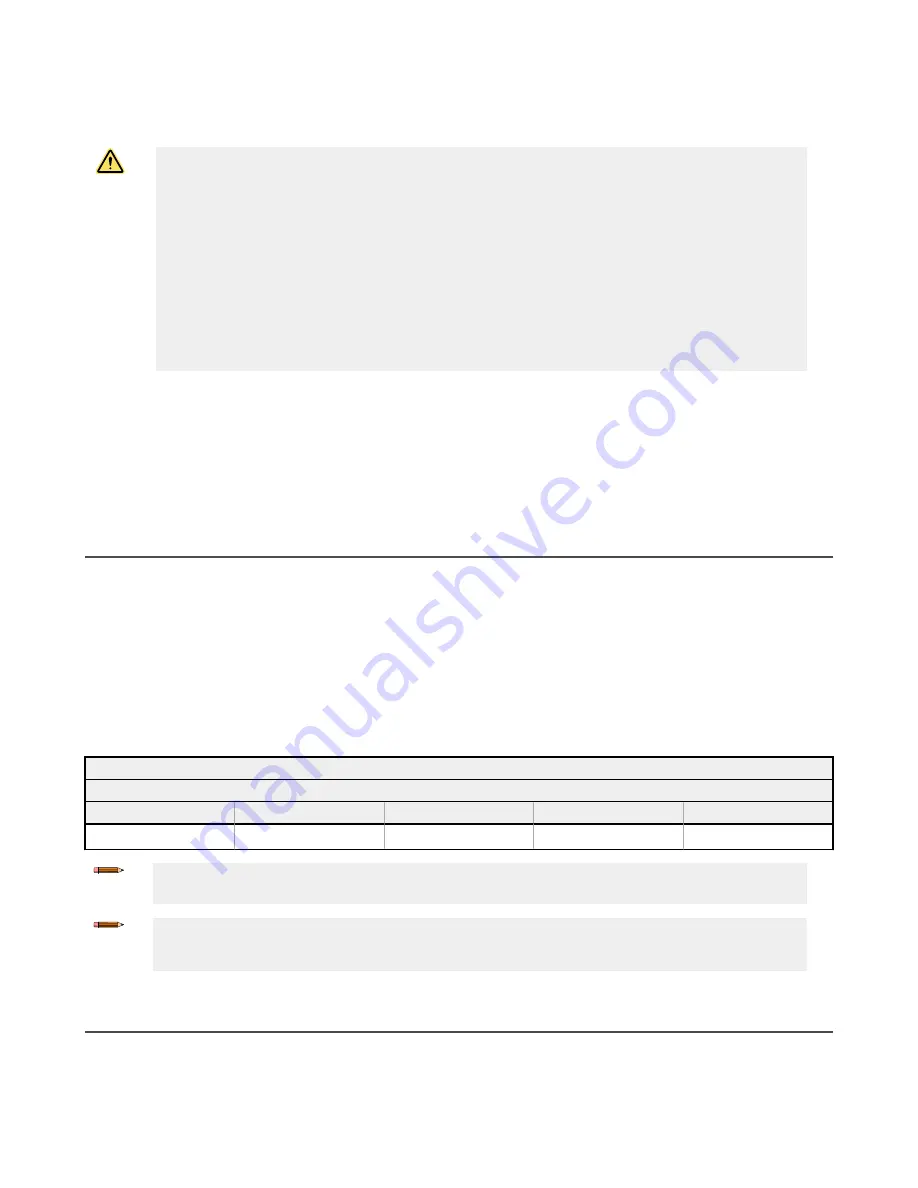
6 Electrical Installation and Testing
The following are the main steps to electrically install the S4B components and interface with the guarded machine.
WARNING:
•
Read this Section Carefully Before Installing the System
•
Failure to follow these instructions could result in serious injury or death.
•
If all mounting, installation, interfacing, and checkout procedures are not followed properly, this
Banner device cannot provide the protection for which it was designed.
•
The user is responsible for ensuring that all local, state, and national laws, rules, codes, or
regulations relating to the installation and use of this control system in any particular application
are satisfied. Ensure that all legal requirements have been met and that all technical installation
and maintenance instructions contained in this manual are followed.
•
The user has the sole responsibility to ensure that this Banner device is installed and interfaced to
the guarded machine by Qualified Persons, in accordance with this manual and applicable safety
regulations. A Qualified person is a person who, by possession of a recognized degree or
certificate of professional training, or who, by extensive knowledge, training and experience, has
successfully demonstrated the ability to solve problems relating to the subject matter and work.
1. Routing cordsets and making initial electrical connections (see
on page 28 and
on page 30).
2. Apply power to each emitter/receiver pair (see
Initial Electrical Connections
on page 30).
3. Perform an Initial Checkout Procedure (see
on page 30).
4. Make all electrical interface connections to the guarded machine (see
Electrical Connections to the Guarded Machine
on page 34).
5. Perform a commissioning checkout procedure (see
on page 36).
6.1 Routing Cordsets
Attach the required cordsets to the sensors, and route the sensor cables to the junction box, electrical panel, or other
enclosure in which the other safety-related parts of the control system are located. This must be done per local wiring code
for low-voltage dc control cables and may require installation of electrical conduit.
See
on page 47 for selection of Banner supplied cables.
The S4B is designed and manufactured to be highly resistant to electrical noise and to operate reliably in industrial settings.
However, extreme electrical noise may cause a random Trip condition; in extreme cases, a Lockout is possible.
Emitter and receiver wiring is low voltage; routing the sensor wires alongside power wires, motor/servo wires, or other high
voltage wiring may inject noise into the S4B System. It is good wiring practice, and sometimes may be required by code, to
isolate emitter and receiver cables from high-voltage wires and to avoid routing cables close to sources of noise.
Sensor cabling and any interconnect wiring should have an insulation temperature rating of at least 90 °C (194 °F).
Table 3: Maximum machine interface cable length versus total load current (OSSDs)
Maximum Machine Interface Cordset Length
Total Load Current (OSSD 1 + OSSD 2)
0.1 A
0.25 A
0.5 A
0.75 A
1.0 A
95.7 m (314 ft)
78 m (256 ft)
54.9 m (180 ft)
42.1 m (138 ft)
34.1 m (112 ft)
Note:
Emitter and receiver power (current) requirements are accounted for. The above values represent
additional current draw that must be accounted for.
Note:
Maximum cordset lengths are intended to ensure that adequate power is available to the S4B when
the supply is operating at +20 V DC. Values in the previous table are worse case. Contact Banner
Engineering if there are any questions.
6.2 Scan Code Selection
The emitter and receiver may be configured to one of two Scan Codes (1 or 2).
A receiver recognizes light only from an emitter with the same scan code. Both the emitter and its corresponding receiver
must have the same scan code setting. The scan code must be configured with power off because the DES4E-.. RD to M12
cordset assemblies must be removed from the units.
S4B Safety Light Curtain
28
www.bannerengineering.com - Tel: + 1 888 373 6767