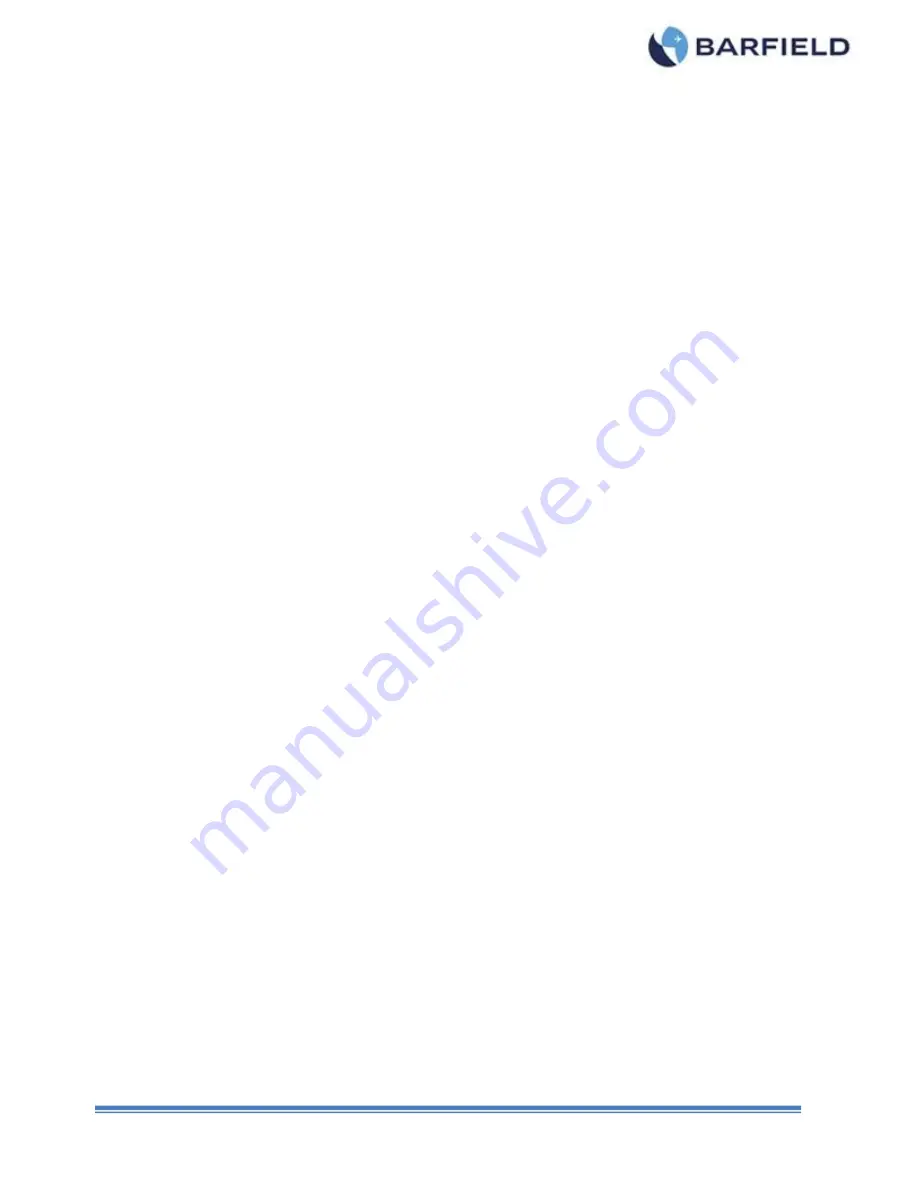
56-101-01178 Revision K
Page | 50
D. Testing the Aircraft Static System
CAUTION
: Observer all safety precautions detailed in the AMM and or CMM.
CAUTION
: The AMM or CMM procedure should always be recognized as the primary
authority and this manual should be recognized as a secondary aide. As such
the primary objective of this manual is to provide instruction relevant to
general Test Set operation while the AMM or CMM dictates the specific test
process, sequences and values.
1. Ensure the 1811NG is powered ON. Wait for Initialization to be completed, the system
to be safe at Ground and the display to indicate “Vented”.
Note:
If required, select Go To Ground and wait for the Test Set to indicate “Unit Safe at
Ground”.
2. Connect the hoses, both Static (Ps) and Pitot (Pt) to the 1811NG ports.
Note
: The Pitot (Pt) hose is not required to perform a Static system test, however it is
highly recommended as a safety precaution to protect the ASI from possible
damage.
3. If not already done, perform a Leak Test on the Test Set and hoses.
Note
: CAP the aircraft end of each hose.
4. Connect the hoses to the aircraft Static and Pitot ports.
Note
: Using the Pitot (Pt) hose for a Static system test will prevent the possibility of
damaging the ASI “Airspeed Indicator” which can happen if the Static (Ps)
channel is driven to a high altitude while testing and creates a large differential
pressure which could exceed the ASI full scale rating.
Note
: While testing the Static (Ps) system, the Target value for CAS should remain at
0 kts. While testing various altitude levels, the Test Set will maintain 0 kts (Qc =
0.000 inHg pressure differential) between the Ps and Pt ports which will ensure
the ASI is not damaged.
5. Verify that the alternate pneumatic system(s) (co-pilot, standby auxiliary, etc.) shares
the same pneumatic lines. If so, they must be sealed or isolated from the current
pneumatic system about to be tested.
6. If necessary, change the displayed parameters on the Test Set to those required. This
can be accomplished by selecting “Display Setup” followed by selecting the desired
aeronautical parameters.
7.
If necessary different units can be selected by selecting the icon “Units” from the Main
Menu.
8. Verify the limits selected are appropriate for the aircraft and/or Instruments that are
going to be tested.
9. If there is a height difference between the Test Set and the aircraft or instruments
about to be tested, enter the Altitude Correction.
a)
From Main Menu, select the blue icon “page 2”. A panel opens with four selections.
b)
Touch “Setup 1”. The “Limits View/Select” screen is displayed.
c)
Select “Altitude Correction” and touch “OK”. A numbered keypad appears.
d) Input the altitude difference (with aircraft / instruments higher than Test Set, the value
would be entered as a (+) positive number).