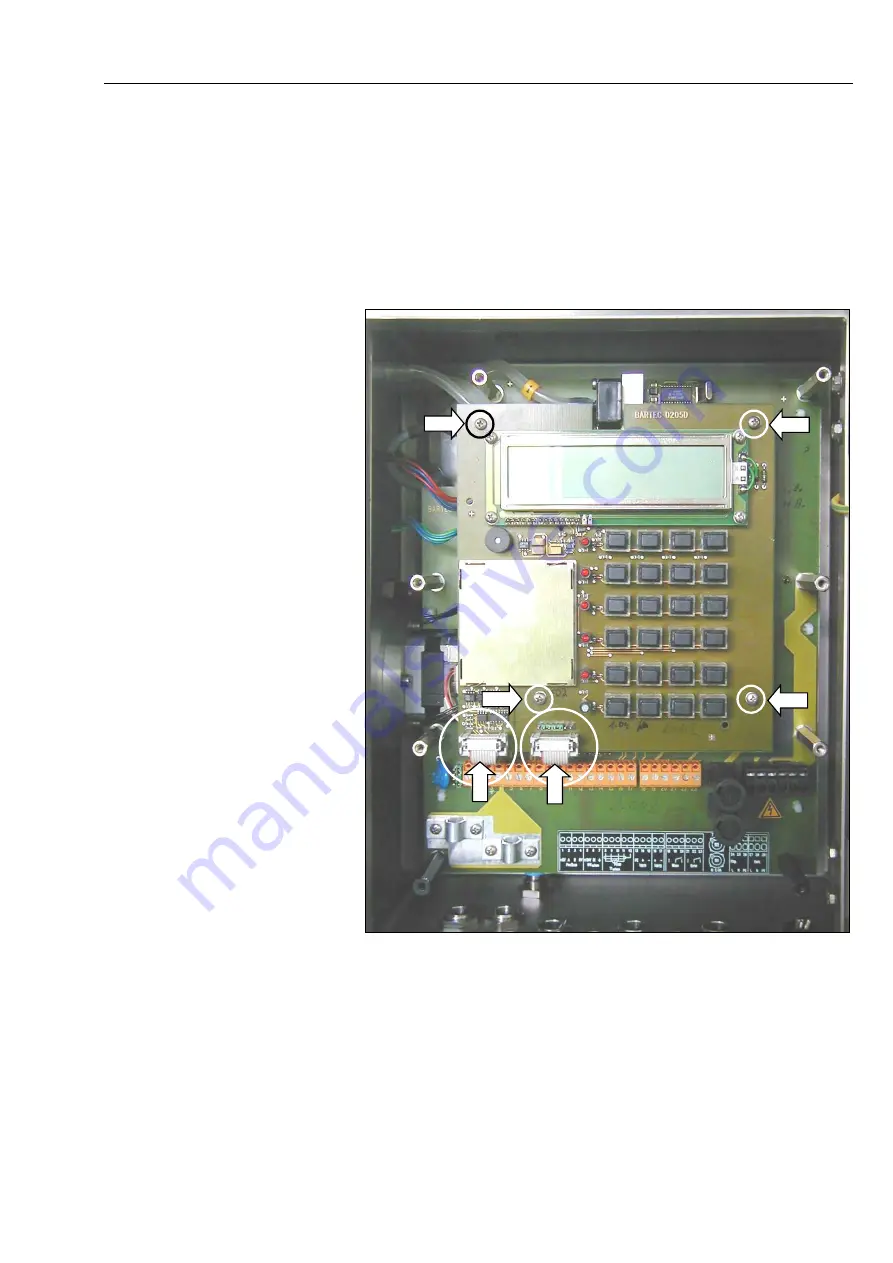
Maintenance
83
Operating Instructions HYGROPHIL® H 4230-12 BA 060207
6.10
Replacing the Display-/ Profibus-
board
Disconnect the device from power supply before starting any work at the
electronics.
Observe the safety precautions according to chapter 2.
Disconnect the two connectors and unscrew the four attachment screws.
Take the board carefully out and insert the replacement board.
Fix the board with the four screws and reconnect the two connectors.
Summary of Contents for HYGROPHIL H 4230-12 Ex Zone II
Page 2: ......
Page 30: ...System description 24 Operating Instructions HYGROPHIL H 4230 12 BA 060207...
Page 34: ...Safety precautions 28 Operating Instructions HYGROPHIL H 4230 12 BA 060207...
Page 66: ...Programming 60 Operating Instructions HYGROPHIL H 4230 12 BA 060207...
Page 112: ...Operating Instructions HYGROPHIL H 4230 12 BA 060207...