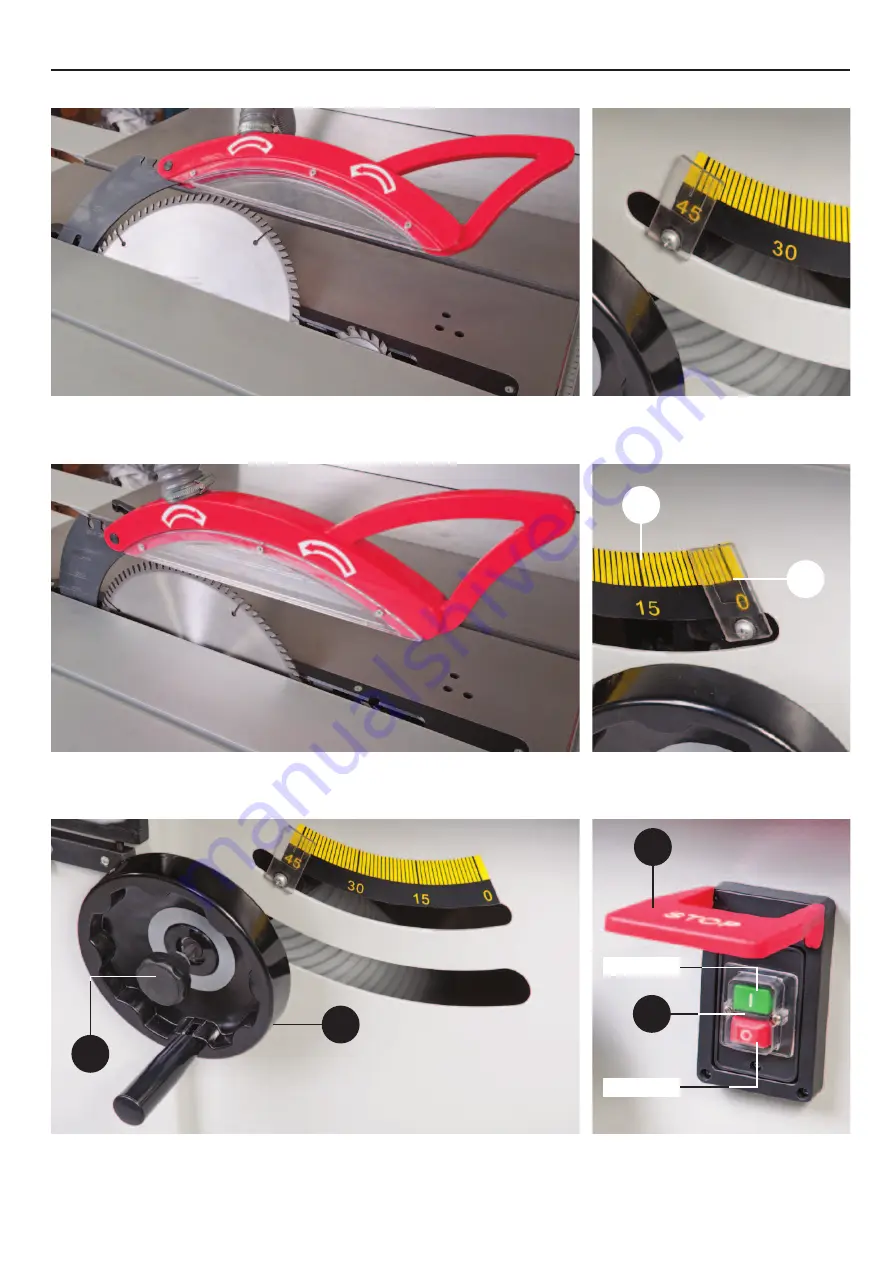
Illustration and Parts Description
27
Saw assembly tilted to 45˚ degrees
Saw scale set to 45˚ degrees
Saw assembly set at 90˚ degrees
• Saw tilt scale (A)
• Scale pointer (B)
Rise and fall operating wheel, (A) and clamping knob, (B)
NVR ON/OFF switch assembly, (A)
Emergency stop shroud, (B)
press down to stop the machine
A
B
B
A
A
B
OFF Button
ON Button
Summary of Contents for MJ12-1600 MKII
Page 1: ...Code 505150 AT M 06 02 2015 REF 508469 MJ12 1600MKII Panel Saw ...
Page 4: ...What s Included 4 1 3 4 2 5 6 8 7 Box 1 ...
Page 5: ...What s Included 5 9 10 11 12 13 Box 1 14 15 16 17 ...
Page 6: ...What s Included 6 Box 1 Box 2 A B C D E F G H I J 18 19 20 21 22 23 24 ...
Page 21: ...Machine Footprint 21 2 900mm 1 440mm 1 620m m 1 Metre extension ...
Page 42: ...Wiring Diagram 42 Single Phase ...
Page 44: ...Exploded Diagram Parts List 44 Diagram List B ...
Page 46: ...Exploded Diagram Parts List 46 Diagram List C ...
Page 47: ...Exploded Diagram Parts List 47 Diagram List C2 Continues Over ...
Page 50: ...Exploded Diagram Parts List 50 Diagram List E ...
Page 52: ...Exploded Diagram Parts List 52 Diagram List G ...
Page 55: ...Notes 55 ...