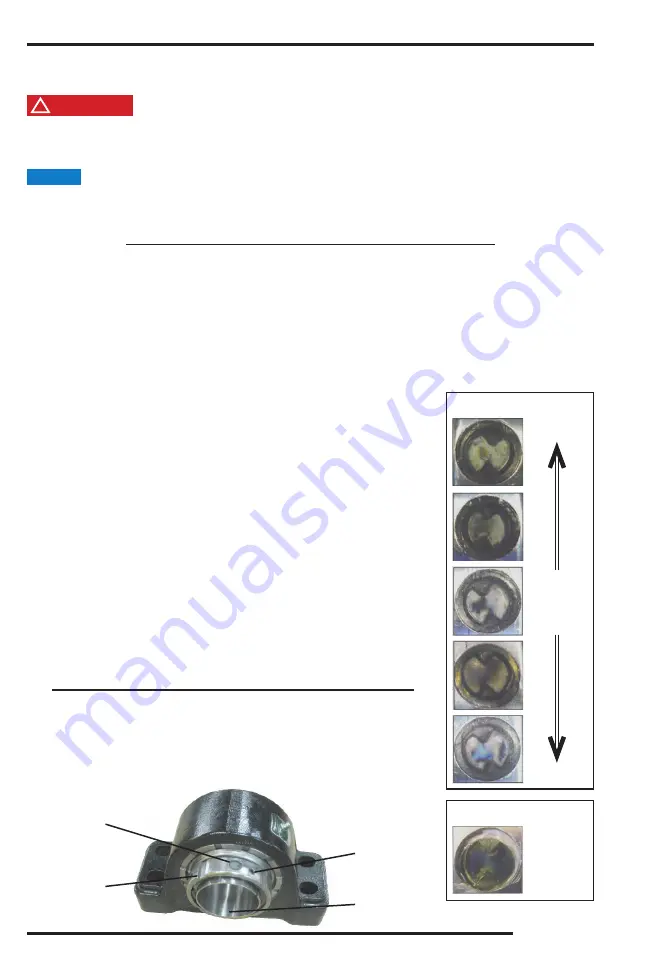
Bandit
68
Copyright 12/17
MODEL 18XP/1590
MAINTENANCE
SERVICING / CHANGING CHIPPER BEARING
(FOR REXNORD® 6000 SERIES)
DANGER
!
STEPS TO REPLACE A CHIPPER BEARING
STEPS TO REMOVE A CHIPPER BEARING
1. Back out the locknut set screws.
2. Loosen the locknut with an impact spanner wrench or a soft drift pin in
a counter-clockwise direction until the bearing adapter assembly
becomes completely loose.
3. Remove the mounting bolts.
4. The bearing should slide freely off the shaft.
Visual
Indicator
Set
Screw
Locknut
Adapter
Sleeve
Proper installation is critical to bearing life. Improper installation could cause premature or immediate
failure. Particular care must be taken not to create a preload on the bearings while tightening the locknut.
Use of a good quality torque wrench is also important to your safety as well as proper bearing installation.
NOTICE
Figure 2
Over
Tightened
Before attempting any type of maintenance, disengage clutch, wait for the disc/drum to come to a complete
stop, turn off engine, remove the ignition key, make sure the ignition key is in your possession, install the
disc/drum lock pin, and disconnect the battery.
1. Clean the shaft so that it is free from burrs and rust. Do not coat the chipper shaft or the bore of the bearing
adapter with a preservative, lubricant, or other substance such as Loctite
®
.
2. If the adapter sleeve happens to get removed from the bearing during installation, the locking pin in the
adapter sleeve must be aligned with the keyway in the inner bore. See Figure 3.
3.
Off set the bearing on the shaft about 1/8” (3.2 mm) from its intended position towards the base, so when
the bearing is tightened up on the shaft, the bolt holes will line up.
4. Hand tighten the locknut to take out the looseness, the use a hook type spanner wrench to bring the
locknut to a snug fi t.
5. Mark the locknut and chipper drum shaft with a grease pencil or a dark marker. Use a soft steel drift pin
and a hammer to drive the locknut clockwise one full turn. Make sure the
adapter sleeve does not turn on the shaft while tightening. If the adapter
sleeve is turning, it can be held by placing a hook type spanner wrench in
the split area of the sleeve.
6. Look at the visual indicators on the locknut. At least one of the visual
indicators should show an indication of defl ection. See Figure 1. If at least
one indicator does not show indication of tightness after 1/4 turn beyond
the fi nal adjustment, the locknut needs to be completely loosened and start
over with step 3.
7. If the entire indicator window becomes completely blue with the possibility of
yellow and red fringing, the bearing has been over-tightened. See Figure 2. The
locknut needs to be completely loosened and start over with step 3.
8. Loosen all the bearing bolts to release the preload on the bearings if there is
any. Keep the weight of the drum head off the bearings while bolting down.
Bolt both bearings down and torque the bolts to 220 ft.-lbs. (298 Nm).
9. If the drum head does not spin freely, there is a preload on the bearings.
The bearing will need to be completely loosened and steps 3 through 8
need to be repeated.
10. Tighten the set screws in the locknut to 13-15 ft.-lbs. (18-20 Nm) of torque
with a 5/32” hex type torque wrench.
Figure 1
Acceptable
Tightness
Range