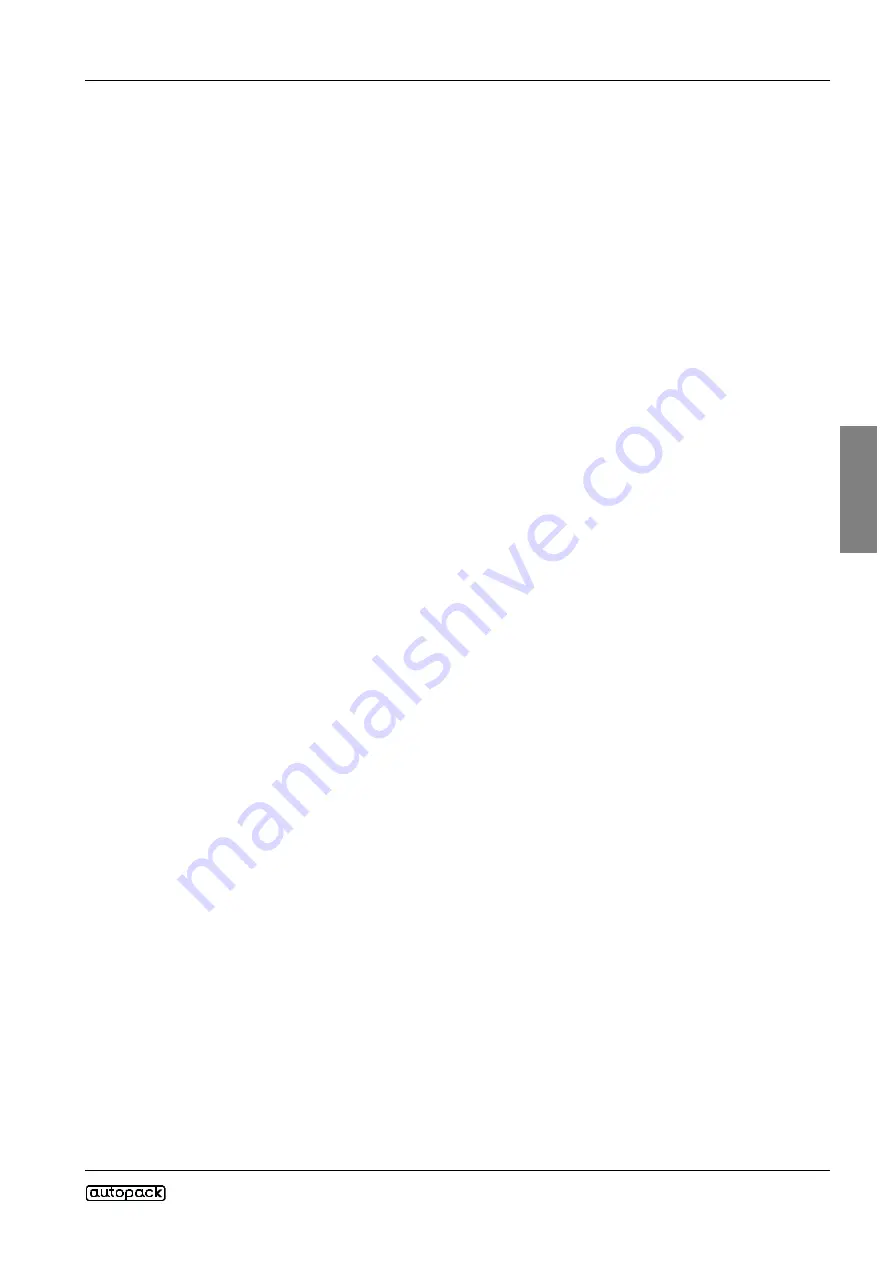
5 Electrical Components
5 - 15
5
•
T9-G910
Power 24VDC
•
T9-K510
Element Shrink Unit380VAC main supply
(208VAC main supply)
•
T9-K520
Element Shrink Unit (380VAC main supply, THX,
208VAC main supply, THX)
•
T9-K910
Main Power Supply, Wrapper Unit
•
T9-K911
Phase Indicator (UPS)
•
T9-K511
Element Shrink Tunnel
•
T9-K512
Element Shrink Tunnel
•
T9-K521
Element Shrink Tunnel (THX)
•
T9-K522
Element Shrink Tunnel (THX, Side Cabinet)
•
T9-Q910
Main Switch
•
T9-H910
Main Switch On lamp
•
T9-Q510
Main Fan Shrink Tunnel, Left (380VAC main supply,
208VAC main supply)
•
T9-Q520
Main Fan Shrink Tunnel, Right (380VAC main supply, THX,
208VAC main supply, THX)
•
T9-R610
Adjust Speed Conveyor (Standard)
•
T9-S910
Emergency Stop Knob, Left (Standard)
•
T9-S911
Emergency Stop Knob, Right (Standard)
•
T9-M910
Cooling Air Outlet
•
T9-U610
Speed Control, Tunnel Conveyor (Danfoss)
•
T9-X910
Main terminal supply
•
T9-X911
Motor&Heater supply (Standard)
•
T9-X912
Control supply (Standard)
•
T9-X913
Main terminal supply (UPS)
Summary of Contents for 45TLW20VL
Page 4: ...1 2 1 Introduction 1 This page intentionally left blank...
