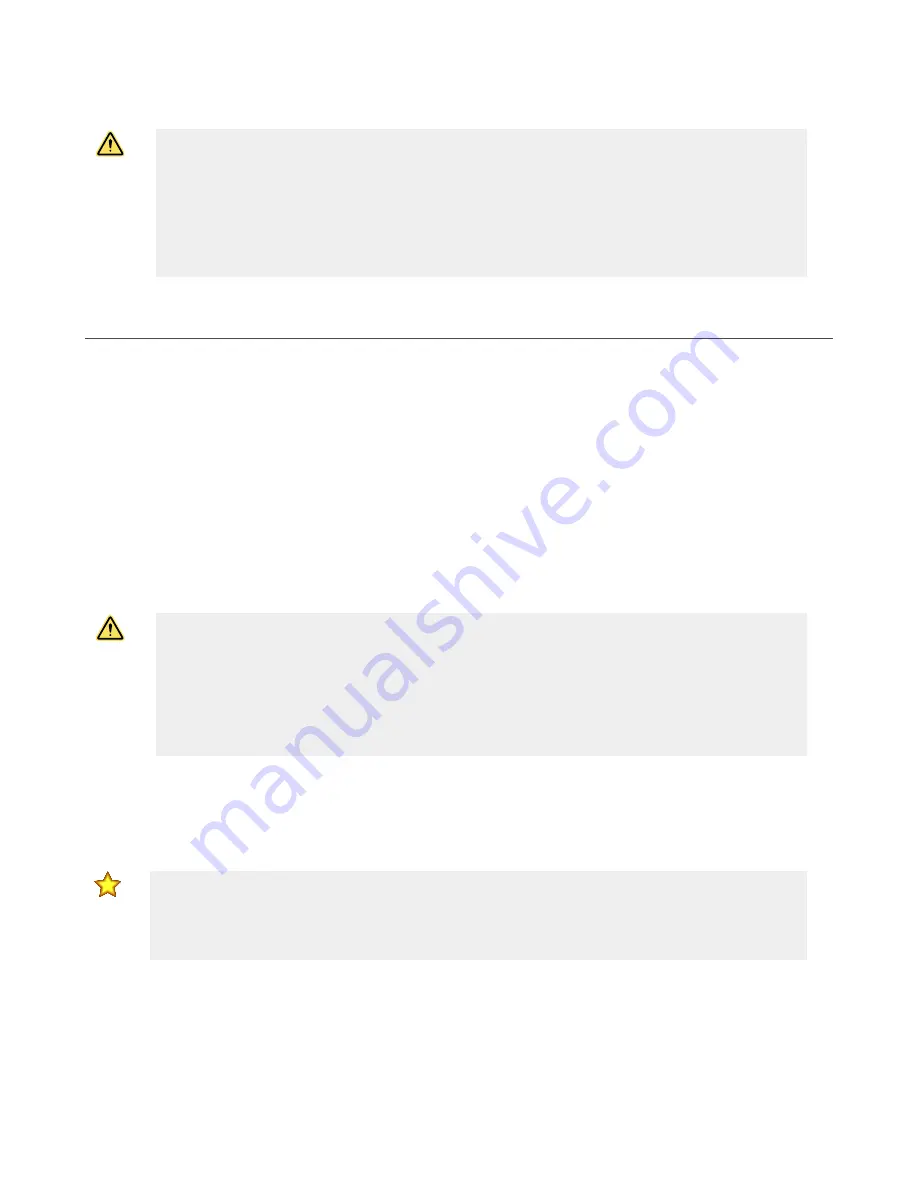
Additional supplemental safeguarding may be required to prevent clearance or trapping hazards (for example, a safety mat
as an area guard between the robot, the turntable, and the conveyor).
WARNING:
•
The hazard must be accessible only through the sensing field
•
Incorrect system installation could result in serious injury or death.
•
The installation of the S4B must prevent any individual from reaching around, under, over or
through the defined area and into the hazard without being detected.
•
See OSHA CFR 1910.217, ANSI B11.19, and/or ISO 14119, ISO 14120 and ISO 13857 for
information on determining safety distances and safe opening sizes for your guarding device.
Mechanical barriers (for example, hard (fixed) guarding) or supplemental safeguarding might be
required to comply with these requirements.
5.5 Reset Switch Location
The S4B has a trip output (auto power-up and automatic reset) that turns the OSSD outputs ON when the defined area is
unobstructed (clear). Per application requirements, a latch response requiring a manual reset to a power-up condition or after
an interruption has cleared the defined area might be required. The latch function can be provided by interfacing the S4B
OSSD outputs to the machine's safety-related control system, a safety controller (such as SC10-2roe or XS/SC26-2), or
safety module (such as the UM-FA-9A/11A).
The system or device providing the latch/reset function must conform to the level of performance required by the risk
assessment. In applications requiring Control Reliability and/or ISO 13849-1:2015 Categories 3 or 4 and PL d or e, it is
recommended that a monitored manual reset (for example, open-closed-open action), such that a shorted or tied-down
button cannot cause a reset be used.
The reset switch must be mounted at a location that complies with the warning and guidelines below.
If any
hazardous areas are not in view from the switch location, additional means of safeguarding must be provided. The switch
should be protected from accidental or unintended actuation (for example, through the use of rings or guards).
A key-actuated reset switch provides some operator or supervisory control, as the key can be removed from the switch and
taken into the guarded area. However, this does not prevent unauthorized or inadvertent resets due to spare keys in the
possession of others, or additional personnel entering the guarded area unnoticed. When considering where to locate the
reset switch, follow the guidelines below.
WARNING:
•
Install reset switches properly
•
Failure to properly install reset switches could result in serious injury or death.
•
Install reset switches so that they are accessible only from outside, and in full view of, the
safeguarded space. Reset switches cannot be accessible from within the safeguarded space.
Protect reset switches against unauthorized or inadvertent operation (for example, through the use
of rings or guards). If there are any hazardous areas that are not visible from the reset switches,
provide additional safeguarding.
All reset switches must be:
•
Outside the guarded area
•
Located to allow the switch operator a full, unobstructed, view of the entire guarded area while the reset is performed
•
Out of reach from within the guarded area
•
Protected against unauthorized or inadvertent operation (such as through the use of rings or guards).
Important:
Resetting a safeguard must not initiate hazardous motion. Safe work procedures require a
start-up procedure to be followed and the individual performing the reset to verify that the entire hazardous
area is clear of all personnel before each reset of the safeguard is performed. If any area cannot be
observed from the reset switch location, additional supplemental safeguarding must be used: at a
minimum, visual and audible warnings of machine start-up.
S4B Safety Light Curtain
www.bannerengineering.com - Tel: + 1 888 373 6767
19