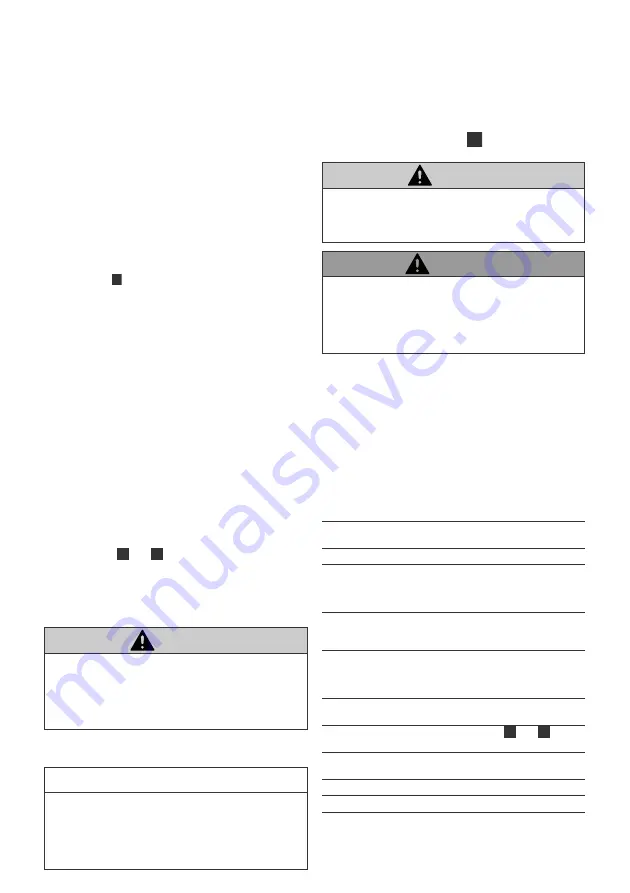
5
AVENTICS
| HF04/LP04 | R412009744–BDL–001–AB
Tools required: Screwdriver
PZ0, Ø max. 3 mm
,
e.g. bit 855/00 size 0x50 mm, code 055805 from WERA
Any mounting orientation may be used.
The pressure regulator can only be mounted on the
subbase
with
bore holes from version 05.08.
Older subbases have no bore holes. If necessary, please
contact your sales service.
O
Use only subbases with bore holes (
6
).
1.
Check that the pressure regulator matches your order
using the material number printed on the housing.
2.
Remove two valves in adjacent valve positions by
loosening the screws (
7
) and pulling them upwards off
the subbase (
5
).
3.
Mount the pressure regulator as follows:
–
HF04: On a double subbase or half-and-half on two
double subbases
–
LP04: On two single subbases
4.
Check the correct seating of the molded seals.
5.
Tighten the mounting screws (
4
) crosswise
(see figure
). Tightening torque: 0.2–0.3 Nm,
max. speed: 500 rpm
6.
Mount the valve to be controlled at valve position 1 (
1
) of
the pressure regulator.
6
Commissioning
O
Let the pressure regulator acclimatize for several hours
before commissioning, otherwise water may condense
in the housing.
Setting the pressure regulator
1.
Pull the blanking plug (
9
) out of push-in fitting (
8
) and
connect the preassembled pressure gauge with
compressed air hose
4 to the push-in fitting.
2.
Slowly pressurize the system to the stipulated working
pressure.
3.
Pull the safety cap (
12
) off the pressure regulator.
4.
Loosen the lock nut (
10
) while counter-holding the
adjustment screw (
11
).
5.
Set the secondary pressure at the adjustment screw.
6.
Tighten the lock nut (
10
) while counter-holding the
adjustment screw (
11
).
7.
Fit the safety cap (
12
) again.
The pressure is now set for operation.
In the diagrams
and
the nominal flow rate Q
n
is
plotted over the pressure p at the measuring tube.
7
Operation
Pressure regulators are not gas-tight. Leakages of
10 ml/min can occur even when new.
8
Service and maintenance
O
Clean the pressure regulator at regular intervals only
using a slightly moist cloth. Only use water to do this
and, if necessary, a mild detergent.
The pressure regulator is maintenance-free.
9
Disassembly
1.
Remove the valve by loosening the screws (
7
) and
pulling it upwards off the pressure regulator.
2.
Remove the pressure regulator by loosening the screws
(
4
) and pulling it upwards off the subbase.
10 Accessories
W
Pressure gauge R412009413
Further accessories approved for your configuration can be
found in the online catalog from AVENTICS at
www.aventics.com/pneumatics-catalog.
11 Technical data
CAUTION
Malfunction with unstable supply pressure!
The function of the pressure regulator is no longer
assured if the supply pressure drops below the pressure
to be regulated.
O
Ensure that the supply pressure does not drop below
the regulated pressure.
NOTICE
Damage to the surface caused by solvents and
aggressive detergents!
The seals on the pressure regulator may age faster
under aggressive ambient conditions.
O
Never use solvents or aggressive detergents.
O
Do not use high-pressure cleaners for cleaning.
1
2
3
CAUTION
Danger of burns caused by hot surfaces!
Touching the device during operating may cause burns.
O
Let the device cool off before disassembling it.
O
Do not touch the device during operation.
WARNING
Danger of injury if disassembled under pressure!
Injuries and damage to the device or system components
may occur if the pressure is not switched off before
beginning disassembly.
O
Make sure that the relevant system part is not under
pressure before you disassemble the product.
Dimensions
(width x height x depth)
23.4 mm x 59.6 mm x 198.5 mm
Weight
102 g
Temperature range
Application:
–5
C to 50
C
Storage
–20
C to 70
C
Permissible medium
Max. particle size Oil
content in compressed air
Compressed air
5 μm
0 mg/m
3
–5 mg/m
3
W
The pressure dew point must be at least 15
C below
the ambient and medium temperature and must not
exceed max. 3
C. The oil content of the compressed air
must remain constant over the whole service life.
Pressure regulation range 0.5–8 bar (R412000999)
0.5–4 bar (R412005884)
Flow rate acc. to
ISO 6953-2
See diagram
and
Protection class acc. to
IEC 60529
IP 65
Fuse
1 A
Mounting position
Any
1
2
3