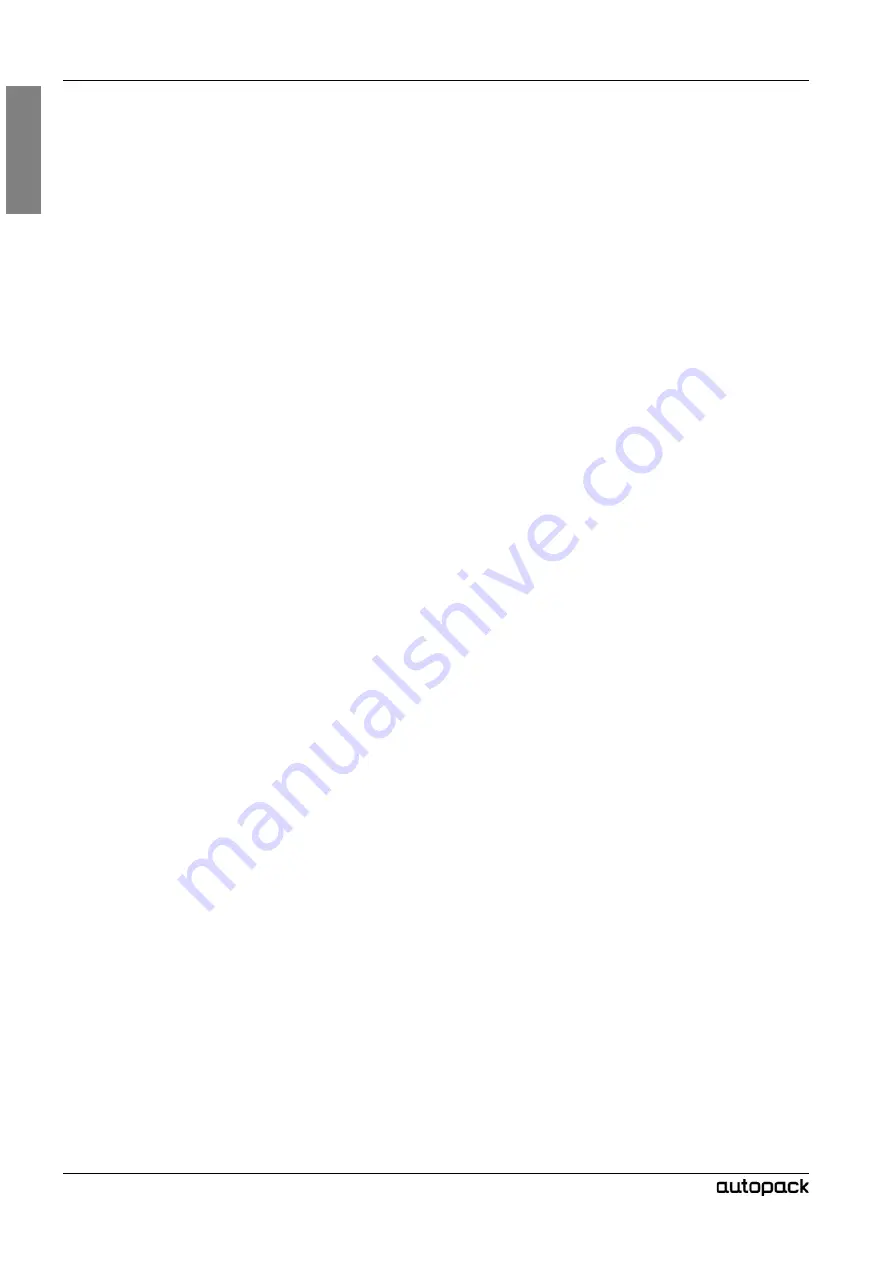
1-6
1 Introduction
1
1.2 Machine introduction
General Information
Sleeve Wrappers
AUTOPACK series of Sleeve Wrappers, covers a family of Fully Automatic
machines designed for collating product into a desired formation, then wrapping in a
sleeve of shrinkable film. The machines are of simple modular design which permits
customizing to suit user requirements. A number of options is available which can
be installed even after the machine has been put to use.
•
Oval bottle wrapping option (WLO)
This machine has a specifically designed infeed and grouping section to enable
fast and effecient handling of oval shaped products resulting in attractive and
tight packs.
Note!
For best results AUTOPACK Sleeve Wrappers should be matched with
AUTOPACK Shrink Tunnels to form high efficiency shrink Packaging
Systems of unequalled versatility.
Shrink Tunnels
AUTOPACK Shrink Tunnels are available in three basic models:
•
Short length tunnel
(
TLX
) designed for slower pharmaceutical and cosmetic
packing lines or label shrinking.
