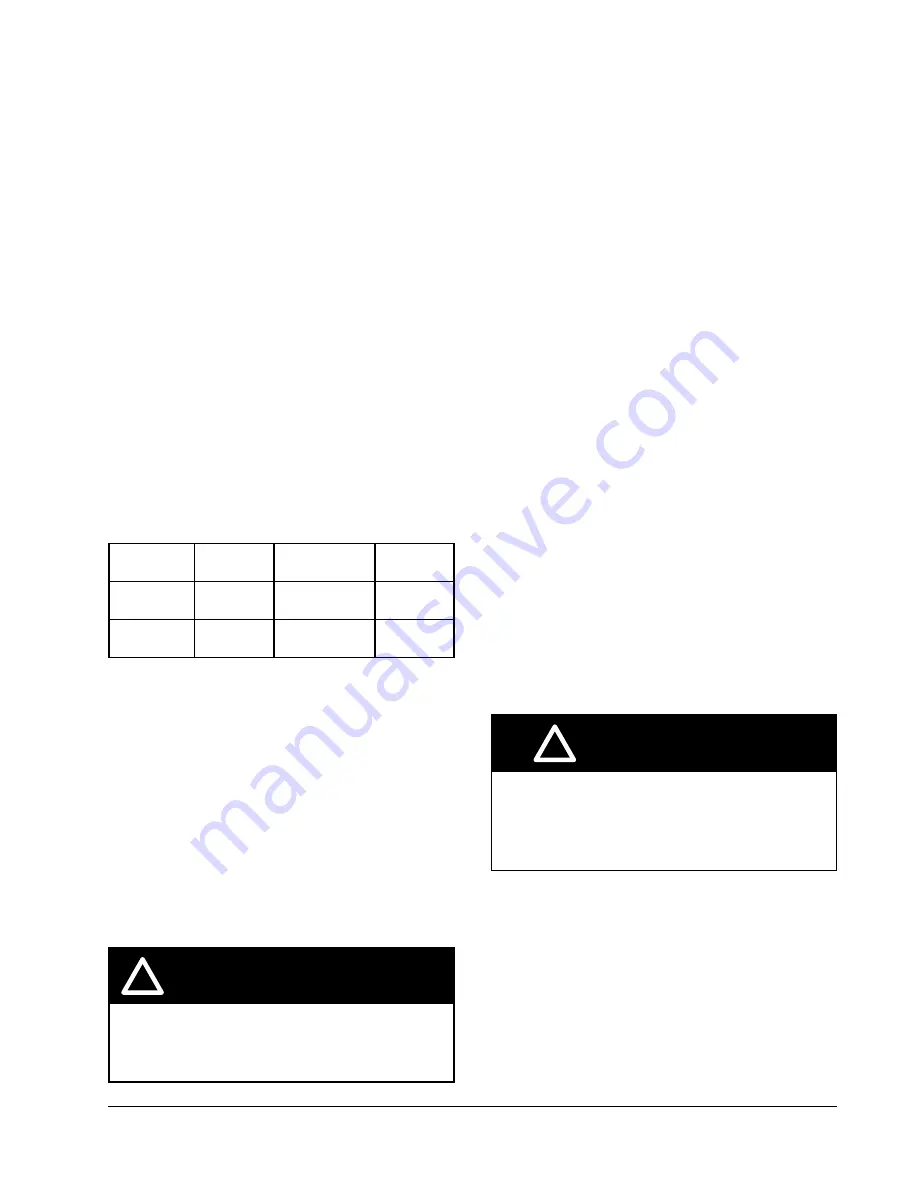
Manual 2100-701
Page
11 of 16
CONTROL WIRING
The ERV-F comes from the factory with the low voltage
control wires connected to the wall mount low voltage
terminal strip. Care must be taken when deciding
how to control the operation of the ventilator. When
designing the control circuit for the ventilator, the
following requirements must be met.
Control Requirements
1. Indoor blower motor will automatically run
whenever the ERV-F is run.
2. Select the correct motor speed tap in the ERV-F.
Using Table 2, determine the motor speed needed
to get the desired amount of ventilation air
needed. For instance, do not use the high speed
tap on a ERV-F*3 if only 250 CFM of ventilation
air is needed. Use the low speed tap instead (see
VENTILATION AIRFLOW
for information on
moving the speed taps). Using the high speed tap
would serve no useful purpose and significantly
affect the overall efficiency of the air conditioning
system. System operating cost would also increase.
TABLE 2
Ventilation Air (CFM)
Model
High Speed
(Black)
Medium Speed
(Blue)
Low Speed
(Red)
ERV-FA2
ERV-FC2
250
225
200
ERV-FA3
ERV-FC3
400
325
250
3. Run the ERV-F only during periods when the
conditioned space is occupied. Running the
ERV-F during unoccupied periods wastes energy,
decreases the expected life of the ERV-F and can
result in a large moisture buildup in the structure.
The ERV-F removes 60-70% of the moisture in the
incoming air, not 100% of it. Running the ERV-F
when the structure is unoccupied allows moisture
to build up in the structure because there is little
or no cooling load. Thus, the air conditioner is not
running enough to remove the excess moisture
being brought in. Use a control system that
in some way can control the system based on
occupancy.
!
IMPORTANT
Operating the ERV-F during unoccupied
periods can result in a buildup of moisture
in the structure.
Recommended Control Sequences
Several possible control scenarios are listed below:
1. Use a programmable electronic thermostat with
auxiliary terminal to control the ERV-F based
on daily programmed occupancy periods. Bard
markets and recommends Bard Part No. 8403-
060 programmable electronic thermostat for air
conditioner and heat pump applications.
2. Use a motion sensor in conjunction with a
mechanical thermostat to determine occupancy
in the structure. Bard recommends Bard Model
CS9B*-**** CompleteStat for this application.
3. Use a CO
2
control with dry contacts to energize the
ERV-F when CO
2
levels rise above desired settings.
4. Use a DDC control system to control the ERV-F
based on a room occupancy schedule to control
the ERV-F.
5. Tie the operation of the ERV-F into the light switch.
The lights in a room are usually on only when
occupied.
6. Use a manual timer that the occupants turn to
energize the ERV-F for a specific number of hours.
7. Use a programmable mechanical timer to energize
the ERV-F and indoor blower during occupied
periods of the day.
VENTILATION AIRFLOW
The ERV-FA* and ERV-FC* are equipped with a
3-speed motor to provide the capability of adjusting
the ventilation rates to the requirements of the specific
application by changing motor speeds (see Table 2).
!
WARNING
Open disconnect to shut all power OFF
before changing motor speeds. Failure to
do so could result in injury or death due to
electrical shock.
The units are set from the factory with the exhaust
blower on the low speed and the intake blower on
medium speed. Moving the speed taps located in the
control panel can change the blower speed of the
intake and exhaust (see Figure 6 on page 12).