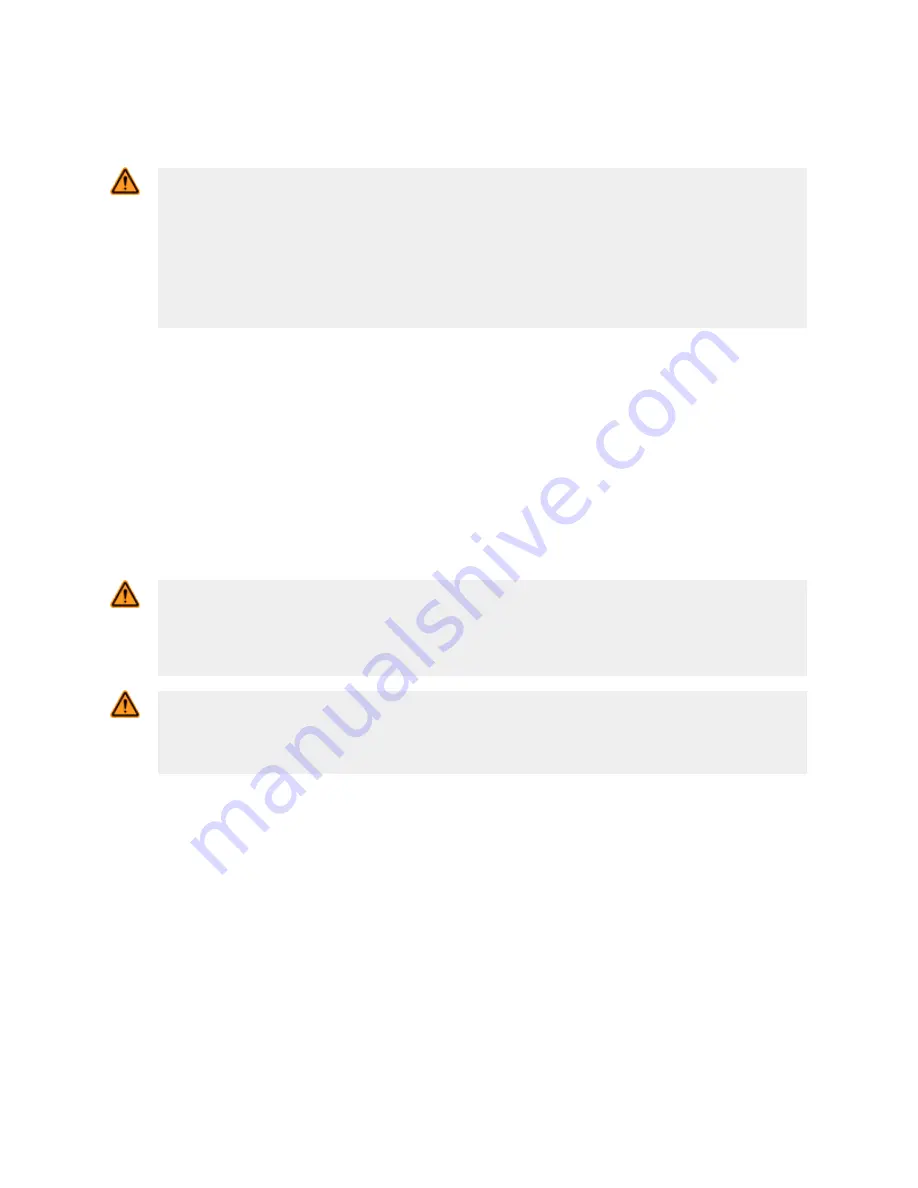
To mute the primary safeguard appropriately, the design of a muting system must:
1. Identify the non-hazardous portion of the machine cycle
2. Involve the selection of the proper muting devices
3. Include proper mounting and installation of those devices
WARNING: Mute and Bypass
Mute and Bypass operations must be done in a way that minimizes personnel risk. Implement
the following when creating mute and bypass applications:
•
Guard against unintended stop signal suspension by using one or more diverse-redundant
mute sensor pairs or a dual channel key-secured bypass switch.
•
Set reasonable time limits (no longer than needed) for the mute and bypass functions.
Failure to follow these rules could lead to an unsafe condition that may result in serious
injury or death.
The Safety Controller can monitor and respond to redundant signals that initiate the mute. The mute then suspends the
safeguarding function by ignoring the state of the input device to which the muting function has been assigned. This allows
an object or person to pass through the defined area of a safety light screen without generating a stop command. This
should not be confused with blanking, which disables one or more beams in a safety light screen resulting in larger
resolution.
The mute function may be triggered by a variety of external devices. This feature provides a variety of options to design
the system to meet he requirements of a specific application.
A pair of muting devices must be triggered simultaneously (within 3 seconds of one another). This reduces the chance of
common mode failures or defeat. Directional muting, in which sensor pair 1 is required to be blocked first, also may reduce
the possibility of defeat.
At least two mute sensors are required for each muting operation. The muting typically occurs 100 ms after the second
mute sensor input has been satisfied. One or two pairs of mute sensors can be mapped to one or more safety input
devices so that their assigned safety outputs can remain On to complete the operation.
WARNING: Muting Limitations
Muting is allowed only during the non-hazardous portion of the machine cycle.
A muting application must be designed so that no single component failure can prevent the stop
command or allow subsequent machine cycles until the failure is corrected.
WARNING: Mute Inputs Must Be Redundant
It is not acceptable to use a single switch, device, or relay with two N.O. contacts for the
mute inputs. This single device, with multiple outputs, may fail so that the System is muted at an
inappropriate time. This may result in a hazardous situation.
Optional Muting Attributes
The Muting Sensor Pair Input and the Muting Block have several optional functions that can be used to minimize an
unauthorized manipulation and the possibility of an unintended mute cycle.
Mute Enable (ME)
The Mute Enable input is a non-safety-rated input. When the input is closed, the Safety Controller allows a mute condition
to occur; opening this input while the System is muted will have no effect.
Typical uses for Mute Enable include:
•
Allowing the machine control logic to create a period of time for muting to begin
•
Inhibiting muting from occurring
•
Reducing the chance of unauthorized or unintended bypass or defeat of the safety system
The optional Mute Enable function may be configured to ensure that a mute function is permitted only at the appropriate
time. If a Mute Enable input device has been mapped to a Muting Block, the safety input device can be muted only if the
mute enable switch is in the enable (24V dc) state at the time the mute cycle is started. A mute enable input device can be
mapped to one or more Muting Blocks.
XS/SC26-2 Safety Controller
37