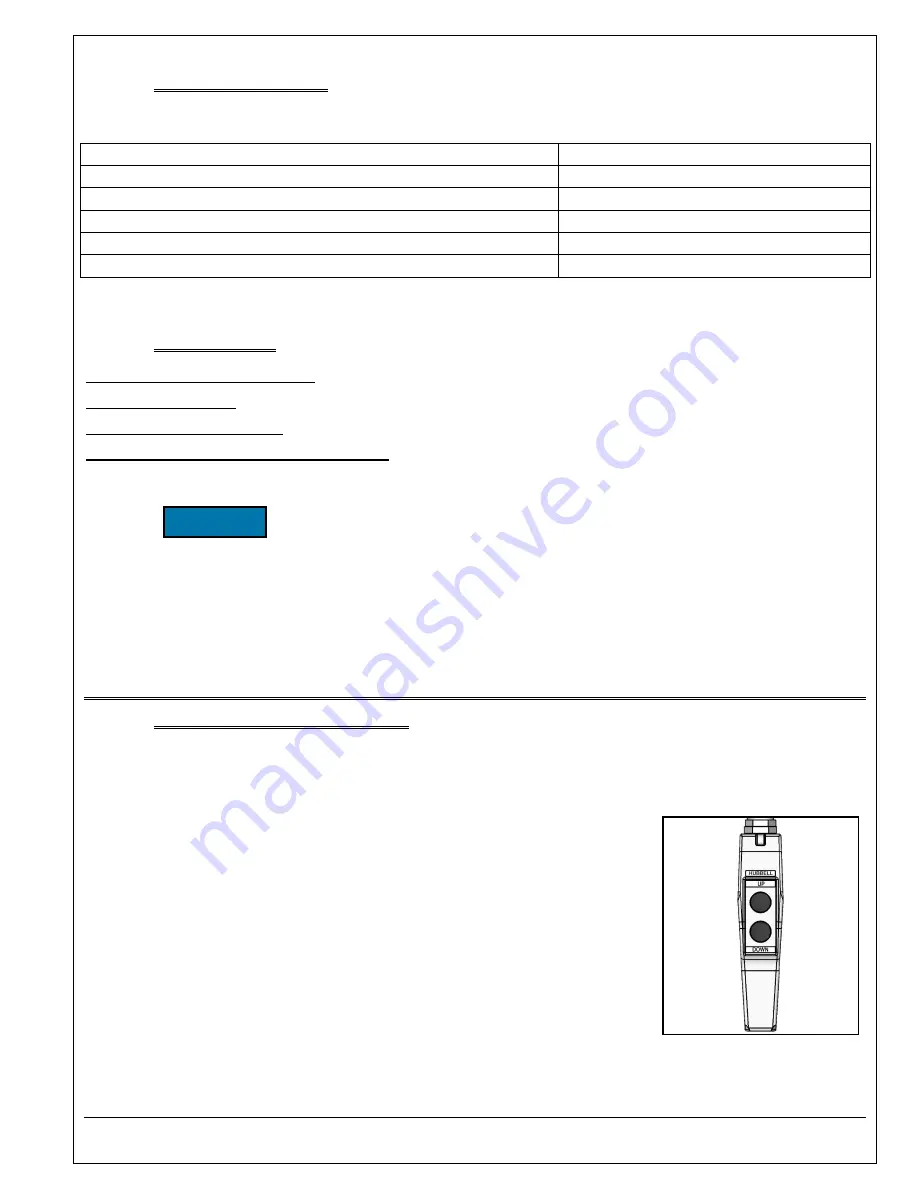
33
6.2.4
Oil Requirements
Follow recommendations below that apply to your application.
Environment (Ambient Temperature)
Recommended Oil
Indoor locations with variable temperatures: 30 - 100 degrees F. 5W 30 or 5W 40 Multiviscosity Motor Oil
Indoor locations with constant temperatures: 60 - 80 degrees F. SAE 20 Motor Oil
Outdoor locations: 30 - 120 degrees F.
