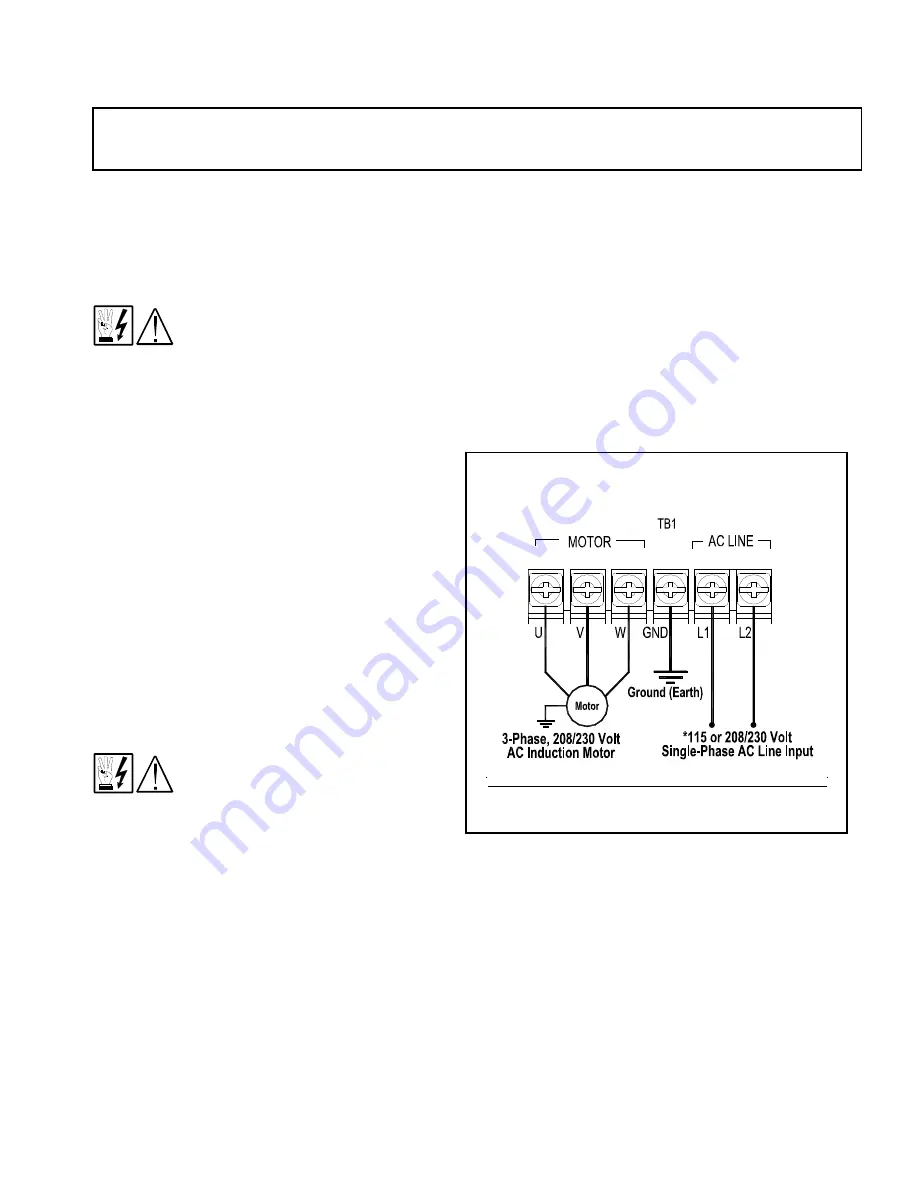
11
FIGURE 1 - QUICK-START CONNECTION
DIAGRAM
*For 115 VAC line, install jumper J1 (supplied).
Recommended Tightening Torque
lb-in (7), kg-cm (8)
2 QUICK-START INSTRUCTIONS
Important:
You must read these simplified instructions before proceeding. These instructions
are to be used as a reference only and are not intended to replace the details provided herein.
You must read the “ALL” Safety Warnings on, page 8, before proceeding.
Note: This drive contains bus capacitors which must be reconditioned if the drive has been in
storage for over 1 year. To recondition the bus capacitors, apply the AC line, with the main
speed potentiometer set to zero, for a minimum of 30 minutes.
See Figures 1 – 4, on pages 11 - 14. See Section 5 - Important Application Information, on
page 17.
WARNING! HIGH VOLTAGE IS PRESENT IN THIS DRIVE. DISCONNECT MAIN
POWER BEFORE MAKING CONNECTIONS TO THE DRIVE. TO PREVENT ACCIDENTAL
CONTACT WITH HIGH VOLTAGE, IT IS REQUIRED THAT THE COVER BE PROPERLY
INSTALLED AFTER ALL SETUP, CONNECTIONS, AND ADJUSTMENTS ARE COMPLETE.
THIS REDUCES ELECTRICAL SHOCK HAZARD. FAILURE TO OBSERVE THIS WARNING
COULD RESULT IN ELECTRICAL SHOCK OR ELECTROCUTION.
Note: It is recommended that both Feed-
Through Bushings (See Figure 4, on page
13) be used to connect the drive. If signal
wiring (for the Run/Fault Relay Output
Contacts or for a remote Main Speed
Potentiometer) is required, it is
recommended that the extra Feed-Through
Bushing (supplied with the drive) be used to
replace the center Hole Plug. Standard 3/4”
fittings (not supplied) can also be used in lieu
of the Feed-Through Bushings.
2.1 MOUNTING
INSTRUCTIONS:
See
Section 3, on page 15.
WARNING! DO NOT USE THIS
DRIVE IN AN EXPLOSION-PROOF
APPLICATION.
2.2
AC LINE INPUT CONNECTION:
Connect the single-phase AC line input to Terminal Block
TB1 (Terminals “L1”, “L2”), as shown in Figure 1. See Section 4.1, on page 15.
Application Note: Do not connect this drive to a GFCI.
Note: The drive is factory set for 208/230 Volt AC line input (Jumper J1 not installed). For 115
Volt AC line input, install Jumper J1 (supplied). See Section 6.1, on page 19.
2.3 AC LINE FUSING
: It is recommended that a fuse(s) or circuit breaker be installed in the AC
line. Fuse each conductor that is not at ground potential. For the recommended fuse size,
see Table 7, on page 5. Also see Section 4.1, on page 15.
2.4 GROUND
CONNECTION:
Connect the ground wire (earth) to Terminal Block TB1
(Terminal “GND”), as shown in Figure 1 and Table 9, on page 15.