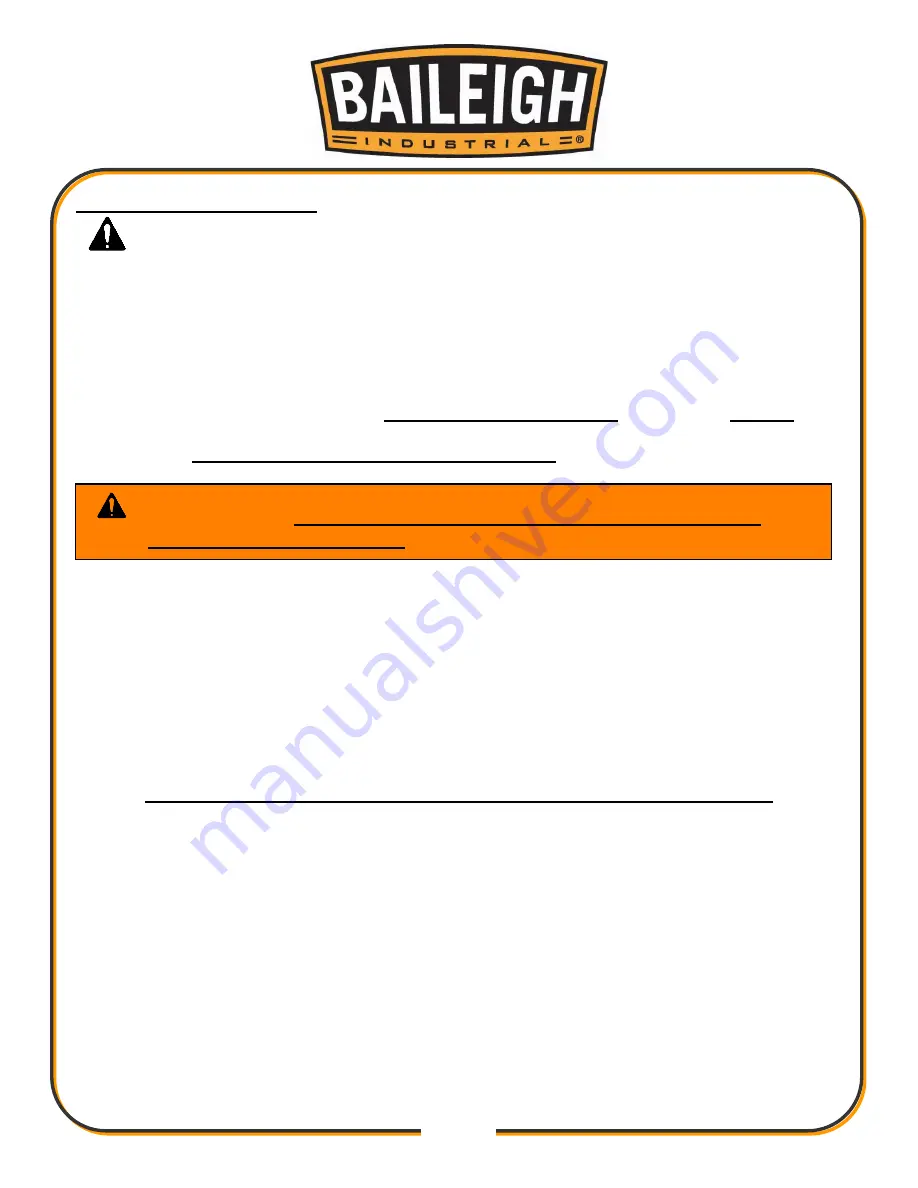
7
7
SAFETY PRECAUTIONS
Metal working can be dangerous if safe and proper operating procedures are not followed. As
with all machinery, there are certain hazards involved with the operation of the product. Using
the machine with respect and caution will considerably lessen the possibility of personal injury.
However, if normal safety precautions are overlooked or ignored, personal injury to the operator
may result.
Safety equipment such as guards, hold-downs, safety glasses, dust masks and hearing
protection can reduce your potential for injury. But even the best guard will not make up for poor
judgment, carelessness or inattention.
Always use common sense
and exercise
caution
in
the workshop. If a procedure feels dangerous, don’t try it.
REMEMBER:
Your personal safety is your responsibility
.
Dear Valued Customer:
• All Baileigh machines should be used only for their intended use.
• Baileigh does not recommend or endorse making any modifications or alterations to a
Baileigh machine. Modifications or alterations to a machine may pose a substantial risk of
injury to the operator or others and may do substantial damage to the machine.
• Any modifications or alterations to a Baileigh machine will invalidate the machine’s warranty.
P
LEASE ENJOY YOUR
B
AILEIGH MACHINE
!
....P
LEASE ENJOY IT
SAFELY!
1.
FOR YOUR OWN SAFETY, READ INSTRUCTION MANUAL BEFORE OPERATING THE
MACHINE.
Learn th
e machine’s application and limitations as well as the specific hazards.
2.
Only trained and qualified personnel can operate this machine.
3.
Make sure guards are in place and in proper working order before operating
machinery.
4.
Remove any adjusting tools.
Before operating the machine, make sure any adjusting tools
have been removed.
5.
Keep work area clean.
Cluttered areas invite injuries.
6.
Overloading machine.
By overloading the machine, you may cause injury from flying parts.
DO NOT
exceed the specified machine capacities.
7.
Dressing material edges.
Always chamfer and deburr all sharp edges.
WARNING:
FAILURE TO FOLLOW THESE RULES MAY RESULT IN
SERIOUS PERSONAL INJURY
Summary of Contents for DP-1250VS
Page 19: ...16 16 GETTING TO KNOW YOUR MACHINE H P J B C A G H I L M E F D N O K Q R ...
Page 36: ...33 33 HEAD MOTOR AND ELECTRICAL PARTS DIAGRAM ...
Page 37: ...34 34 ...
Page 42: ...39 39 HEAD AND SPINDLE PARTS DIAGRAM ...
Page 45: ...42 42 COLUMN TABLE AND BASE PARTS DIAGRAM ...
Page 48: ...45 45 CHUCK GUARD PART DIAGRAM ...