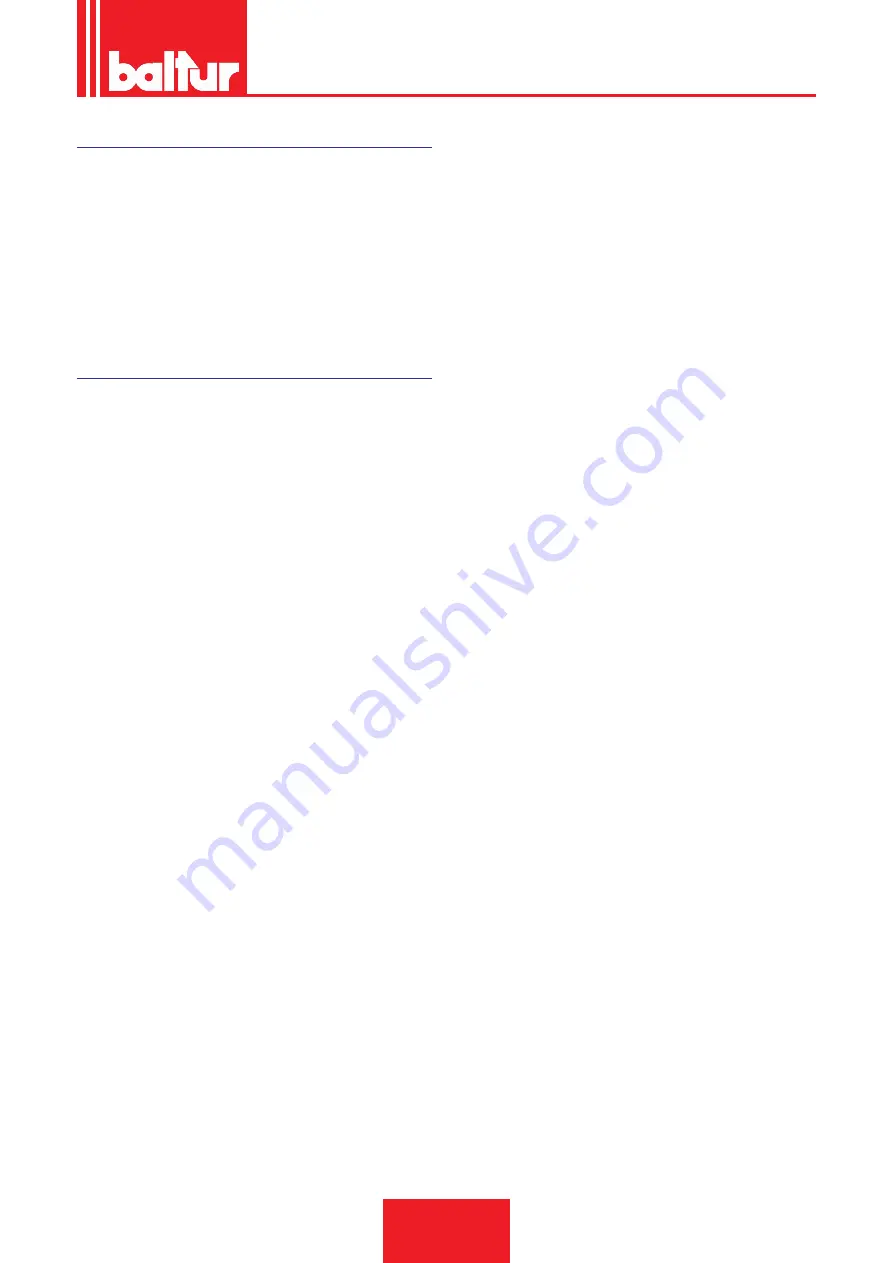
ENGLISH
15 / 28
0006081514_201711
OPERATING DESCRIPTION
Burner operation is fully automatic; it starts up by enabling the main
switch and the control panel switch.
Burner operation is managed by the electronic command and control
equipment.
The “lock-out” position is a safety position that the burner automatically
assumes when a burner or system component is not working properly.
The burner may stay in the lock-out position without any time limits.
