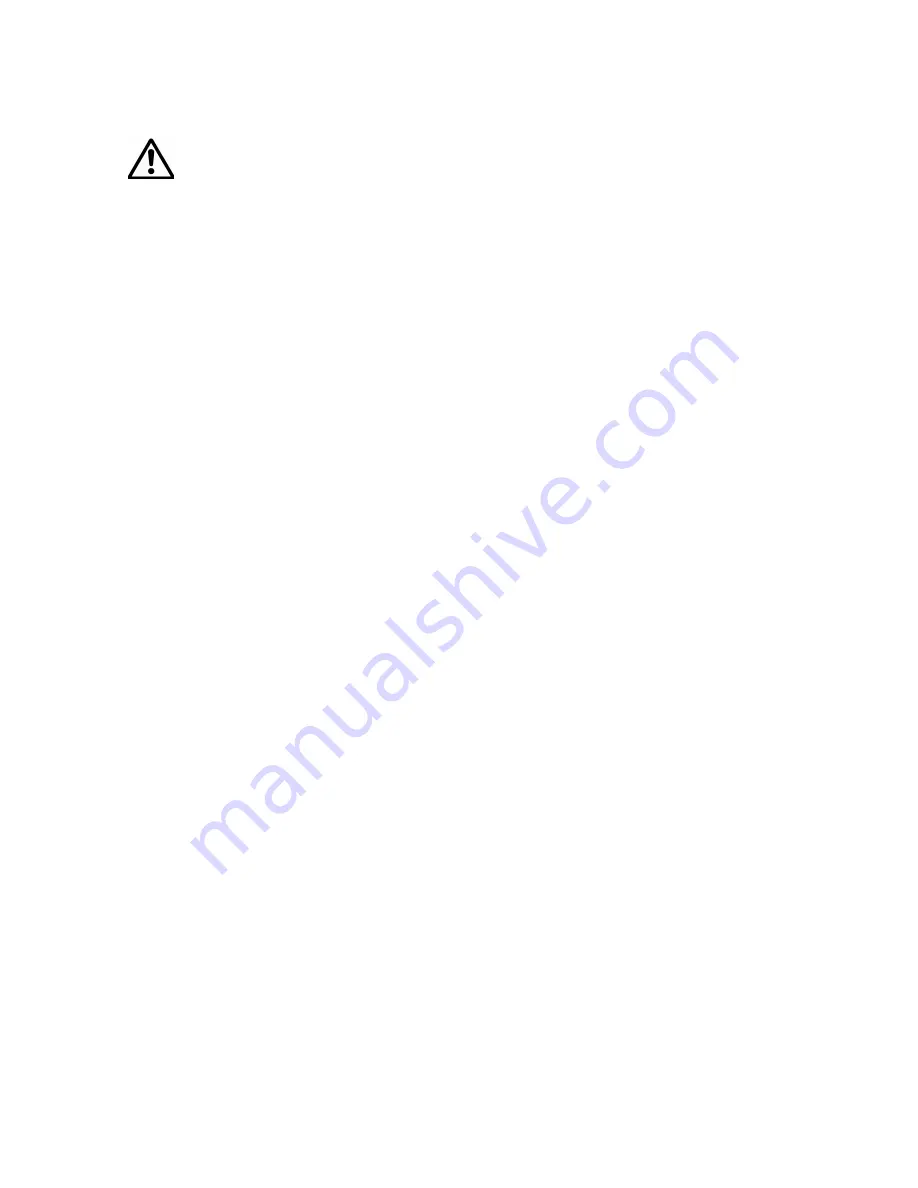
18
5.8 Digital input configuration – Modbus control mode (Optional – P1-12 = 4)
The following table defines the digital input functionality when the drive is in Modbus control mode.
P2-01
Digi input 1 function
Digi input 2 function
Digi input 3 function
Analog input function
0..2,4
6..9,
13..16,18
O : Stop (Disable)
C : Run (Enable)
No effect
No effect
3
O : Stop (Disable)
C : Run (Enable)
O : Forward
C : Reverse
O : Master speed ref
C : Preset speed 1
Digital input 1 must be closed
to enable the drive
Digi input 3
Analog input
Preset value
Open
Open
Preset speed 1
Closed
Open
Preset speed 2
Open
Closed
Preset speed 3
5
O : Stop (Disable)
C : Run (Enable)
O : Master speed ref
C : Preset speed
Closed
Closed
Preset speed 4
10
O : Stop (Disable)
C : Run (Enable)
O : Master speed ref
C : Digital speed ref
External trip input :
O : trip C : OK
11
O : Stop (Disable)
C : Run (Enable)
O : Master speed ref
C : Preset speed 1
External trip input :
O : trip C : OK
12
O : Stop (Disable)
C : Run (Enable)
O : Preset speed 1
C : Master speed ref
External trip input :
O : trip C : OK
17
O : Stop (Disable)
C : Run (Enable)
O : Master speed ref
C : Bipolar analog input
O : Master / analog speed
C : Preset speed 1
19
O : Stop (Disable)
C : Run (Enable)
O : Master speed ref
C : 2
nd
analog input
No effect
20,21
O : Stop (Disable)
C : Run (Enable)
2
nd
digital output :
Drive healthy = +24V
O : Master speed ref
C : Preset speed 1
22
O : Stop (Disable)
C : Run (Enable)
2
nd
digital output :
Drive healthy = +24V
External trip input :
O : trip C : OK
Digital input 1 must be closed
to enable the drive
Notes:
If P2-19 = 2 or 3, drive can only be started / stopped by closing / opening digital input 1. If P2-19 = 0 or 2,
the master speed reference will be automatically reset to zero each time when drive is stopped.