•
Medium to high speed general purpose tunnels (TMX)
suitable for most
shrink packaging applications
•
Long series, heavy duty tunnels (THX)
, applicable at all speeds where
thicker films and heavy packs are used.
The machines are of simple modular design permitting customized user application
requirements. AUTOPACK Shrink Tunnels have a number of operating features
which are not normally found on similar type equipment. These are:
– Quiet and efficient operation
– Small external size compared to product handling capacity
– Symmetrical, fixed air flow pattern
– Drop down bottom for easy cleaning
– Cooling station with a roller accumulation conveyor
Because of its unique air flow, AUTOPACK tunnels can be used with a variety of
films and machines such as L bar sealers, flow wrappers, but the airflow symmetry
really excess with Sleeve Wrapped product, resulting in tight, unique form pack with
small holes on either side.
1.2-1
System Used
For Wrapper
a) Control System - PLC control Inductive proximity sensors. Some models have
simple relay control option.
b) Welding Bar Motion - Pneumatic cylinder activation of welding bar and rear
pack clamp.
c)
Product Pusher and Lifter if fitted - Pneumatically operated, and guided units
with clip in product plates. This allows for quick change of product and pack
size.
Summary of Contents for 45TLW20VL
Page 4: ...1 2 1 Introduction 1 This page intentionally left blank...
Page 6: ...1 4 1 Introduction 1 This page intentionally left blank...
Page 11: ...2 1 2 2 Safety precautions...
Page 12: ...2 2 2 Safety precautions 2 This page intentionally left blank...
Page 14: ...2 4 2 Safety precautions 2 This page intentionally left blank...
Page 26: ...2 16 2 Safety precautions 2 This page intentionally left blank...
Page 27: ...3 1 3 3 Installation...
Page 28: ...3 2 3 Installation 3 This page intentionally left blank...
Page 30: ...3 4 3 Installation 3 This page intentionally left blank...
Page 37: ...4 1 4 4 Maintenance...
Page 38: ...4 2 4 Maintenace 4 This page intentionally left blank...
Page 51: ...4 Maintenance 4 15 4 Figure 01 Example of Function Code Data Changing Procedure...
Page 55: ...4 Maintenance 4 19 4 To move cylinder unlock screw 4...
Page 56: ...4 20 4 Maintenace 4...
Page 57: ...4 Maintenance 4 21 4 4 7 Knife Replacement...
Page 58: ...4 22 4 Maintenace 4 4 8 Welding Bar Heater Assembly Replacement...
Page 66: ...4 30 4 Maintenace 4...
Page 67: ...4 Maintenance 4 31 4...
Page 68: ...4 32 4 Maintenace 4...
Page 69: ...4 Maintenance 4 33 4...
Page 70: ...4 34 4 Maintenace 4...
Page 71: ...5 1 5 5 Electrical Components...
Page 72: ...5 2 5 Electrical Components 5 This page intentionally left blank...
Page 74: ...5 4 5 Electrical Components 5 This page intentionally left blank...
Page 79: ...5 Electrical Components 5 9 5 5 2 Electrical system description 5 2 1 Safety system...
Page 80: ...5 10 5 Electrical Components 5 This page intentionally left blank...
Page 81: ...5 Electrical Components 5 11 5 This page intentionally left blank...
Page 86: ...5 16 5 Electrical Components 5 5 4 Electrical Component 5 4 1 Wrapper Top view Side view...
Page 91: ...6 1 6 6 Spare Parts...
Page 92: ...This page intentionally left blank...
Page 94: ...6 4 Assembly drawing WEL13261 Graphic ID WEL13261 eps Parent Drw WEL13261 dwg KNIFE ASSEMBLY...
Page 98: ...6 8 Assembly drawing SHRINK TUNNEL SPARE PARTS...
Page 100: ...6 10 Assembly drawing Electrical Spear parts Wrapper...
Page 103: ...6 13 Assembly drawing This page intentionally left blank...
Page 104: ...6 14 Assembly drawing Electrical Spear parts Tunnel...
Page 107: ...7 1 7 7 Human Machine Interface...
Page 108: ...7 2 7 HMI operation 7 This page intentionally left blank...
Page 110: ...7 4 7 HMI operation 7 This page intentionally left blank...
Page 119: ...8 1 8 8 Diagrams Drawings...
Page 120: ...8 2 8 Diagrams Checks 8 This page intentionally left blank...
Page 121: ...This page intentionally left blank...
Page 122: ...This page intentionally left blank...