Page 6: ...1 4 1 Introduction 1 This page intentionally left blank...
Page 11: ...2 1 2 2 Safety precautions...
Page 12: ...2 2 2 Safety precautions 2 This page intentionally left blank...
Page 14: ...2 4 2 Safety precautions 2 This page intentionally left blank...
Page 26: ...2 16 2 Safety precautions 2 This page intentionally left blank...
Page 27: ...3 1 3 3 Installation...
Page 28: ...3 2 3 Installation 3 This page intentionally left blank...
Page 30: ...3 4 3 Installation 3 This page intentionally left blank...
Page 37: ...4 1 4 4 Maintenance...
Page 38: ...4 2 4 Maintenace 4 This page intentionally left blank...
Page 51: ...4 Maintenance 4 15 4 Figure 01 Example of Function Code Data Changing Procedure...
Page 55: ...4 Maintenance 4 19 4 To move cylinder unlock screw 4...
Page 56: ...4 20 4 Maintenace 4...
Page 57: ...4 Maintenance 4 21 4 4 7 Knife Replacement...
Page 58: ...4 22 4 Maintenace 4 4 8 Welding Bar Heater Assembly Replacement...
Page 66: ...4 30 4 Maintenace 4...
Page 67: ...4 Maintenance 4 31 4...
Page 68: ...4 32 4 Maintenace 4...
Page 69: ...4 Maintenance 4 33 4...
Page 70: ...4 34 4 Maintenace 4...
Page 71: ...5 1 5 5 Electrical Components...
Page 72: ...5 2 5 Electrical Components 5 This page intentionally left blank...
Page 74: ...5 4 5 Electrical Components 5 This page intentionally left blank...
Page 79: ...5 Electrical Components 5 9 5 5 2 Electrical system description 5 2 1 Safety system...
Page 80: ...5 10 5 Electrical Components 5 This page intentionally left blank...
Page 81: ...5 Electrical Components 5 11 5 This page intentionally left blank...
Page 86: ...5 16 5 Electrical Components 5 5 4 Electrical Component 5 4 1 Wrapper Top view Side view...
Page 91: ...6 1 6 6 Spare Parts...
Page 92: ...This page intentionally left blank...
Page 94: ...6 4 Assembly drawing WEL13261 Graphic ID WEL13261 eps Parent Drw WEL13261 dwg KNIFE ASSEMBLY...
Page 98: ...6 8 Assembly drawing SHRINK TUNNEL SPARE PARTS...
Page 100: ...6 10 Assembly drawing Electrical Spear parts Wrapper...
Page 103: ...6 13 Assembly drawing This page intentionally left blank...
Page 104: ...6 14 Assembly drawing Electrical Spear parts Tunnel...
Page 107: ...7 1 7 7 Human Machine Interface...
Page 108: ...7 2 7 HMI operation 7 This page intentionally left blank...
Page 110: ...7 4 7 HMI operation 7 This page intentionally left blank...
Page 119: ...8 1 8 8 Diagrams Drawings...
Page 120: ...8 2 8 Diagrams Checks 8 This page intentionally left blank...
Page 121: ...This page intentionally left blank...
Page 122: ...This page intentionally left blank...