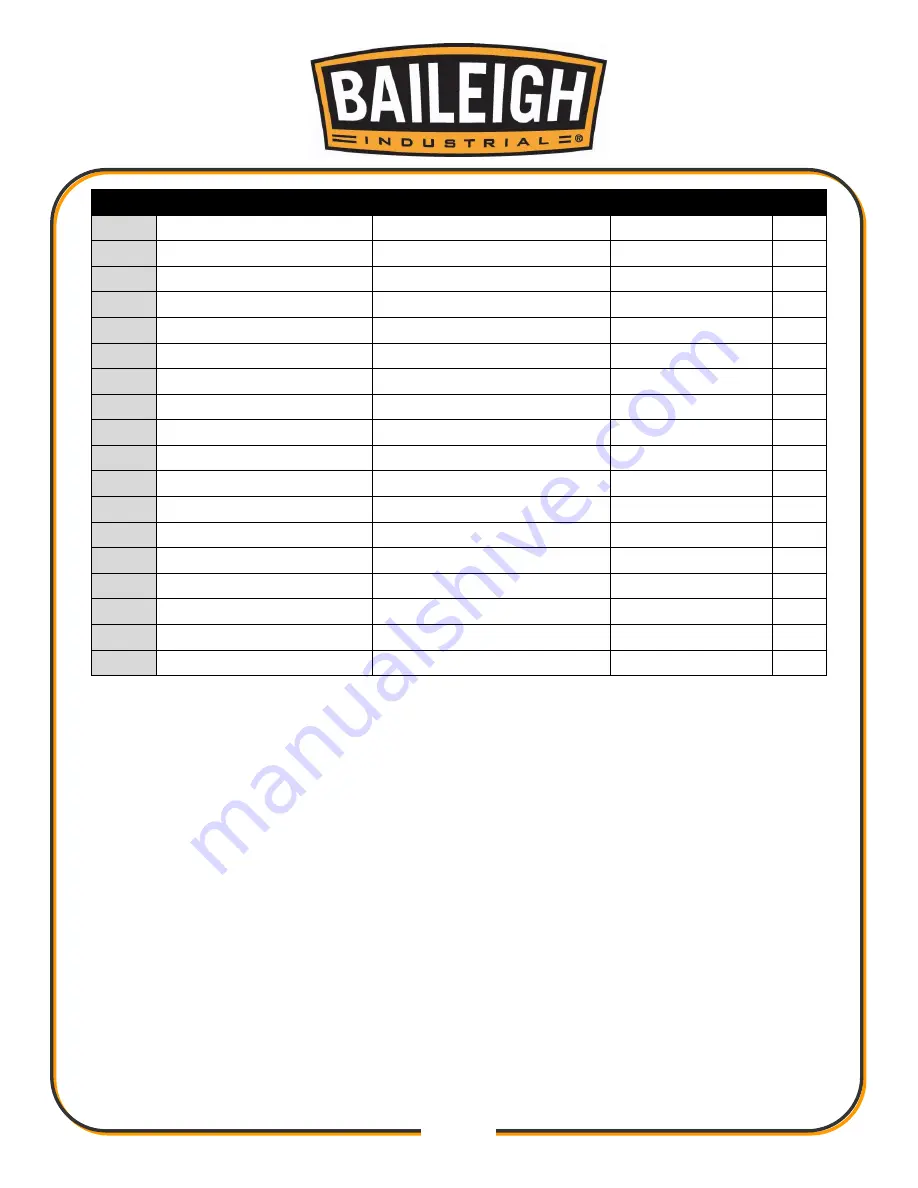
34
34
Item
Part No.
Description
Size
Qty.
94A
DP2012FHDV3-094A
Phillip Head Screw
1
95
DP2012FHDV3-095
Light Socket
1
96
DP2012FHDV3-096
Light
1
97
DP2012FHDV3-097
Hex Wrench
3mm
1
98
DP2012FHDV3-098
Hex Wrench
4mm
1
99
DP2012FHDV3-099
Drift key
1
100
DP2012FHDV3-100
Power Cord
1
100B
DP2012FHDV3-100B
Wire Gasket
1
100C
DP2012FHDV3-100C
Motor Cord
1
104
DP2012FHDV3-104
Motor Fan Cover
1
105
DP2012FHDV3-105
Speed Chart
1
110
DP2012FHDV3-110
Strain Relief
1
111
DP2012FHDV3-111
Insert Retaining Ring
1
112
DP2012FHDV3-112
Degree Scale
1
113
DP2012FHDV3-113
Indicator
1
114
DP2012FHDV3-114
Set Screw
M8x25
1
115
DP2012FHDV3-115
Hex Nut
M8
1
116
DP2012FHDV3-116
Lock Washer
20
1
Summary of Contents for DP-2012F-HD-V3
Page 17: ...15 15...
Page 24: ...22 22 ELECTRICAL SCHEMATIC...
Page 31: ...29 29 STAND TABLE PARTS DIAGRAM...
Page 32: ...30 30 HEADSTOCK PARTS DIAGRAM...
Page 38: ...36 36 NOTES...
Page 39: ...37 37 NOTES...