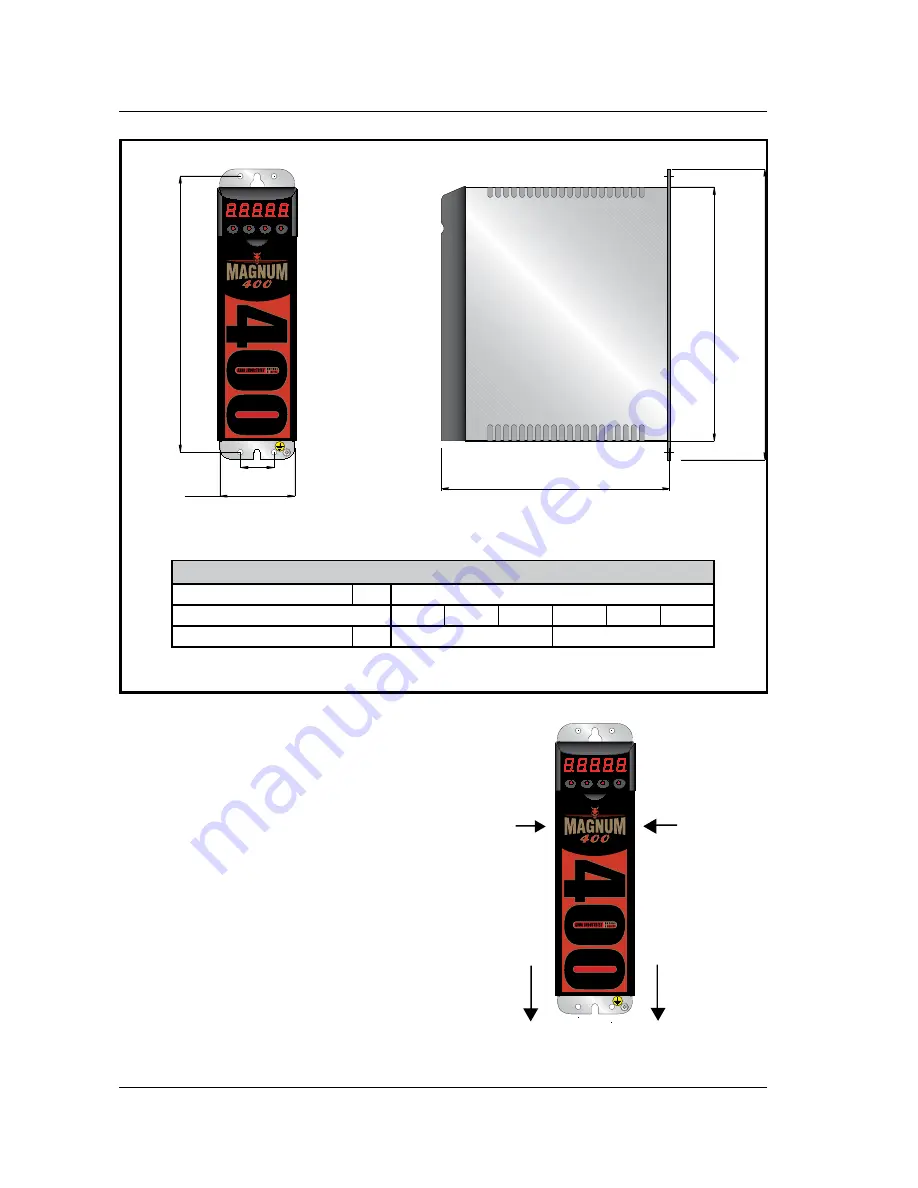
12
AXOR Industries
Service Manual
Magnum400
TM
ver.2 rel.05/'15
1.4 Mechanical Dimension
Dimension in: [mm]
UP
MODE
DWN
SET
A
A
B
B
73,5
270
247
284
223
33
UP
MODE
DWN
SET
noTe
:
The
m1
and
m2
connectors are located
under the plastic cover.
To open it, push the cover on the
borders (see A), move it down and
remove it (see B).
Mechanical specifications
external dimensions
mm
284 x 223 x 73,5
Size
1,5/3
3,5/7
7/14
10/20 14/28 20/40
weight
Kg
4,2
4,6