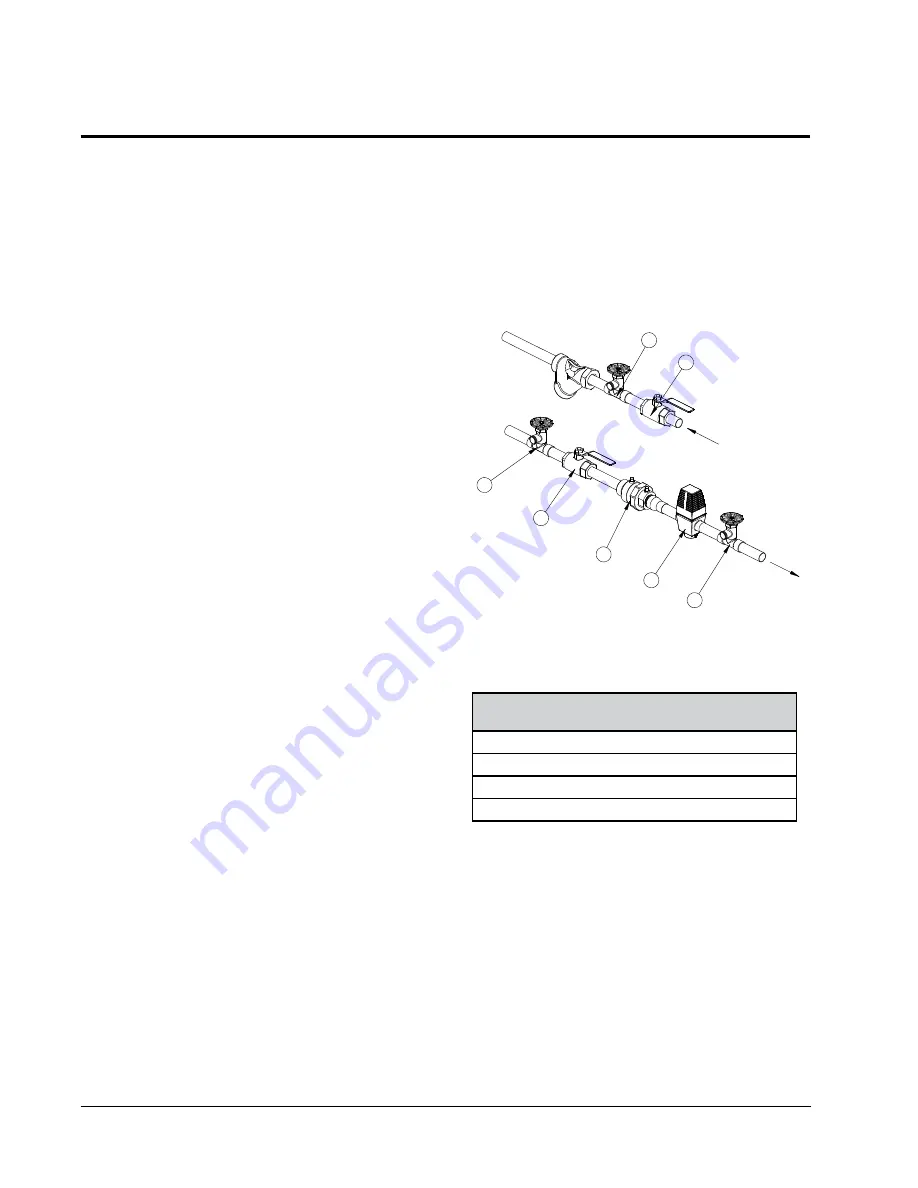
Manual 2100-738C
Page
56 of 73
OPEN LOOP
(Well System Applications)
NOTE
It is highly recommended on ground water
systems (pump & dump) that a cupronickel
coaxial coil is utilized on the source side of
the system. Not doing so may void the product
warranty due to aggressive/corrosive/highly
oxygenated water attacking a copper coaxial
water coil.
Water Connections
It is very important that an adequate supply of clean,
noncorrosive water at the proper pressure be provided
before the installation is made. Insufficient water,
in the heating mode for example, will cause the
low pressure switch to trip, shutting down the heat
pump. In assessing the capacity of the water system,
it is advisable that the complete water system be
evaluated to prevent possible lack of water or water
pressure at various household fixtures whenever the
heat pump turns on. All plumbing to and from the unit
is to be installed in accordance with local plumbing
codes. The use of plastic pipe, where permissible,
is recommended to prevent electrolytic corrosion
of the water pipe. Because of the relatively cold
temperatures encountered with well water, it is strongly
recommended that the water lines connecting the unit
be insulated to prevent water droplets form condensing
on the pipe surface.
Refer to Figure 36. Slow closing
Solenoid Valve (6)
with a 24V coil provides on/off control of the water
flow to the unit. Refer to the wiring diagram for correct
hookup of the valve solenoid coil.
Constant Flow Valve (7)
provides correct flow of water
to the unit regardless of variations in water pressure.
Observe the water flow direction indicated by the arrow
on the side of the valve body. Table 12 shows the flow
rate of each valve. Two constant flow rate valves may be
installed in parallel to increase the flow. For example,
when a 8603-007 (6 GPM) and 8603-011 (5 GPM)
are installed in parallel the total flow will be 11 GPM.
Strainer (5)
installed upstream of
constant flow valve
(7)
to collect foreign material which would clog the flow
valve orifice.
Figure 36 shows the use of
shutoff valves (9 and 11)
,
on the in and out water lines to permit isolation of the
unit from the plumbing system should future service
work require this. Globe valves should not be used as
shutoff valves because of the excessive pressure drop
inherent in the valve design. Instead use gate or ball
valves as shut-offs so as to minimize pressure drop.
Drain cocks (8 and 10)
and tees have been included to
permit acid cleaning the refrigerant-to-water coil should
6
10
11
8
9
12
7
MIS-2749
Figure 36
Piping Diagram
such cleaning be required. See
Water Corrosion
section on page 58.
Drain cock (12)
provides access to the system to check
water flow through the constant flow valve to ensure
adequate water flow through the unit. A water meter is
used to check the water flow rate.
TABLE 12
Constant Flow Valves
The pressure drop through the constant flow valve will
vary depending on the available pressure ahead of the
valve. Unless minimum of 15 psig is available
immediately
ahead of the valve, no water will flow.
Part No.
Min. Available
Pressure PSIG
Flow Rate GPM
CFV-5
15
5
CFV-6
15
6
CFV-7
15
7
CFV-9
15
9