To “reset” the control box operation, press the reset button.
Lock-outs may also be caused by temporary faults; in these cases if it
is reset, the burner will start up without any difficulties.
STARTING UP AND REGULATION
•
Bleed out the air contained in the gas piping, with due precautions
and with doors and windows open.
• Wait the time necessary for the gas in the room to disperse outside.
Re-connect the burner to the gas pipeline.
•
Check that thee voltage on the mains meets the manufacturer
requirements and that all electrical connections made at the
installation site are performed properly as illustrated in our wiring
diagram.
•
Check that the discharge of combustion products through the boiler
gate and flue gate take places freely.
•
Check that there is water in the boiler and that the gate valves of
the system are open.
•
Make sure that the combustion head is long enough to enter the
furnace following the measure specified by the boiler manufacturer.
•
Apply a pressure gauge of appropriate scale to the pressure intake
on the gas pressure switch. If the foreseen amount of pressure
allows it, it is better to use a water column instrument. Do not use
dial instruments for average pressures.
•
With the switch on the burner panel at the position “0” and the main
switch on, check, closing the contactor manually, that the motor
rotates in the right direction. If necessary, swap the two power
cables for the motor around to change the direction of rotation.
•
If using the inverter, see the specific instructions in the quick guide.
•
Now switch on the main switch. This powers on the control device,
and the programmer turns on the burner as described in the
chapter "Operation description". For burner adjustment, refer to the
instructions for the electronic cam supplied.
•
After having adjusted the “minimum”, (200) bring the burner to the
maximum, using the controls on the electronic cam keyboard.
•
We recommend that you check the combustion using the
appropriate instrument at all intermediate points on the modulation
route (from 200 to 999), checking the gas flow rate by reading the
meter.
•
It is essential to check, using an appropriate instrument, that the
percentage of carbon monoxide (CO) present in the fumes does
not exceed the limit set by the regulations in force at the time of
installation.
•
Now check the proper automatic operation of modulation. This
ensures that the equipment receives the signal from the electronic
modulation regulator, if the burner is the modulating model, or from
the second stage thermostat or pressure switch, if it is a two stage
progressive burner.
AIR PRESSURE SWITCH
The air pressure switch stops the equipment operation if air pressure
is not at the expected value.
The pressure switch must therefore be adjusted so that it is triggered
to close the NO contact (normally open) when the air pressure in the
burner reaches a particular value.
To ensure correct operation of the air pressure switch you must, with
burner on and in 1st stage, increase its regulation value until the
burner triggers and then it immediately “locks-out”.
Release the burner by pressing the appropriate button and readjust
the pressure switch until preventilation air pressure can be detected.
GAS PRESSURE CONTROL PRESSURE-SWITCHES
The gas pressure switches (minimum and maximum) prevent
the burner from operating when gas pressure is not between the
expected range.
The maximum pressure switch makes use of the NC (normally closed)
contact which is closed when the pressure switch detects a pressure
lower than its own setting.
Adjustment of minimum and maximum pressure values on the
pressure switches must be performed when testing the burner, on the
basis of the pressure measured in each case.
Summary of Contents for 67200010
Page 2: ......
Page 25: ...ITALIANO 23 28 0006081514_201711 SCHEMI ELETTRICI TBG 480 2000 ME ...
Page 26: ...ITALIANO 24 28 0006081514_201711 TBG 480 2000 ME ...
Page 27: ...ITALIANO 25 28 0006081514_201711 TBG 480 2000 ME ...
Page 28: ...ITALIANO 26 28 0006081514_201711 TBG 480 2000 ME ...
Page 30: ......
Page 53: ...ENGLISH 23 28 0006081514_201711 WIRING DIAGRAMS TBG 480 2000 ME ...
Page 54: ...ENGLISH 24 28 0006081514_201711 TBG 480 2000 ME ...
Page 55: ...ENGLISH 25 28 0006081514_201711 TBG 480 2000 ME ...
Page 56: ...ENGLISH 26 28 0006081514_201711 TBG 480 2000 ME ...
Page 58: ......
Page 59: ......