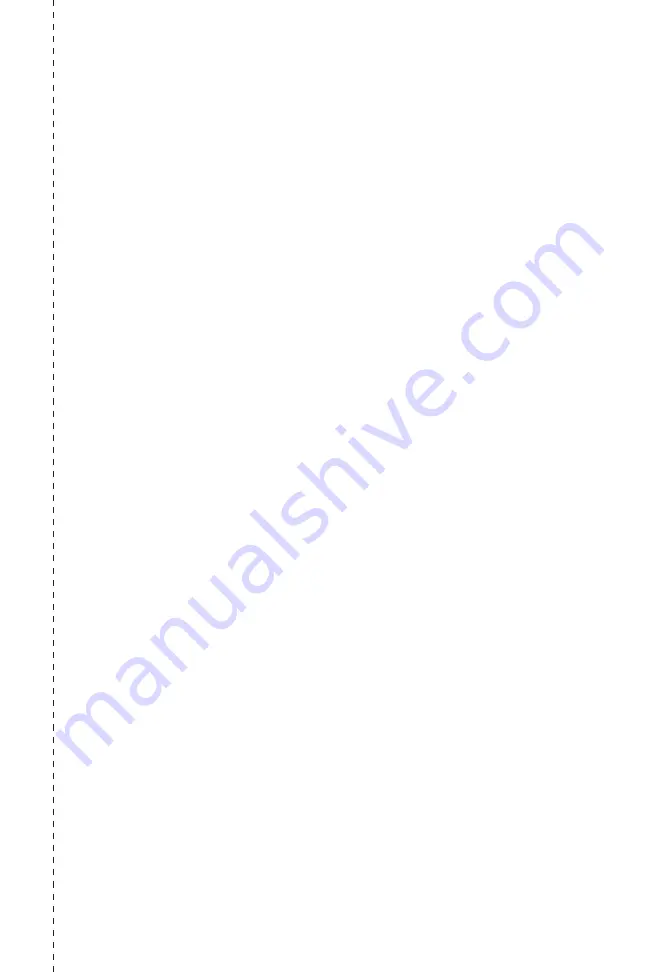
Copyright 2/17 FORM #WV-124
I have inspected this equipment and find it in correct working condition. To the best of my knowledge,
the customer and his/her personnel are aware of, and agree to the above procedures.
Signed: ________________________________________________________ Date: ______________
(Dealer Representative)
The equipment has been thoroughly checked by the above named dealer representative, and I am
satisfied with his/her instructions. I have also read, understand, and agree to reverse side of page.
Signed: ________________________________________________________ Date: ______________
(Customer)
WARRANTY VALIDATION FORM
(STUMP GRINDER)
PURCHASER / OWNER INFORMATION:
Company Name __________________________________ Contact Name _____________________
Mailing/Street Address _______________________________________ City _______________________
State ___________________ Zip Code _______ Country ______________ Telephone Number ( __ ) ________
E-mail ____________________________ Machine Model No. _______ Date Put Into Service ______
Machine Serial No. ____________________ Machine Work Order No. ________ Machine Hours _______
Engine Make _________________ Engine Serial No. __________________ Machine Color _______
DEALER / SELLER INFORMATION:
Dealer/Seller Name _______________________________ Contact Name _____________________
Mailing/Street Address _______________________________________ City _______________________
State ___________________ Zip Code _______ Country ______________ Telephone Number ( __ ) ________
IMPORTANT - WARRANTY WILL BE DEEMED NULL AND
VOID IF THIS FORM IS NOT FILLED OUT COMPLETELY AND
ACCURATELY AND RETURNED TO THE CUSTOMER DATA
DEPARTMENT WITHIN 10 DAYS OF EQUIPMENT DELIVERY
1. _____ The customer has received instruction and fully understands all operational, safety and maintenance requirements
of the equipment.
2. _____ The customer has received instruction and fully understands that everyone within 100 feet of the machine must
wear proper personal safety equipment including hard hat, face shield, safety glass, gloves, ear protection and/or other
items per OSHA and ANSI requirements.
3. _____ The customer has received instruction and fully understands the equipment maintenance schedules and procedures.
The customer understands that it is their responsibility to perform scheduled maintenance that includes periodic relief valve
adjustments,retighteningallfastenersasneeded,periodiccleaningofflowdivider,clutchandbeltadjustments,andotheritems.
4. _____ The customer has received instruction and fully understands not to reach near the cutter head with hands or feet
ortobelocatedneardebrisfieldwithenginerunning.
5. _____ The customer has received instruction and fully understands that the operators must always be located within
easy reach of all control and shut down devices.
6. _____ The customer has received instruction and fully understands to not start grinding a stump without checking for power
lines, water lines, sewer lines, phone lines, etc.
7. _____ The customer has received instruction and fully understands the purpose of and how to operate the shut
down/shut-off devices, and will not attempt to override any safety devices or guards.
8. _____ The customer has received instruction and fully understands that before performing any maintenance on the
machine the ignition key must be removed, the cables must be completely disconnected from the battery, the cutter head
must have come to a complete stop, and the cutter head lock must be installed. The customer understands they must
allow the necessary time for the cutter head to come to a complete stop before opening the cutter head guard or start any
maintenance or service procedures. If applicable the customer has received instruction and fully understands the purpose
of the beltshield inspection hole and that they are never to attempt any maintenance or service procedures until visually
confirmingthebeltshavecometoacompletestop.
9. _____ The customer has received instruction and fully understands the machine is not to be operated without the factory
approved cutter head guard in place, the machine is not to be operated with any type of make shift cutter head guard, and
the machine is not to be operated under any circumstances with the cutter guard open or unsecured.
10. _____ The customer has reviewed and fully understands limited warranty, and all written and visual instructions.
11. _____ The customer has received instruction and fully understands that warranty will not apply if the machine is operated
with replacement parts or equipment not manufactured or recommended by Bandit Industries, Inc.
12. _____ The customer has received, been advised, and understands the manuals, and the Safety/Service video supplied
with the grinder. A video is supplied for equipment models as available.
13. _____ All Danger, Warning and Operational decals are properly displayed on equipment and fully understood by customer.
14. _____ The customer has been instructed, understands, and agrees that all potential operators must: See the supplied
video, be instructed on all the Danger, Warning and Operational decals, read the manual and follow the procedures.
Customer Data Department
6750 Millbrook Road
Remus, MI, USA 49340
Phone: (800) 952-0178 in USA
Phone: (989) 561-2270
Fax: (989) 561-2273
Website: www.banditchippers.com