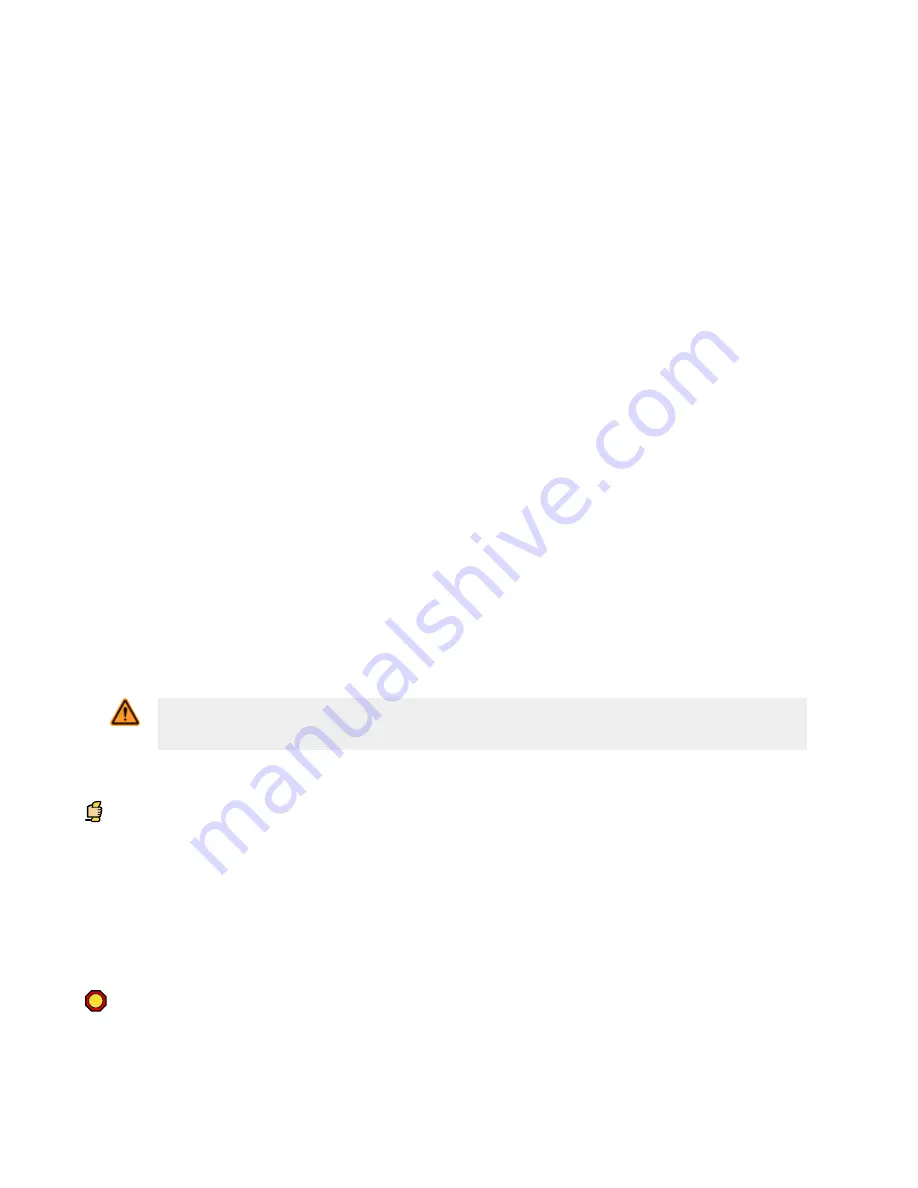
Rope pull emergency stop switches have many of the same requirements as emergency stop push buttons, such as
positive (direct) opening operation, as described by IEC 60947-5-1. See
on page 72 for
additional information.
In emergency stop applications, the rope pull switches must have the capability not only to react to a pull in any direction,
but also to a slack or a break of the rope. Emergency stop rope pull switches also need to provide a latching function that
requires a manual reset after actuation.
Rope (Cable) Pull Installation Guidelines
ANSI NFPA 79, ANSI B11.19, IEC/EN 60204-1, and ISO 13850 specify emergency stop requirements for rope (cable) pull
installations, including the following:
•
Rope (cable) pulls must be located where emergency shutdown is required
•
Rope (cable) pulls must be continuously operable, easily visible, and readily accessible. Do not mute or bypass
•
Rope (cable) pulls must provide constant tension of the rope or cable pull
•
The rope or cable pull, as well as any flags or markers, must be colored Red
•
The rope or cable pull must have the capability to react to a force in any direction
•
The switch must:
◦
Have a self-latching function that requires a manual reset after actuation
◦
Have a direct opening operation
◦
Detect a slack condition or a break of the rope or cable
Additional installation guidelines:
•
The wire rope should be easily accessible, red in color for E-Stop functions, and visible along its entire length.
Markers or flags may be fixed on the rope to increase its visibility
•
Mounting points, including support points, must be rigid and allow sufficient space around the rope to allow easy
access
•
The rope should be free of friction at all supports. Pulleys are recommended. Lubrication may be necessary.
Contamination of the system, such as dirt, metal chips or swarf, etc, must be prevented from adversely affecting
operation
•
Use only pulleys (not eye bolts) when routing the rope around a corner or whenever direction changes, even
slightly
•
Never run rope through conduit or other tubing
•
Never attach weights to the rope
•
A tensioning spring is recommended to ensure compliance with direction-independent actuation of the wire rope
and must be installed on the load bearing structure (machine frame, wall, etc.)
•
Temperature affects rope tension. The wire rope expands (lengthens) when temperature increases, and contracts
(shrinks) when temperature decreases. Significant temperature variations require frequent checks of the tension
adjustment
WARNING: Failure to follow the installation guidelines and procedures may result in the ineffectiveness
or non-operation of the Rope Pull system and create an unsafe condition resulting in a serious injury or
death.
6.4.4 Enabling Device
An enabling device is a manually operated control which, when continuously actuated, allows a machine cycle to be
initiated in conjunction with a start control. Standards that cover the design and application of enabling devices include:
ISO 12100-1/-2, IEC 60204-1, ANSI/NFPA 79, ANSI/RIA R15.06, and ANSI B11.19.
The enabling device actively controls the suspension of a Stop signal during a portion of a machine operation where a
hazard may occur. The enabling device permits a hazardous portion of the machine to run, but must not start it. An
enabling device can control one or more safety outputs. When the enable signal switches from the Stop state to the Run
state, the Controller enters the Enable mode. A separate machine command signal from another device is needed to start
the hazardous motion. This enabling device must have ultimate hazard turn Off or Stop authority.
6.4.5 Protective (Safety) Stop
A Protective (Safety) Stop is designed for the connection of miscellaneous devices that could include safeguarding
(protective) devices and complementary equipment. This stop function is a type of interruption of operation that allows an
orderly cessation of motion for safeguarding purposes. The function can be reset or activated either automatically or
manually.
XS/SC26-2 Safety Controller
73