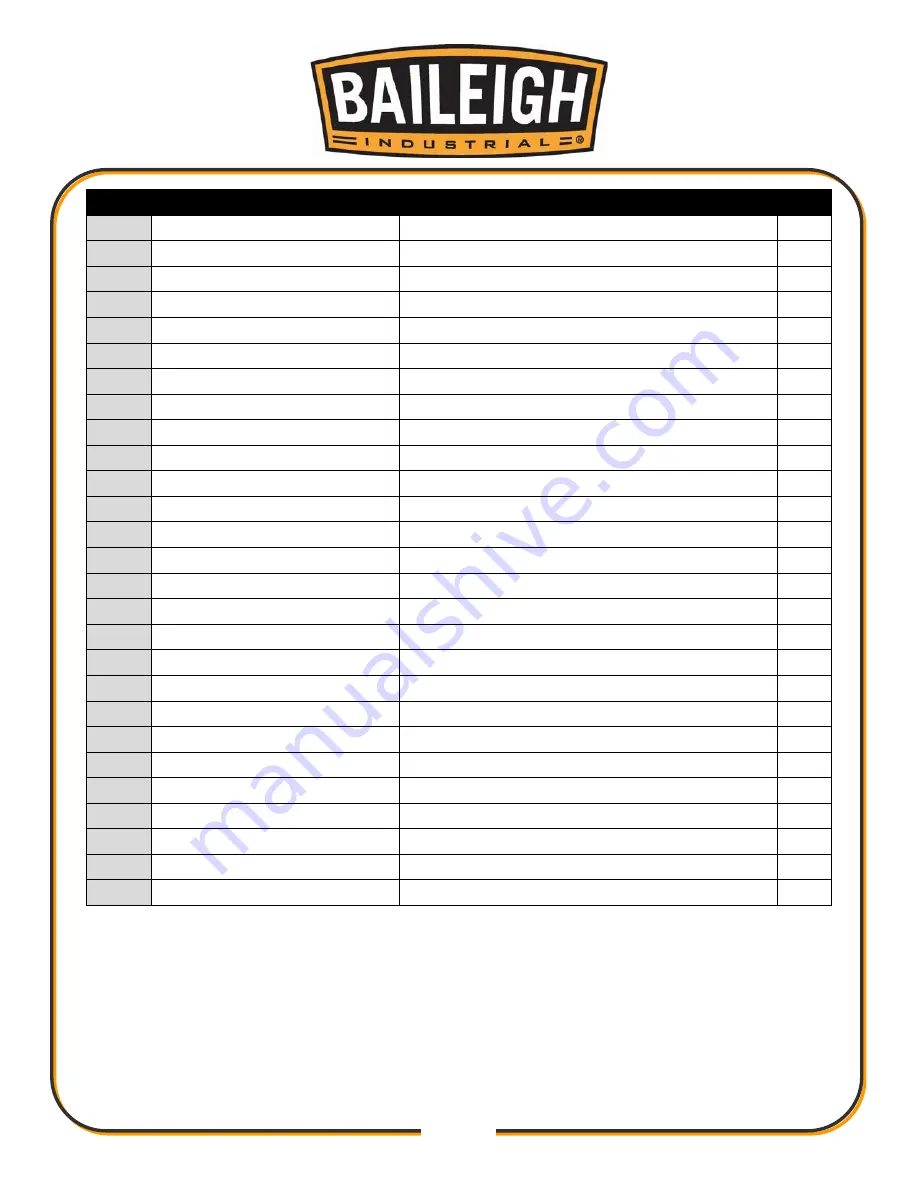
23
23
Item
Part No.
Description
Qty.
34
M6 x 1.0 x 20
Set Screw
1
35
M10 x 1.5 x 35
SHCS
2
36
M10 x 1.5
Flange Nut
2
37
M12 x 1.75 x 35
SHCS
3
38
PP-1492
Tooling Pin
1
39
M5 x 0.8 x 40
SHCS
4
40
M16 x 2.0 x 35
Hex Flange
8
41
M6 x 1.0 x 30
SHCS
4
42
M6 x 1.0
Flanged Nut
4
43
M8 x 1.25 x 70
SHCS
4
44
.25 x 1.0
Slotted Spring Pin
1
45
PP-0837
1.25 I.D. x 1.50 O.D. x 1.50 Long
1
46
M10 x 1.5 x 20
SHCS
4
47
STD.
.1875 x 1 Keystock
2
48
3/4" Ext. Retaining Ring
Std.
6
49
1/2-13 x 1.0
SHCS
2
50
PP-0322
0.75 Id x 1.25 Od x .125 THK
4
51
PP-0101
0.75 Id x 1.25 Od x .0625 THK
10
52
AH-7A015
Spacer
2
53
STD.
M16 x 2.0 x 30 Set Screw
1
54
M6 x 1.0 x 20
SHCS
2
55
M8 x 1.25 x 25
SHCS
2
56
M6 x 1.0 x 25
SHCS
2
57
PP-1333
1/4 NPT – 3/8 Push Lock Elbow
4
58
AH28-7A016-V2
Guide Hub
1
61
AH28-6A007
Shipping Bracket
4
62
M12 x 1.75
Flange Nut
4
Summary of Contents for PH-28A
Page 18: ...16 16 PARTS DIAGRAM ...
Page 19: ...17 17 FRAME ...
Page 20: ...18 18 PNEUMATICS ...
Page 21: ...19 19 ANVIL RAM ...
Page 22: ...20 20 QUICK RELEASE ...
Page 23: ...21 21 HAMMER HEAD PRE 2018 ...
Page 27: ...25 25 NOTES ...