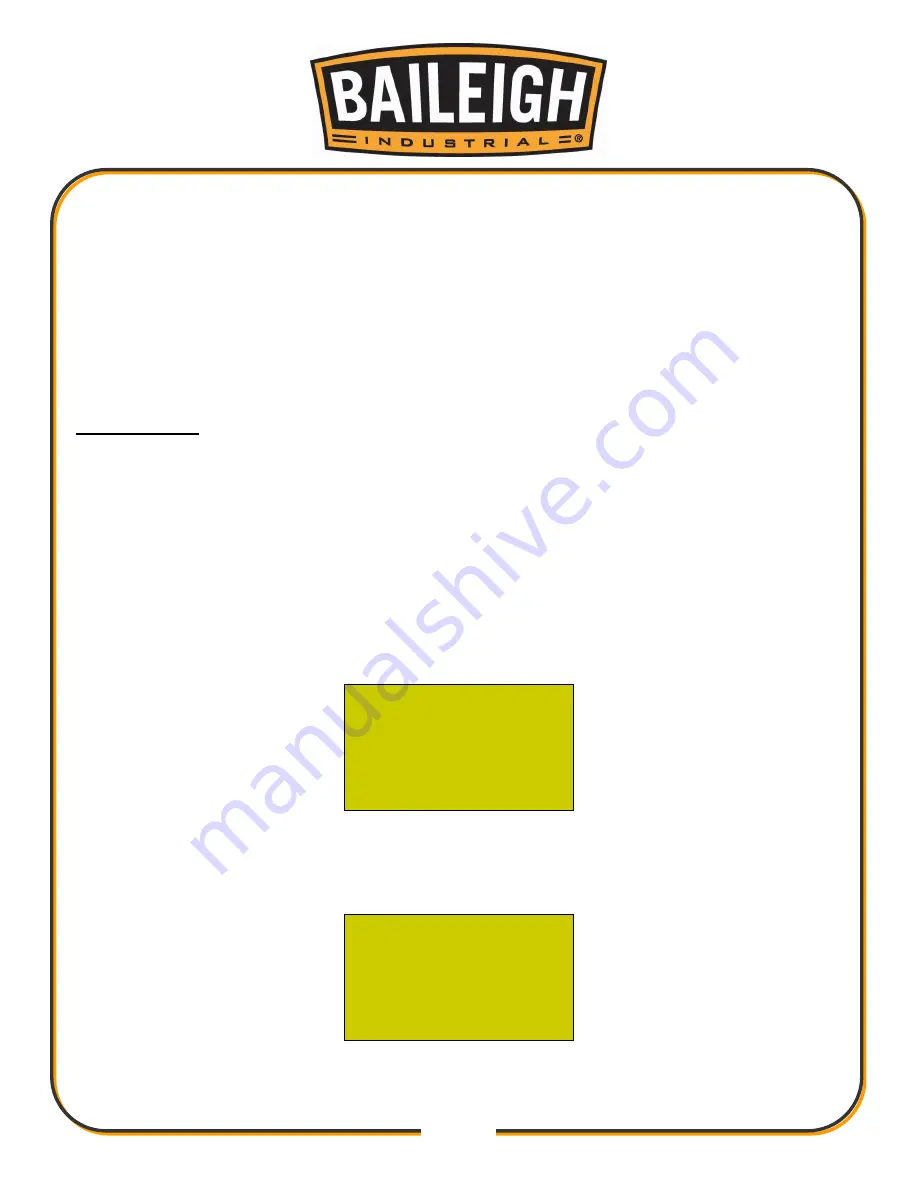
35
35
14. The bit will touch the sensor, (typically twice and may appear as a quick bounce), and then
lift approximately 1mm above the touch pad.
15. When completed, tool number 3 has been measured and that Z coordinate will have been
recorded within the systems memory.
16. Repeat these steps as needed for any other tool holder and bit assemblies.
17. Once completed, this will need to be repeated when the bit in the holder is changed in any
way, either by sharpening, or replacing or similar change.
MENU TREE
The normal operation screen will display is a combination of rows and columns.
X, Y, and Z are each in a row with their coordinate locations relative to the last set workpiece
coordinate. The right or 3
rd
column is a display of the active operating conditions and settings.
When the machine is not moving it will display “Idle”. When it is being moved or running a
program, it will displa
y “Run”.
The next row down will display the Spindle status. SOff = Spindle Off. When the spindle is
running, this will display from 0S to S7 depending upon the operator’s settings. These steps or
gears are the relative rpm that the spindle will be turning at.
Pressing the “Shift” key will change between “Jog” or “Stepping”. This will change the movement
of the axises from continues as long as the axis key is pressed to moving a specific distance
each time the axis key is pressed.
1X
0.000
Idle
1Y
0.000
SOff
1Z
11.000
Slow
Jog
T1
100%
Pressing the OK key will change to the parameters screen for the operation being performed.
Using the up or down arrow keys will move the cursor around the screen to allow for values to
be edited as needed. Press ESC to return to the Operating screen. Pressing the
MSpd
8000/
3000
StepXY
0.100
StepZ
0.100
File
T1.NC
Summary of Contents for WR-84V-ATC
Page 48: ...46 46...
Page 51: ...49 49 ELECTRICAL SCHEMATIC...
Page 52: ...50 50...
Page 53: ...51 51...