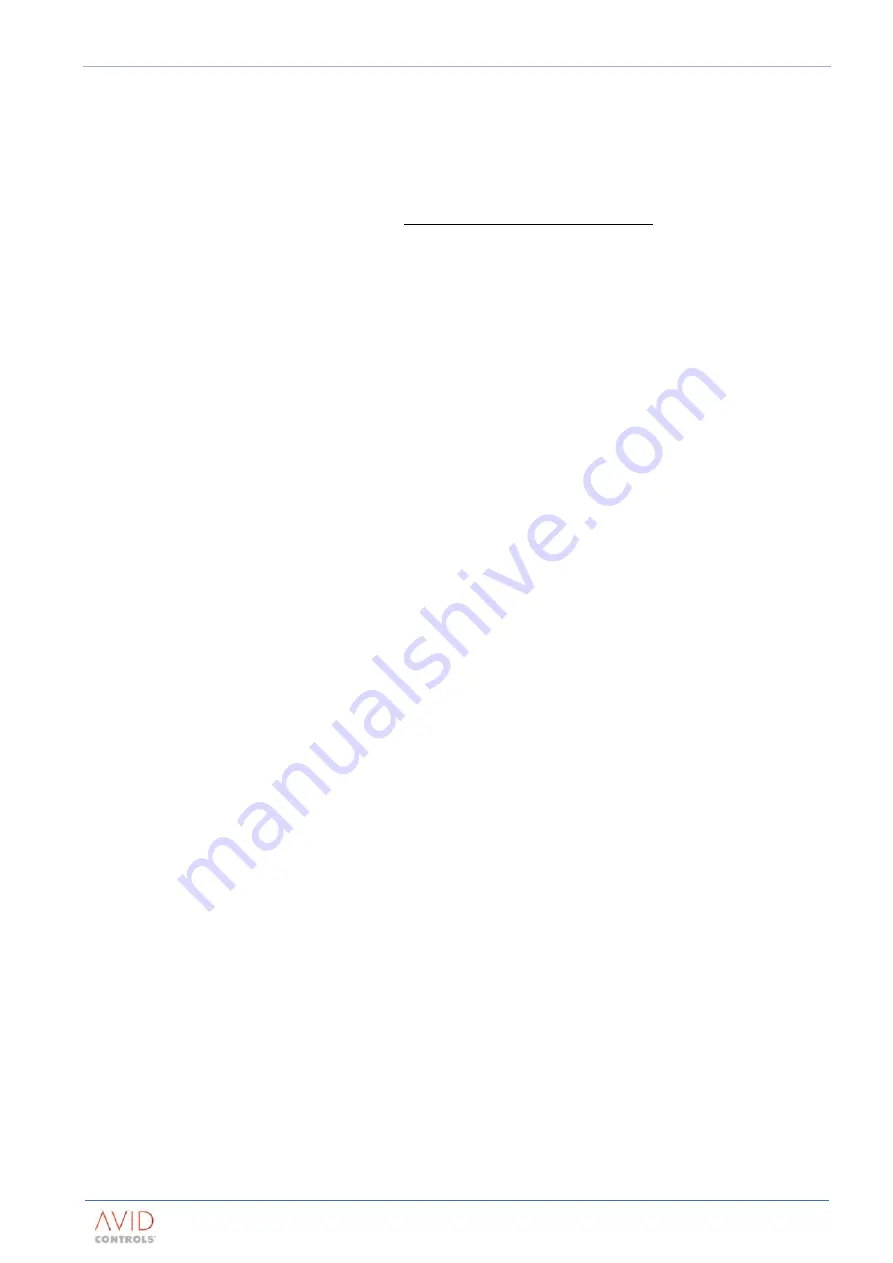
T1689 Technical Manual Rev 07
PDS Design
MV3000 Air Cooled DELTA
Mains Supply Cables
Page 105
Due to imperfections in encoder manufacture, the edges are not equally spaced. Some encoder manufacturers
quote the minimum edge separation in electrical degrees. This is 90° for a perfect encoder but can be as low as
40°.
For a given required top speed and encoder minimum edge separation, the line count must not exceed:
Speed
Top
Required
Separation
Edge
Min
Count
Line
Max
_
_
)
_
_
(
10
500
_
_
3
×
×
=
Where :
Min_Edge_Separation is in electrical degrees
Required_Top_Speed is in rev/min.
If the encoder manufacturer quotes a “scribing error” in electrical degrees, then
Min_Edge_Separation = 90 - Scribing_Error.
If the encoder manufacturer quotes a symmetry of 180
±
x and a quadrature phase shift of 90
±
y, then
Min_Edge_Separation = 90 - x - y.
4.3.3
Encoder Mounting
For vector control mode, the mechanical coupling between motor and encoder is critical and any eccentricity in
the mechanical coupling will impair performance. The best solution is a motor built with an integral shaft
encoder, otherwise accurate alignment of encoder with motor shaft is very important.
An encoder may be used to perform position control. For position control in frequency control or encoderless
vector control modes, an encoder or linear scale may be mounted on the controlled plant.
To prevent electrical noise being coupled from the motor into the electrical signals from the encoder:
•
The encoder shaft must be electrically insulated from the motor shaft and motor frame;
•
The encoder body must be electrically insulated from the motor frame.
4.3.4
Encoder Cable Screening
The encoder wires, including the encoder power supply wires, must be contained in a screened cable and the
screen must be connected to the M4 screw adjacent connector TB5 on the User I/O Termination Panel. The
screen must be continuous throughout its length. In addition to the connection to the M4 screw on the User
I/O Termination Panel, the screen should be connected by a 360° bond to the drive enclosure and to the
encoder body.
4.4
MAINS SUPPLY CABLES
Where the mains supply cable to the drive is a screened or armoured cable, the screen must be bonded to the
drive enclosure. The screen or armour should also be bonded to safety earth at the source of the supply.
Where the drive is fed from an isolating transformer, the supply cable to the drive must be screened or
armoured or placed in a metallic trunking. The screen or armour or metallic trunking must be bonded to the
drive enclosure and to safety earth at the supply transformer. This bonding is most effective when it is done
via 360
°
cable glands.