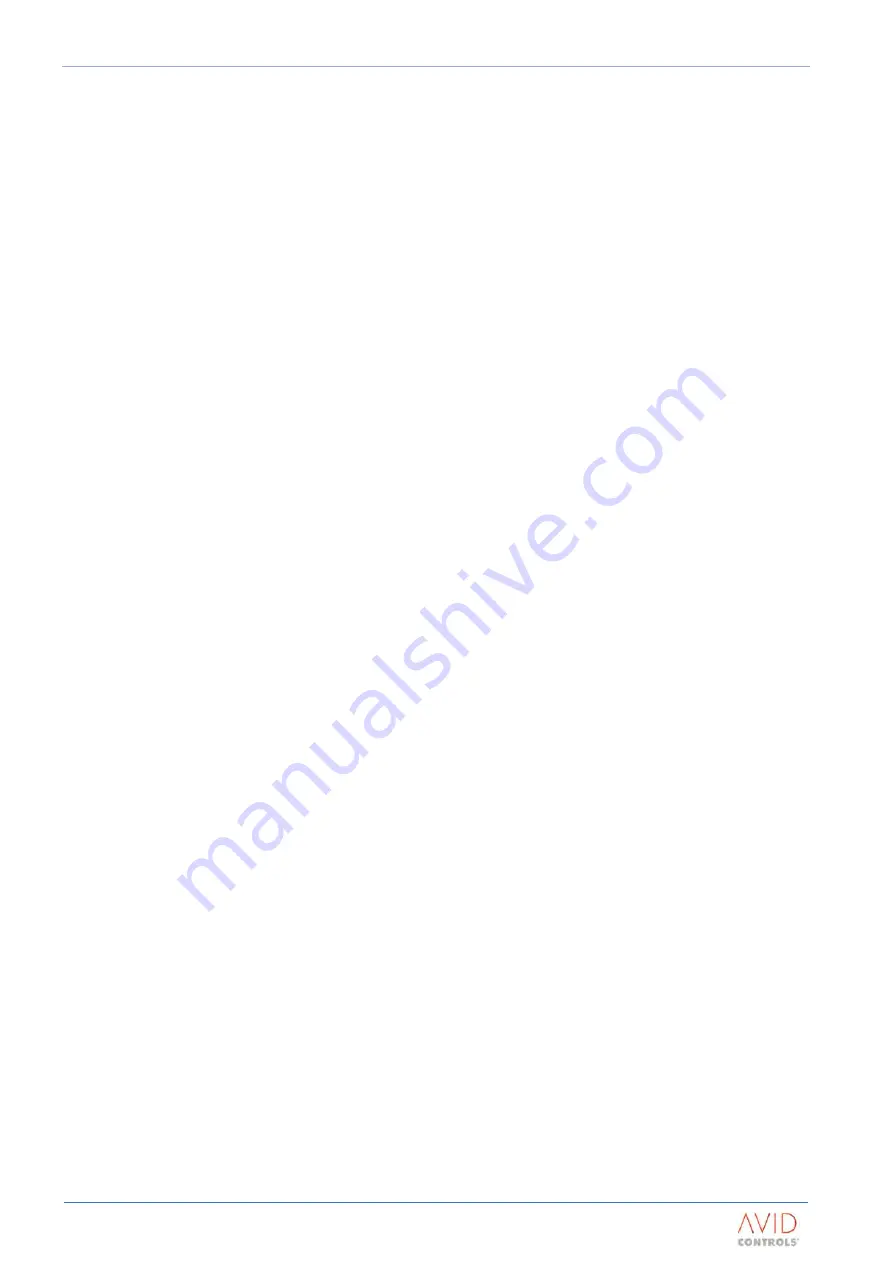
Drive (CDM) Design
T1689 Technical Manual Rev 07
Mechanical Design principles
MV3000 Air Cooled DELTA
Page 82
3.5.3
Electrical Bonding
In additional to electrical safety bonding, functional bonding of the enclosure/s and the components located in
these is mandatory to ensure that the CDM performs correctly.
This bonding is especially important between the control components and the DELTA power modules.
•
A continuous bond of earthed metal is required from all the DELTA transistor modules to the controller:
•
This is usually achieved by a wide steel plate that provides a low inductance path between
modules and to the controller. The high frequency currents creating a small voltage difference
across this bond.
•
Also bond the DELTA power modules together using the bonding plate supplied with the DELTA
modules to form a single metal highway across the front of the DELTAs. This arrangement forms
a ground plane (low resistive and low inductive path) against which the control ribbon cables
must be run (see Section 5.14: Fitting Earth Bonding Plates).
•
It is unnecessary to extend this bonding highway to the rectifier modules.
•
Additional low inductance paths are beneficial.
•
The DELTA mounting frames when directly fastened (metal-to-metal) to the unpainted enclosure
frame also aid this bonding.
•
Screened control cables also provide a low inductance path, but without adequate parallel metal-
to-metal component bonding, the signals carried will be disrupted by noise currents.
•
The installer of the modules must complete the bonding path (and cable routing) to the
controller. These parts are not supplied with the modules as the exact position of the controller
is not fixed.
•
The control enclosure must also be bonded to the power modules enclosure:
•
Use high frequency techniques.
•
Use multiple paths.
•
Bond all of the enclosures together.
•
Converters contain high leakage current equipment so currents will flow between adjacent
enclosures.
•
To minimise the voltage created by these currents, a low impedance, low inductance path
(some of these currents are at high frequency) must be provided. This is usually in
addition to any safety bonding.
•
This bonding must be by direct metal-to-metal contact, not by braids or cables to make a
‘continuous enclosure’.
•
Bond all of the enclosure’s panels together.
•
This bonding must be by direct metal-to-metal contact, not by braids or cables to make a
‘continuous enclosure’.
•
Bond all the cable gland plates to the enclosure.
•
To continue the screening effectiveness of screened or armoured cables, you must bond to the
ground plate by a 360° degree connection.
•
The gland plate must then be connected directly to the enclosure walls, or to metal framework to
which the outer walls are electrically bonded.
•
Gland plates must not be spaced off, even on metal pillars or bars.
•
Direct metal-to-metal contact across a large surface area must be achieved for low
inductance continuity.
•
This bonding is required in addition to any electrical safety bonding.
•
Both control and power cabling gland plates must be directly bonded.