5W 30 or 5W 40 Multiviscosity Motor Oil
Outdoor locations: 10 degrees F below 0 to 100 degrees F.
5W 20 or 5W 30 Multiviscosity Motor Oil
Cold Storage Warehouse: 10 - 40 degrees F.
Contact local
Autoquip
Service Rep.
Note: All oils are detergent type.
6.2.5
Oil Capacity
*Contractor Polyethylene Tank: Oil capacity is approximately: (5.5) gallons or (22) quarts.
*Vertical Steel Tank: Oil capacity is approximately: (10) gallons or (40) quarts.
*Large Vertical Steel Tank: Oil capacity is approximately: (12) gallons or (48) quarts.
Steel Tube Tank for Internal Power Units: Oil capacity is approximately (2) gallons or (8) quarts.
* Oil level should be 1" to 1-1/2" below the top of the reservoir.
Use approved fluids only. Use of unauthorized fluids may
cause damage to seals and hosing.
Do Not Use:
Automatic Transmission Fluid (ATF)
Hydraulic Jack Oil
Brake Fluids
6.3
General Maintenance
6.3.1
Hydraulic Cylinder Repair
6.3.1.1.
Cylinder Removal
1. Raise lift to its full height and engage maintenance device.
See “Maintenance Device” section.
2. Disconnect electrical power to lift. Follow lock out-tag out procedure.
3. Disconnect cylinder hose at the tee connection on the Base assembly.
Place the open end of the hose in a container to receive oil spillage.
4. Remove the setscrew or hex bolt in the cylinder upper leg clevis
(otherwise known as the Trunnion clevis).
5. Secure the cylinder from dropping on the floor. Remove the cylinder pin
from the upper leg clevis.
6. Lift the cylinder out of the leg assembly.
7. Push the piston rod into the cylinder to eject as much oil as possible into a container.
NOTICE
Summary of Contents for PLTC-58120
Page 13: ...13 1 DECAL_CAPACITY 2 36430050 3 36401487 4 36401560 5 06100010...
Page 14: ...14 6 36403225 7 36400265 8 36400257 9 36403720 10 36433670...
Page 17: ...17 PLT Pit Detail See Pit Installation Notes...
Page 19: ...19 Lifting and Installation...
Page 22: ...22 4 6 Bridge Lifting Chain Installation Steel Bridge...
Page 23: ...23 4 7 Bridge Lifting Chain Installation Aluminum Bridge...
Page 24: ...24 4 8 Bridge Winch Installation Steel Bridge...
Page 25: ...25 4 9 Bridge Winch Installation Aluminum Bridge...
Page 26: ...26 4 10 Pit Modification Installation for Mechanical Wheel Chock...
Page 30: ...30 Figure 6 1...
Page 35: ...35 Figure 6 3 Cylinder Seals...
Page 39: ...39 Electric Schematic 5HP 3Ph Continuous Running Vertical Power Unit...
Page 40: ...40 Electric Schematic 5HP 1Ph 230V Vertical Power Unit...
Page 41: ...41 Electric Schematic 3HP 1Ph 115V Vertical Power Unit...
Page 42: ...42 Hydraulic Schematic Contractor Power Unit...
Page 43: ...43 Hydraulic Schematic Vertical Power Unit...
Page 44: ...44 Hydraulic Schematic Continuous Running Vertical Power Unit...
Page 45: ...45 Push Button Wiring Diagram...
Page 46: ...46 Guarded Foot Switch Wiring Diagram...
Page 47: ...47 Guarded Foot Switch Assembly...
Page 48: ...48 Optional Limit Switch Mounting Diagram PLTC 6050 to 6060...
Page 49: ...49 Optional Limit Switch Mounting Diagram PLTC 6070 to 58150...
Page 54: ...54 7 PARTS LISTS Contractor Power Unit...
Page 55: ...55 Vertical Power Unit...