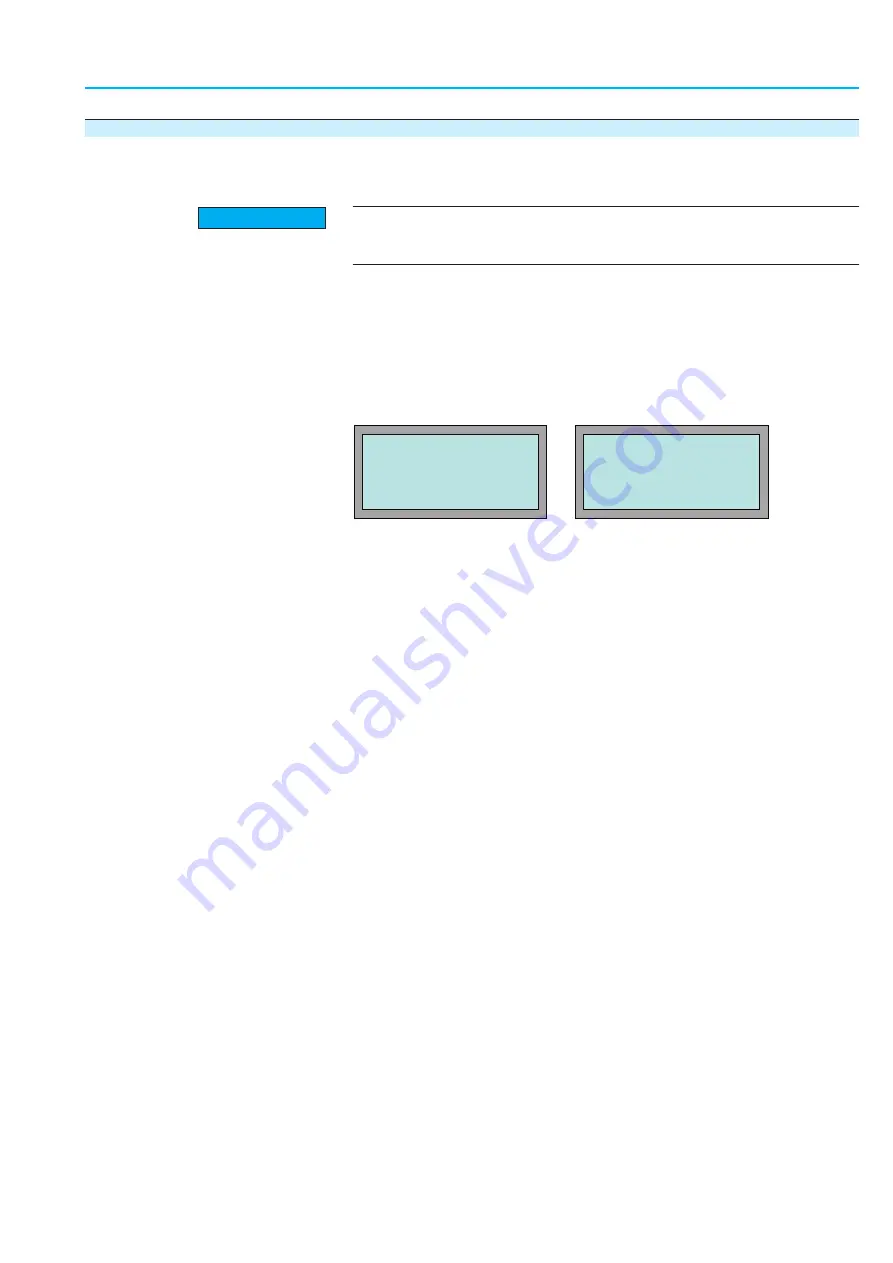
7.2
Torque switching: check/set
This setting is only possible for the non-intrusive version.
For further information refer to page 8.
Æ
Via the menu to parameter:
MAIN MENU (M0)
SETTINGS (M1)
TORQUE (M12)
OPENING (M1210)
CLOSING (M1211)
Default value:
according to order data
Setting range:
according to torque setting range
refer to actuator name plate
Information
The value can be displayed in percent, Newtonmeter (Nm), or in Lbs/ft.
To change the display unit, refer to page 16.
To display in percent:
100 % equals the max. torque indicated on the name plate of the actuator.
Example:
SA 07.5 with 20 – 60 Nm:
100 % = 60 Nm
33 % = 20 Nm
Information
The following fault signals are sent if torque setting performed has been
reached in mid-travel:
.
Status indication
S0
: operation mode OFF/LOCAL =
FLT + NR
.
Status indication
S0/S6
: operation mode REMOTE =
FAULT IND.
.
Status indication
S1
:
TORQUE FAULT (OPEN)
or
TORQUE FAULT
(CLOSE)
(torque fault)
.
The Foundation Fieldbus APVB transducer block signals a fault via
XD_ERROR (General Error, 17 (0x11)) and XD_ERROR_EXT (Torque
fault OPEN, 0x00000001 or Torque fault CLOSE, 0x00000002), thus
generating an operation mode change of the DOFB or AOFB to the IMan
status.
The fault has to be acknowledged before the operation can be resumed.
The acknowledgement is made:
1. either by an operation command in the opposite direction.
–
For
TORQUE FAULT (CLOSE)
: Operation command in direction
OPEN
–
For
TORQUE FAULT (OPEN)
: Operation command in direction
CLOSE
2. or, in case the torque present is smaller than the preset tripping torque:
–
via the Reset push button in selector switch position LOCAL.
–
via the APPLICATION_RESET Foundation Fieldbus parameter of the
APVB transducer block (index 784).
41
Actuator controls
Manual
AUMATIC AC 01.1/ACExC 01.1 Foundation Fieldbus
Valve damage due to incorrect setting!
Ò
The torque must suit the valve.
Ò
Only change the setting with the consent of the valve manufacturer.
EDIT
M1211
CLOSING
100%
:EDIT
↵
:OK
C:ESC
EDIT
M1210
OPENING
100%
:EDIT
↵
:OK
C:ESC
NOTICE