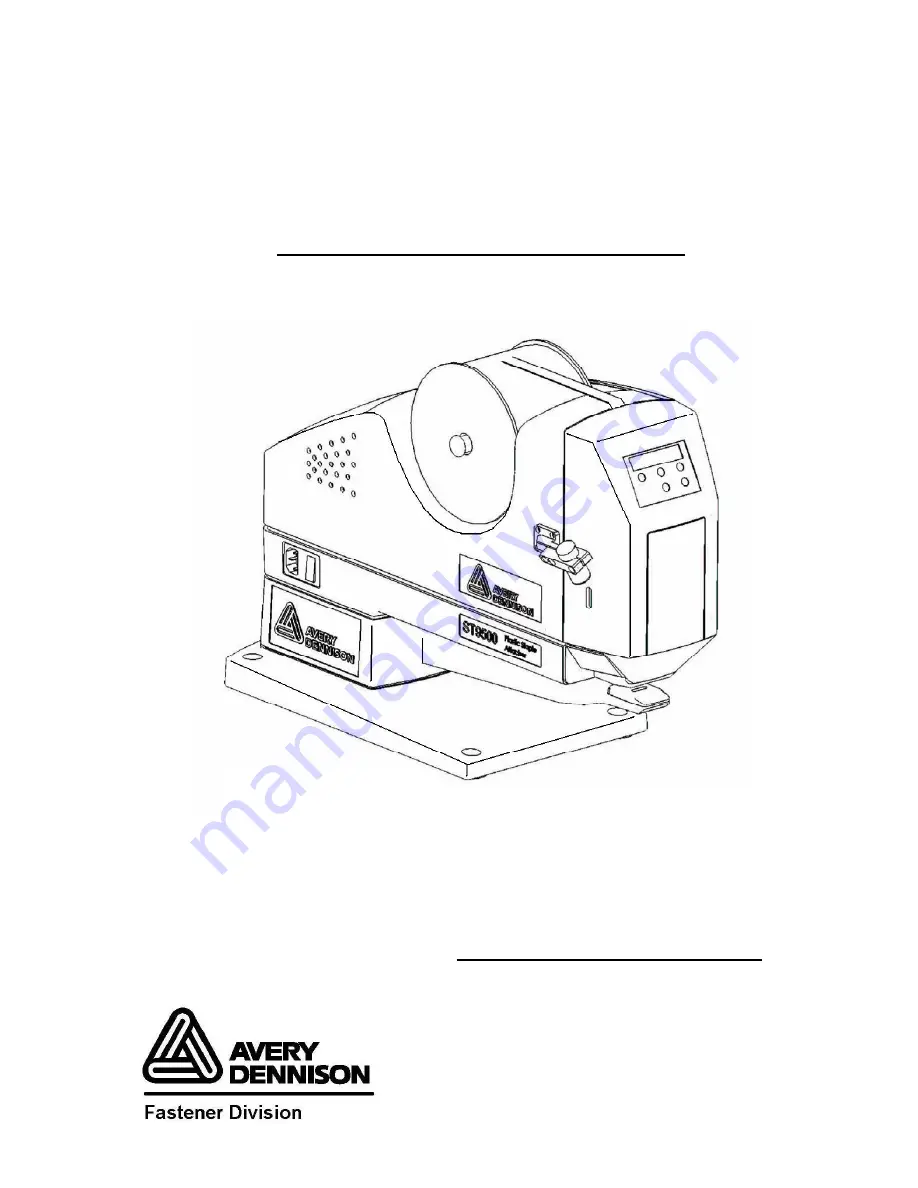
1
ST9
ST9
ST9
ST95
5
5
500™
00™
00™
00™
Plastic Staple
Plastic Staple
Plastic Staple
Plastic Staple
®
®
®
®
Attacher
Attacher
Attacher
Attacher
Item # 15000™
Operator and
Operator and
Operator and
Operator and
Service Manual
Service Manual
Service Manual
Service Manual
©
©
©
©
Part No. 3-05-0100-01 Rev. 1
Patent(s) Pending
Summary of Contents for ST9500
Page 17: ...17 5 Panel Operation Flow Chart...
Page 58: ...58 Whole Machine Exploded Illustration...
Page 60: ...60 Base Assembly and Body Assembly Exploded Illustration...
Page 62: ...62 Motor Assembly Exploded Illustration...
Page 65: ...65 Head Subassembly and Knife Lever Assembly Exploded Illustration...
Page 67: ...67 Base Knife Assembly Exploded Illustration...
Page 69: ...69 Left and Right Needle Holder Assembly Exploded Illustration...
Page 71: ...71 Guide Bar Assy Feed Assy and Feed Lever Assy Exploded Illustration...
Page 74: ...74 Switch Power Supply Assy and Driver Assy Exploded Illustration...