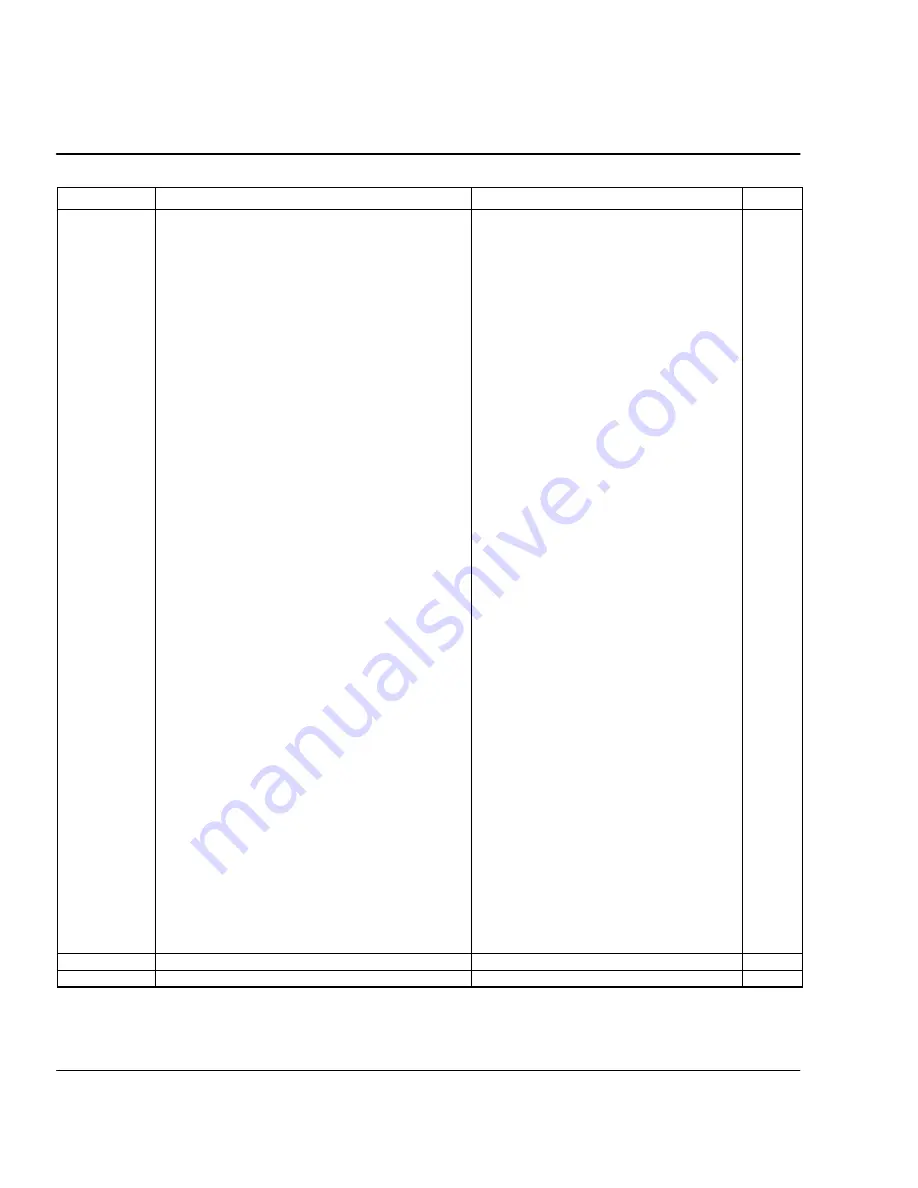
9-14 Accessories & Options
MN1276
Continued
Index (hex)
Object
Used
PDO mappable parameters (2080 -- 2093):
MANUFACT_POS
MANUFACT_ABS_POS
MANUFACT_VEL
MANUFACT_VEL_COMMAND
MANUFACT_CONTROL_COMMAND
MANUFACT_TORQUE_COMMAND
MANUFACT_POS_COMMAND
Read only:
MANUFACT_COM_ACTU
MANUFACT_COM_ACTV
MANUFACT_COM_ANAIN
MANUFACT_COM_CUR
MANUFACT_COM_FLT
MANUFACT_COM_FEST
MANUFACT_COM_LOG
MANUFACT_COM_MODE
MANUFACT_COM_MPFE
MANUFACT_COM_MVFE
MANUFACT_COM_PFE
MANUFACT_COM_VFE
MANUFACT_COM_POS
MANUFACT_COM_PREF
MANUFACT_COM_RFOFS
MANUFACT_COM_VEL
MANUFACT_COM_VREF
MANUFACT_COM_WRN
MANUFACT_COM_ABSPOS
Write only:
MANUFACT_COM_CLEAR
2180 MANUFACT_COM_DIS
MANUFACT_COM_ENA
MANUFACT_COM_DISA
MANUFACT_COM_FRST
MANUFACT_COM_GRST
MANUFACT_COM_HOLD
MANUFACT_COM_IADJ
MANUFACT_COM_ICLC
MANUFACT_COM_JS
MANUFACT_COM_LOGRST
MANUFACT_COM_PRST
MANUFACT_COM_ABS
MANUFACT_COM_HOME
MANUFACT_COM_INC
MANUFACT_COM_CALC
MANUFACT_COM_QUIT
MANUFACT_COM_CONT
MANUFACT_COM_STOP
MANUFACT_COM_PLOAD
MANUFACT_COM_PSAVE
2080
2082
2081
2090
2091
2092
2093
2100
2101
2102
2103
2104
2105
2106
2107
2108
2109
210A
210B
210C
210D
210E
210F
2110
2111
2112
2180
2181
2182
2183
2184
2185
2186
2187
2188
2189
218A
218B
218C
218D
218E
2190
2191
2192
2193
2194
2195
6000 -- 9FFF
Standardized Device Profile Area
A000-- FFFF
Reserved