5.9 Real-time
monitoring
parameters
Parameter group zero provides access to internal drive read-only parameters for monitoring purposes.
Par Description
Display
range
Explanation
P0-01
Bipolar analog input value
-100%...100%
100% = max input voltage
P0-02 2
nd
analog input value
0..100%
100% = max input voltage
P0-03
Speed controller reference
-500%...500%
100% = Base frequency (P1-09)
P0-04
Digital speed ref (digi pot)
- P1-01 … P1-01
Speed displayed in Hz / rpm
P0-05
Torque controller reference
0 ...200%
100% = motor rated torque
P0-06
User PID ref input
0..100%
PID controller reference value
P0-07
User PID feedback
0..100%
PID controller feedback value
P0-08
User PID error input
0..100%
Reference – Feedback
P0-09 User
PID
P-term
0..100%
Proportional
component
P0-10
User PID I-term
0..100%
Integral component
P0-11
User PID D-term
0..100%
Differential component
P0-12
User PID output
0..100%
Combined output
P0-13
Output Torque
0…200%
100% = motor rated torque
P0-14
Magnetising current
A rms
Magnetising current in A rms
P0-15
Rotor current
A rms
Rotor current in A rms
P0-16
Field strength
0..100%
Magnetic field strength
P0-17
Stator resistance
Ohm
Phase – Phase stator resistance
P0-18
Stator inductance
H
Stator inductance in Henry
P0-19
Rotor resistance
Ohm
Calculated rotor resistance
P0-20
DC bus voltage
V dc
Internal DC bus voltage
P0-21 Drive
temperature
o
C Internal
drive
temperature
P0-22
Supply voltage L1 – L2
V rms, ph-ph
Phase – phase supply voltage
P0-23
Supply voltage L2 – L3
V rms, ph-ph
Phase – phase supply voltage
P0-24
Supply voltage L3 – L1
V rms, ph-ph
Phase – phase supply voltage
P0-25
Estimated Rotor speed
Hz or rpm
Applies to vector modes only
P0-26
kWh meter
0.0 … 999.9 kWh
Cumulative energy consumption
P0-27
MWh meter
0.0 … 60 000 MWh
Cumulative energy consumption
P0-28
Software ID, IO processor
eg “1.00”, “493F”
Version number and checksum
P0-29
Software ID, Motor control
eg “1.00”, “7A5C”
Version number and checksum
P0-30
Drive serial number
000000 … 999999
00-000 … 99-999
Unique drive serial number
eg 540102 / 24 / 003
7
3. Electrical
Installation
3.1 Safety
Electric shock hazard!
Disconnect and
ISOLATE
the Optidrive before attempting
any work on it. High voltages are present at the terminals and within the drive for up
to 10 minutes after disconnection of the electrical supply.
•
Optidrives should be installed only by qualified electrical persons and in accordance with
local and national regulations and codes of practice.
•
The Optidrive has an Ingress Protection rating of IP20. For higher IP ratings, use a
suitable enclosure.
•
Where the electrical supply to the drive is through a plug and socket connector, do not
disconnect until 10 minutes have elapsed after turning off the supply
•
Ensure correct earthing connections, see diagram below
•
The earth cable must be sufficient to carry the maximum supply fault current which
normally will be limited by the fuses or MCB
3.2 Precautions
•
Ensure that the supply voltage, frequency and number of phases (single or three phase)
correspond to the rating of the Optidrive as delivered
•
An isolator or similar should be installed between the power supply and the drive
•
Never connect the mains power supply to the Optidrive output terminals UVW
•
Protect the drive by using slow-blow HRC fuses or an MCB located in the mains supply
to the drive
•
Do not install any type of automatic switchgear between the drive and the motor
•
Wherever control cabling is close to power cabling, maintain a minimum separation of
100 mm and arrange crossings at 90
o
•
Ensure that screening or armouring of power cables is effected in accordance with the
connections diagram below
•
Ensure that all terminals are tightened to the appropriate torque (see table, left)
Connect drive according to the following diagram, ensuring that motor terminal box
connections are correct. There are two connections in general : Star and Delta. It is essential
to ensure that the motor is connected in accordance with the voltage at which it will be
operated. For more information, refer to the following diagram
For recommended cabling and wiring sizing, refer to section 7.4.
It is recommended that the power cabling should be 3-core or 4-core PVC-insulated
screened cable, laid in accordance with local industrial regulations and codes of practice.
The ground terminal of each Optidrive should be individually connected DIRECTLY to the
site earth (ground) bus-bar (through the filter if installed) as shown. Optidrive ground
connections should not loop from one drive to another, or to, or from any other equipment.
Ground loop impedance must conform to local industrial safety regulations. To meet UL
regulations, UL approved ring crimp terminals should be used for all earth wiring
connections.
Summary of Contents for OPTIDRIVE PLUS 3 GV
Page 1: ......